A paper recently published in the journal Additive Manufacturing demonstrated freeform injection molding (FIM) of functional ceramics using hybrid additive manufacturing (AM).
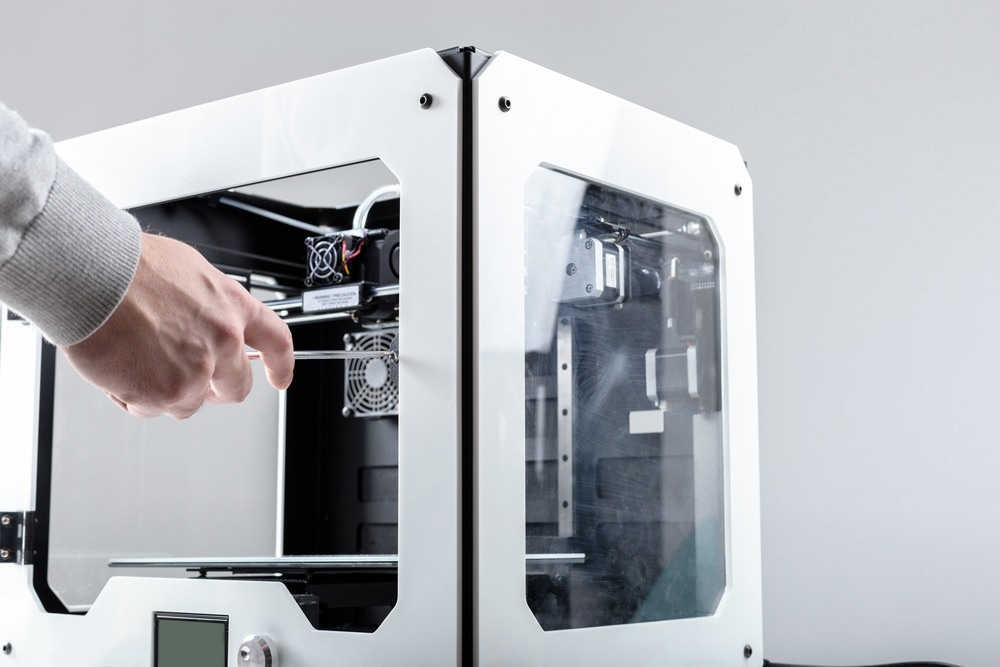
Study: Freeform injection molding of functional ceramics by hybrid additive manufacturing. Image Credit: FabrikaSimf/Shutterstock.com
Background
Functional ceramic materials, such as piezoelectric ceramic materials, have gained considerable attention for advanced applications, such as acoustic wave transducers and sensors. Functional ceramics are also used in energy applications and catalysis due to their superior thermo-mechanical properties and energy dissipation.
Although high-performance ceramics are used in several critical applications, conventional ceramics processing approaches have limited ability to process ceramics with complex geometries due to the use of high sintering temperatures to consolidate ceramics, which creates severe residual and thermomechanical stress.
Ceramic injection molding (CIM) is a common ceramic forming method used to produce ceramic parts with complex shapes due to its accuracy, reproducibility, and high production volumes. However, mold machining the metallic blocks are time-consuming and expensive, specifically when advanced components and mold designs, such as inserts and cooling channels, are needed for complex shapes.
In the past few years, several AM/three-dimensional (3D) printing methods, such as digital light processing (DLP), stereolithography (SLA), and fused deposition modeling, were introduced to fabricate ceramics with complex shapes. The use of AM methods for ceramic processing can expand the use of ceramic materials to new applications, such as radio frequency communications, photocatalysis, and heat management.
AM methods can be used with conventional ceramic forming processes such as CIM to develop robust and sustainable methods to process ceramics with complex shapes. Previous studies have demonstrated that hybrid processes can produce structures with finer features. However, these processes use molding or gel-casting at low pressures and temperatures and require a considerable time to cure the ceramic formulation.
