Using a novel technique for defect detection, researchers from EPFL have settled a long-running dispute over laser additive manufacturing procedures.
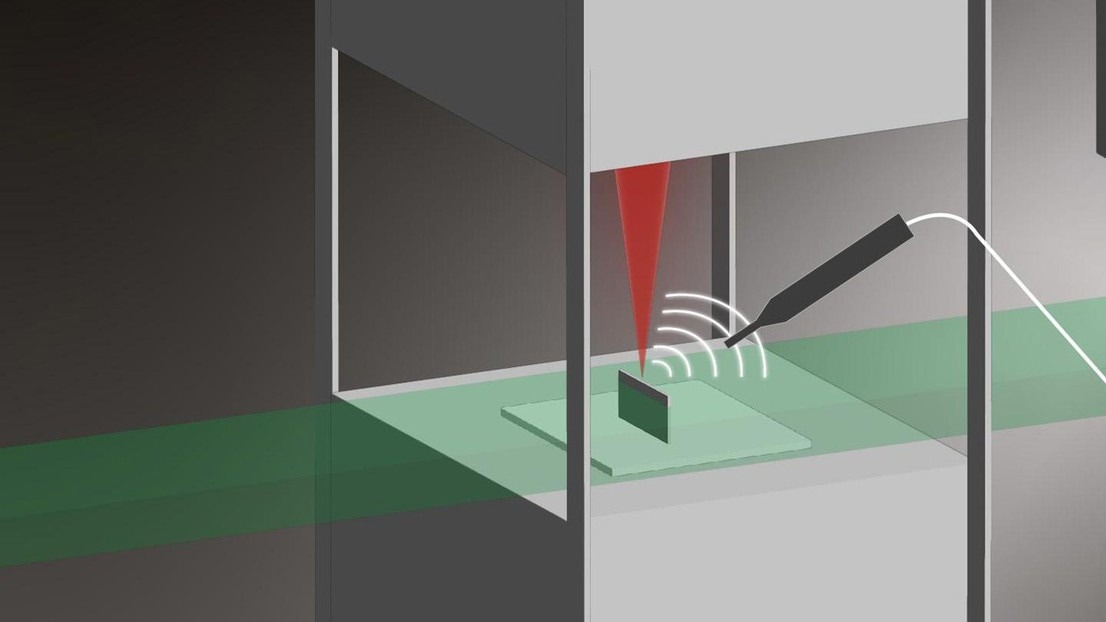
A graphic representation of the experimental setup for listening for printing defects. Image Credit: EPFL/Titouan Veuillet
Unexpected flaws have frequently slowed the advancement of laser additive manufacturing, which 3D prints metallic items using powders and lasers. Conventional monitoring techniques, such as thermal imaging and machine learning algorithms, have demonstrated serious drawbacks.
They frequently fail to see flaws or misunderstand them, which makes precision manufacturing difficult to use and excludes the process from crucial sectors like the automobile and aerospace industries.
However, what if it were feasible to identify flaws in real-time by comparing the sounds produced by the printer when a print is perfect and one that has anomalies? This method of defect detection was thought to be unreliable up until now.
Nevertheless, this assumption has been successfully contested by scientists at EPFL’s School of Engineering’s Laboratory of Thermomechanical Metallurgy (LMTM).
There’s been an ongoing debate regarding the viability and effectiveness of acoustic monitoring for laser-based additive manufacturing. Our research not only confirms its relevance but also underscores its advantage over traditional methods.
Roland Logé, Professor and Head, Laboratory of Thermomechanical Metallurgy, EPFL
The industrial sector would benefit significantly from this research since it presents a novel yet affordable way to monitor and enhance the quality of goods produced using laser powder bed fusion (LPBF).
The synergy of synchrotron X-ray imaging with acoustic recording provides real-time insight into the LPBF process, facilitating the detection of defects that could jeopardize product integrity.
Dr. Milad Hamidi Nasab, Study Lead Researcher and Scientist, EPFL
These improvements increase the reliability and security of manufactured goods while also producing considerable cost savings in an era where companies are always striving for efficiency, accuracy, and waste reduction.
How Does LPBF Manufacturing Work?
A state-of-the-art technique called LPBF is changing the way metal is manufactured. In essence, it precisely melts tiny metal particles with a high-intensity laser, building layer upon layer to create intricate 3D metallic structures. Consider LPBF as the more sophisticated, metallic equivalent of a traditional 3D printer. It uses a small coating of microscopic metal powder, which can range in size from that of human hair to that of a fine grain of salt (15–100 μm), in place of melted plastic.
Using a computerized blueprint as a guide, the laser travels across this layer, melting particular patterns. With this method, custom, intricate pieces with minimum waste, such as lattice structures or unique shapes, can be manufactured. However, there are several difficulties with this potential approach.
The metal powder changes phases between liquid, vapor, and solid as the laser interacts with it, forming a melt pool. The technique may occasionally malfunction because of factors like the angle of the laser or the existence of particular geometrical characteristics in the powder or component.
These events are referred to as “inter-regime instabilities” because they can occasionally cause transitions between the "conduction" and “keyhole” regimes, two different melting processes.
In unstable keyhole regimes, pockets of porosity can develop as a result of the molten powder pool going deeper than planned, which might lead to structural defects in the final product. The Image Analysis Hub of the EPFL Center for Imaging developed a method that makes it simpler to visualize minor changes associated with the liquid metal and a tool for annotating the melt pool geometry to enable the assessment of the width and depth of the melt pool in X-Ray images.
Detecting These Defects Using Sound
The EPFL team developed an experimental design in collaboration with the Paul Scherrer Institute (PSI) and the Swiss Federal Laboratories for Materials Science and Technology (Empa) that combined acoustic emission measurements with operando X-Ray imaging investigations. The studies were carried out using the miniature LPBF printer created by Dr. Steven Van Petegem’s group at the Swiss Light Source at PSI’s TOMCAT beamline.
Combining this with an extremely sensitive microphone within the printing chamber allowed for the immediate identification of production flaws by highlighting specific changes in the audio signal during regime transitions.
Giulio Masinelli of Empa, a signal processing specialist, introduced an adaptive filtering approach that represented a turning point in the study.
This filtering approach allows us to discern, with unparalleled clarity, the relationship between defects and the accompanying acoustic signature.
Giulio Masinelli, Doctoral Student, EPFL
In contrast to conventional machine learning methods, which are excellent at identifying patterns in statistical data but are frequently customized for particular use cases, this approach offers better temporal and geographical precision along with deeper insights into the physics of melting regimes.
EPFL makes a significant contribution to the field of laser additive manufacturing with this research. The results have great significance for prospective industrial uses, namely in fields such as precision engineering and aerospace. The study highlights the significance of consistent production procedures, hence reinforcing Switzerland's reputation for painstaking workmanship and manufacturing precision.
It also raises the possibility of early defect identification and rectification, which would improve product quality.
Logé concluded, “This research paves the way for a better understanding and refinement of the manufacturing process, and will ultimately lead to higher product reliability in the long term.”
Journal Reference
Nasab, M. H., et. al. (2023) Harmonizing sound and light: X-ray imaging unveils acoustic signatures of stochastic inter-regime instabilities during laser melting. Nature Communications. doi:10.1038/s41467-023-43371-3.