Sep 13 2007
University at Buffalo chemists have developed a novel way to grow chemically pure, zinc oxide thin films characterized by dense, bristle-like nanostructures and a new method for depositing them on temperature-sensitive substrates, including polymers, plastics and tapes.
The research, published online last month in the Journal of Physical Chemistry, may make possible the deposition of versatile zinc oxide films onto flexible surfaces, enabling the development of more efficient solar cells, liquid-crystal displays, chemical sensors and optoelectronic devices.
The issue of the journal commemorates the career of Richard E. Smalley, a pioneer of nanotechnology, with whom the lead UB author, James F. Garvey, Ph.D., professor of chemistry, worked while on sabbatical in 1995.
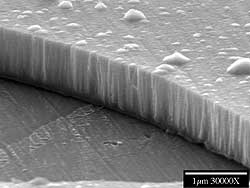
High-quality zinc oxide thin films are versatile and can be fabricated into many shapes, including films, nanorods and nanoparticles. However, there is a drawback: They usually are deposited at high temperatures, which can damage or even melt the substrate they are coating.
"That makes it impossible to coat plastic, a hard drive, an electronic device or even contact lenses since the deposition process damages the underlying surface," Garvey said.
By contrast, the UB researchers have developed a technique in which the metal oxide molecules are cool enough to safely coat temperature-sensitive substrates.
The UB researchers grow the thin films by first reacting zinc metal and oxygen in the presence of a high power, electrical arc discharge.
The method they developed, called Pulsed Arc Molecular Beam Deposition (PAMBD), strikes a discharge between two pure zinc rods.
"This lightening-like discharge creates a bright, blue plasma five times hotter than the surface of the sun," Garvey said.
At these high temperatures, the pure zinc metal is vaporized and reacts completely with an oxygen gas pulse to create chemically zinc oxide molecules.
The gaseous zinc oxide is then sprayed through a tiny aperture, a process that results in cooling the expanding gas down to about 50 degrees Kelvin, he explained, allowing the beam of now cold metal oxides to safely coat even the most temperature-sensitive surfaces.
"This is an enabling technology that will allow for the deposition of thin films on batteries, credit cards, on any flexible surface you have," Garvey said, adding that the UB process can use any metal and a wide array of different metal oxides can be produced easily.
"Since it is a pulsed technique, the thickness of the resulting films can be precisely controlled," he noted. "In this way, our PAMBD source is really a high-temperature chemical reactor that generates metal oxide molecules on demand and then rapidly cools them down for subsequent coating of any surface."
The chemists now are working with researchers in the UB Department of Physics to use the thin films and the deposition technique to create nanorods and spintronic devices.
In addition to Garvey, co-authors on the paper are Chi-Tung Chiang, Ph.D., post-doctoral associate, and Robert L. DeLeon, Ph.D., adjunct associate professor, both in the Department of Chemistry in the UB College of Arts and Sciences.