The Study
In this study, researchers combined AM and CIM into a single hybrid process, referred to as FIM, to exploit the benefits of both CIM and AM. In this hybrid method, a photopolymer material formulation was 3D-printed into a sacrificial thermosetting polymeric mold, which was chemically dissolved after CIM.
The process yielded waste savings and geometrical capabilities of 3D printing and material forming characteristics and versatility of CIM. Researchers also analyzed the ability of FIM to process different ceramic feedstocks and evaluated the samples of different geometries with rising geometrical complexity.
Alumina, zirconia, and lead-free piezoelectrics, including barium titanate and bismuth sodium barium titanate, were used as feedstocks in this study. Several functional ceramics were processed into complex geometries. Freeform/periodic features, such as double helix and cylindrical lattice, and curved surfaces, such as lens and dome, were fabricated using alumina and yttria-stabilized zirconia commercial feedstocks, respectively.
Critical analysis was conducted to identify strategies for modeling and processing and gate positions to prevent defects and produce finer geometries. Volumetric deviation and computed tomography (CT) scanning were used to relate the inner defects and 3D structures with every processing step.
Injection molding simulations were used to optimize the processing parameters. The FIM-fabricated ceramic part quality was evaluated by investigating the geometrical features, macro-defects, and microstructure of the structural ceramics and the piezoelectric performance of barium titanate and bismuth sodium barium titanate. Researchers also assessed the effect of sintered- and green-density, shape distortion, and linear shrinkage.
Observations
FIM of functional ceramic materials, including piezoceramics, alumina, and zirconia, was demonstrated successfully. Molding these functional ceramics is typically challenging owing to ultraviolet light scattering issues.
Several complex and simple geometries were sintered effectively. Layered defects, such as cracks and delaminations, were not observed in the fabricated ceramic samples. These defects are common in ceramic structures 3D-printed using FDM, SLA, and DLP methods.
Anisotropic shrinkage and inter-layer adhesion issues were also eliminated using this hybrid AM technique. A proper outlet and gate position design in the FIM mold prevented the weak point formation in the green state and reduced the cracks from the mold expansion during dissolution.
The melt front fusion in the ceramic feedstock was controlled properly during the injection by tuning the feedstock packing, pressure, and temperature. Complex shapes were fabricated using the full dissolution method, where the mold was fully dissolved, and the ceramic part was obtained. The green-ceramic strength during this process was primarily influenced by the design and quality of the injection.
The linear shrinkage value matched the material specifications during the consolidation and sintering of ceramics. A greater dimensional deviation was observed in the piezoelectric ceramic material-based feedstocks.
All ceramic parts demonstrated expected microstructures and grain growth after sintering. Samples with complex and simple geometries displayed isotropic shrinkage features for the complete sintered volume. Shape distortion with extreme dimensional deviations was only observed on small regions on the thinner parts and edges.
The piezoceramics demonstrated an electromechanical response even after processing, which indicated that their functionality was not affected by the geometries and the processing method. The processing parameters, including sintering and injection molding, were critical for the resulting density and defects, respectively, which influenced the electromechanical performance.
To summarize, the findings of this study demonstrated that hybrid AM-based FIM is a suitable, versatile, and fast approach for functional ceramic processing. The combination of electromechanical performance and complex geometries offers great potential for advanced applications.
More from AZoM: What is Glow Discharge Optical Emission Spectrometry?
Further Reading
Kyriakos Didilis, Debora Marani, Uffe Ditlev Bihlet, Astri Bjørnetun Haugen, Vincenzo Esposito. Freeform injection molding of functional ceramics by hybrid additive manufacturing. Additive Manufacturing 2022. https://www.sciencedirect.com/science/article/abs/pii/S2214860422005863
Disclaimer: The views expressed here are those of the author expressed in their private capacity and do not necessarily represent the views of AZoM.com Limited T/A AZoNetwork the owner and operator of this website. This disclaimer forms part of the Terms and conditions of use of this website.