Reviewed by Mila PereraSep 23 2022
A group of scientists from the National Institute of Standards and Technology (NIST), Argonne National Laboratory, and the University of Wisconsin-Madison has pinpointed a specific 17-4 steel composition that equaled the properties of the traditionally produced version when printed.
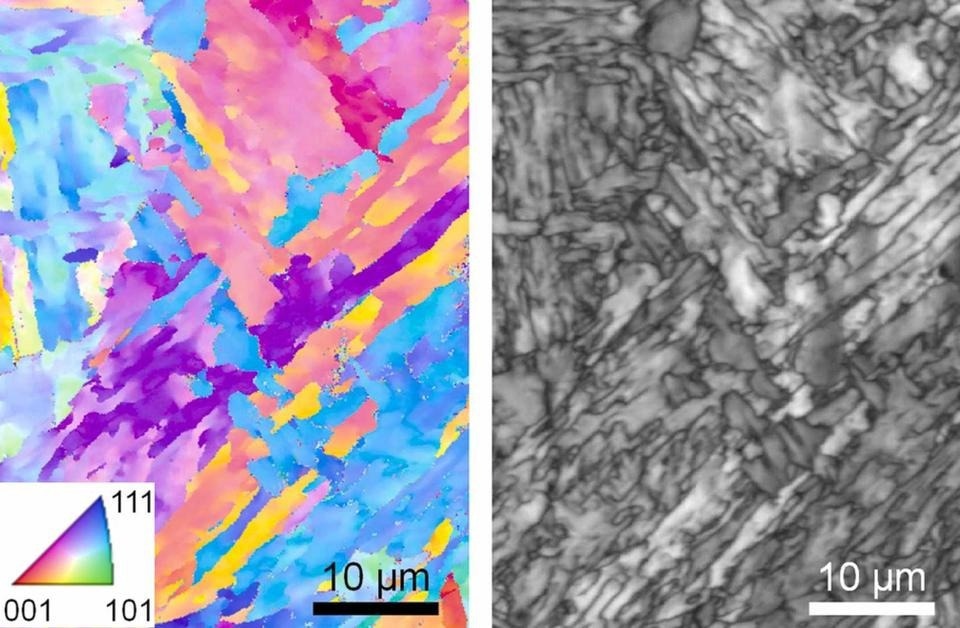
A microscopic image of 3D-printed 17-4 stainless steel. The colors in the left-side version of the image represent the differing orientations of crystals within the alloy. Image Credit: NIST
Strength and durability are vital for cargo ships, airliners, nuclear power plants, and other crucial technologies. This is why they harbor a spectacularly robust and corrosion-resistant alloy known as stainless steel (17-4 precipitation hardening (PH). For the first time, 17-4 PH steel can be reliably 3D-printed while keeping its advantageous properties.
Researchers developed their technique using high-speed data about the printing process, acquired with high-energy X-Rays from a particle accelerator. The study was published in the journal Additive Manufacturing.
The observations could help producers of 17-4 PH parts use 3D printing to lower costs and enhance their manufacturing versatility.
3D printing has advantages over traditional manufacturing; however, 3D printing of certain materials produces results incompatible with specific applications.
Printing metals is complex because the temperatures shift quickly during the process.
When you think about additive manufacturing of metals, we are essentially welding millions of tiny, powdered particles into one piece with a high-powered source such as a laser, melting them into a liquid and cooling them into a solid.
But the cooling rate is high, sometimes higher than one million degrees Celsius per second, and this extreme nonequilibrium condition creates a set of extraordinary measurement challenges.
Fan Zhang, Study Co-Author and Physicist, National Institute of Standards and Technology
According to Zhang, the organization or crystal structure of the atoms within the material alters quickly and is challenging to pinpoint due to its rapidly changing temperature.
Investigators have struggled to 3D-print 17-4 PH, a material with a crystal structure that must be precisely correct to display its highly desired properties.
This is because they do not understand what happens to the steel’s crystal structure as it is printed.
The researchers intend to explain what transpires during rapid temperature fluctuations and identify a strategy for accelerating the internal structure’s transition.
The scientists required specialized equipment to capture profound structural changes in milliseconds. They discovered synchrotron X-Ray diffraction (XRD, to be the ideal technique for the job.
In XRD, X-Rays interact with a material and will form a signal that is like a fingerprint corresponding to the material’s specific crystal structure.
Lianyi Chen, Study Co-Author and Professor, Mechanical Engineering, University of Wisconsin-Madison
The researchers smashed high-energy X-Rays into steel samples while printing at the Advanced Photon Source (APS), a robust light source at the Department of Energy’s Argonne National Laboratory.
The authors depicted the evolution of the crystal structure during a print, demonstrating how elements within their control, such as the metal powder's composition, affected the entire process.
Even though iron is the key component of 17-4 PH steel, the alloy’s composition might have various chemical elements.
The researchers had a vivid picture of the structural dynamics during printing. They tweaked the steel's makeup to identify a set of compositions that worked, including nickel, iron, niobium, copper, and chromium.
Composition control is truly the key to 3D-printing alloys. By controlling the composition, we are able to control how it solidifies. We also showed that, over a wide range of cooling rates, say between 1,000 and 10 million degrees Celsius per second, our compositions consistently result in fully martensitic 17-4 PH steel.
Fan Zhang, Study Co-Author and Physicist, National Institute of Standards and Technology
Some compositions formed strength-inducing nanoparticles that, under the old method, required the steel to be cooled and then reheated.
3D printing could allow manufacturers to reduce the need for special equipment, high production costs, and additional time.
Mechanical testing revealed that the 3D-printed steel had the same strength as conventionally made steel due to its martensite structure and strength-inducing nanoparticles.
The study could be influential beyond 17-4 PH steel. The information obtained from the XRD-based method might be used to develop and test computer models intended to forecast printed items' quality and optimize other alloys for 3D printing.
Chen says, “Our 17-4 is reliable and reproducible, which lowers the barrier for commercial use. If they follow this composition, manufacturers should be able to print out 17-4 structures that are just as good as conventionally manufactured parts.”
A 3D printer of the laser powder-bed fusion type, in action. Laser powder-bed fusion adds successive layers of metal powder and then uses a laser to melt each layer into place on the part being created. Video Credit: National Institute of Standards and Technology.
Journal Reference
Guo, Q., et al. (2022) Phase transformation dynamics guided alloy development for additive manufacturing. Additive Manufacturing. doi.org/10.1016/j.addma.2022.103068.