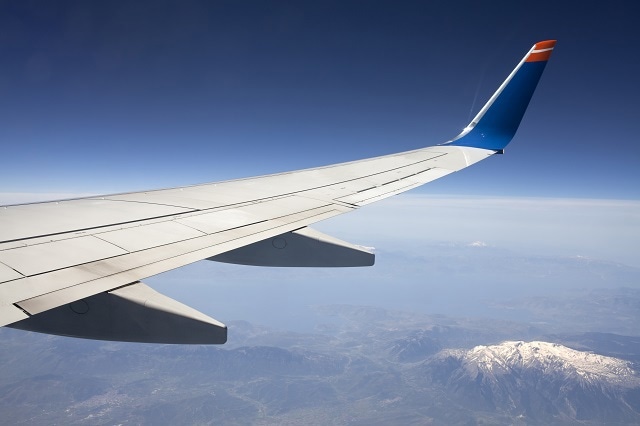
Image Credits: Maciej Bledowski/shutterstock.com
The design of an aircraft must take in consideration a multitude of factors such as efficiency, comfort, safety and reliability. However, the importance placed of each of these aspects entirely depends on the type of the aircraft being designed which can vary from fighter jets to commercial aeroplanes.
As a result, the design of the aircraft has to meet specific requirements which influence the complexity of its structure and the materials used in its construction. A wide range of materials may be used in the design of the aircraft to make use of properties such as strength, elasticity, specific weight and corrosion resistance.
Different materials can also be used in the design of specific parts of the aircraft, as a function of the initial requirements of the strength-to-weight ratio and the preferential directions of the applied loads.
Using Wood in the Design of the First Aircraft
Wood is one material which has mechanical and physical properties which meet the criteria required for the manufacture of aircraft components. This material possesses a high strength-to-weight ratio when used in laminate structures and is resistant to adverse environmental conditions if it is first subjected to a specific preservation treatment.
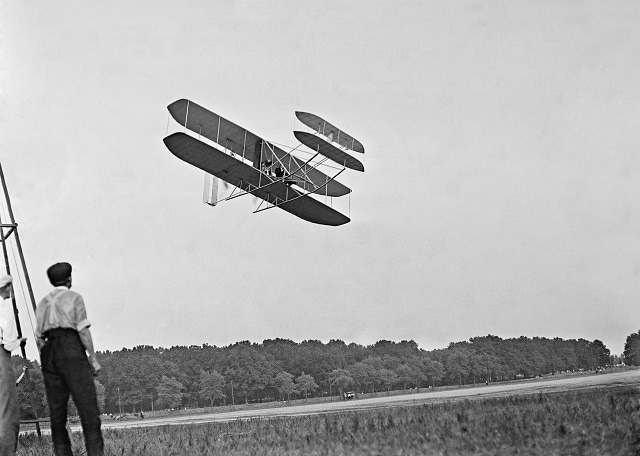
Image Credits: Everett Historical/shutterstock.com
Wood was the original material of choice in the construction of early aircraft but it is no longer used in modern aircraft as there are other available materials, both metallic and non-metallic, which have higher strength-to-weight ratios for lightweight and corrosion resistant structures.
The Introduction of Metals
The metals used in the aircraft manufacturing industry include steel, aluminium, titanium and their alloys. Aluminium alloys are characterised by having lower density values compared to steel alloys (around one third), with good corrosion resistance properties.
However, steel alloys have a greater tensile strength, as well as a higher elastic modulus. As a result, steel is used in the parts of aircraft for which strength is very important, such as in the design of landing gears.
Titanium is also used in the design of aircraft structures as it is a lightweight, strong and corrosion resistant metal. This material is employed in the manufacture some of the engine components, together with specifically designed heat resistant alloys, such as Nickel-based superalloys.
Composite Materials in the Aircraft Industry
In addition to metals, composite materials are also used within the aircraft industry due to their strength, relatively low weight and corrosion resistance. Composites are created by the combination of different materials, which have been selected on the basis of their structural properties.
They can be made of fibrous materials embedded within a resin matrix. In general, fibres oriented in a specific direction are laminated with fibres characterised by a different orientation in order to obtain the required strength and stiffness.
Composite materials are mainly used in the manufacture of modern aircrafts and their use has been gradually increasing over the last few years, leading to a decline in the use of metallic materials.
The Wings of a Modern Aircraft
The wings of a modern aircraft can be designed as a combination of different types of materials, depending on their specific structural function. The structure of the wing of an aircraft is comprised of several different elements, namely spars, skin and ribs, as well as control surfaces, such as ailerons and flaps.
Each of these components needs to support different loads and, thus, the right material needs to be selected. Steel and aluminium alloys can be used in the manufacture of ribs, whilst composite materials can be used in the design of the wing skin and the control surfaces.
Improving Aerodynamics and Fuel Efficiency
The material chosen in each application depends also on the type of aircraft which will be manufactured, with lighter materials such as composites being used in ultralight structures.
New materials are continuously being developed and tested, thanks to research projects which are focused on aircraft design, in order to improve aspects such as aerodynamic efficiency, fuel consumption and noise generation.
Several new concepts related to innovative wing shapes and materials are under development, focusing on reduction of drag and noise levels and potentially increasing the fuel efficiency.
It has been estimated that a 1% reduction of the amount of drag for a large transport aircraft can save up to 400,000 litres of fuel, thus reducing emissions by around 5000 kg.
The PrandtlPlane Configuration
An example of this is represented by the PrandtlPlane configuration, a closed-wing platform based on the concept of the ‘best wing system’ concept introduced by Ludwig Prandtl in 1924. According to this solution, a lifting system represented by a wing box in the front view is characterised, under specific conditions, by the minimum value of the induced drag.
PrandtlPlane Flight Tests n.1
Video Credit: PrandtlPlane Flight Tests - SkyBox Engineering/Youtube.com
Following the development of models and simulations on this concept, the research project IDINTOS has been carried out by a consortium of Italian public and private partners, resulting in the design and manufacture of an amphibious ultralight PrandtlPlane. Composite materials have been used in the entire structure of the aircraft prototype, from the fuselage to the innovative wing structure.
FlexFoil Wings
Another example of an innovative concept for the design of an aircraft wing has been developed by NASA in a joint project involving the US-based company FlexSys and the Air Force Research Laboratory.
The innovative design allows the profile of the wing to change during flight through a seamless flexible edge. Traditional flaps have been replaced by a shape morphing control surface with the capability to perform the large angular deformations required for landing and take-off.
The novel wing aerofoil, FlexFoil, uses the natural elasticity of aviation-grade materials due to a technology known as ‘distributed compliance’. The seamless structure integrates actuators and sensors, allowing large deformations with contained strains.
At last, a shape-morphing aircraft wing is here - no flaps
Video Credit: A shape-morphing aircraft wing - FlexSys K/Youtube.com
According to FlexSys, the shape-changing bird-like wing can increase fuel efficiency by up to 12% as well as reducing the noise on landing and take-off by up to 40%.
The experimental control surfaces have been integrated with an aircraft after six months of testing. The flight of this prototype has been realised for data collection purposes, with fixed flap angles ranging from -2 degrees to +30 degrees.
The Future of Aircraft Wing Design
The previous examples of novel concepts for the design of aircraft wings demonstrate that different types of materials may be used in the future as demand increases for lighter structures characterised by non-conventional aerodynamics and highly complex geometries.
However, the aerospace industry is underpinned by rigorous safety testing and regulations that must be applied to the innovative technologies which are continuously being developed. As a result, long periods of time often pass before a novel concept is introduced into the mainstream aircraft manufacturing industry, imposing strict limitations to the use of the next generation materials.
Sources and Further Reading
Disclaimer: The views expressed here are those of the author expressed in their private capacity and do not necessarily represent the views of AZoM.com Limited T/A AZoNetwork the owner and operator of this website. This disclaimer forms part of the Terms and conditions of use of this website.