Nov 28 2018
The skeleton of our infrastructure comprises mild and high strength low-alloy (HSLA) steel, which has an important role to play in construction industries today. This article will compare and contrast mild and HSLA steel properties, as well as common grades, to give you a complete profile of these categories of steel.
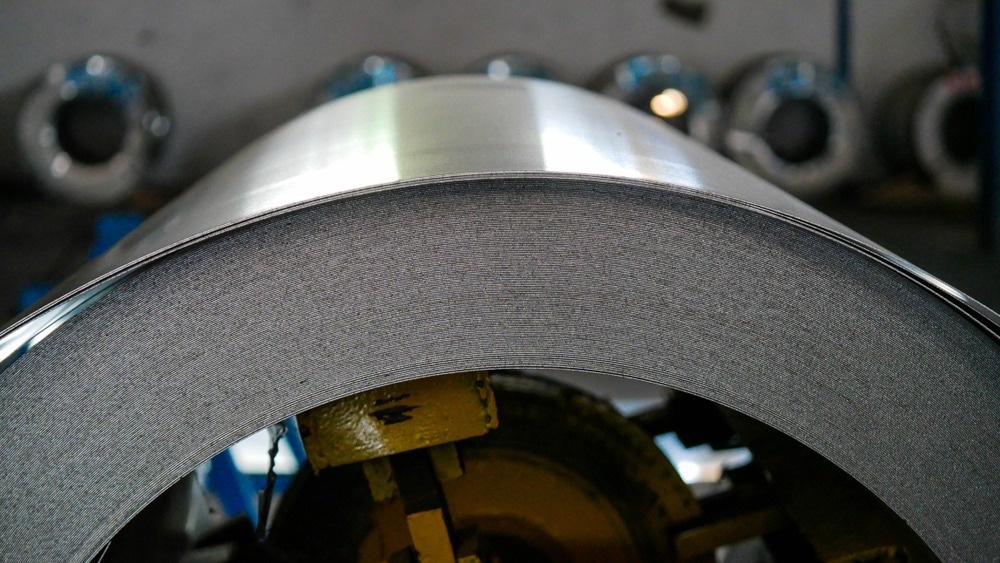
Image Credit: Nurihsan Hadad/Shutterstock.com
What is Mild Steel?
Mild steel is a type of carbon steel. Carbon and iron are the two main elements that make up steel, with a maximum carbon content of 2.1% of the material’s weight. Steel with such a carbon content is referred to as high-carbon steel (or carbon tool steel). High-carbon steel is incredibly hard, but also very brittle, thus making it extremely difficult to machine, cut, or bend. In other words, high-carbon steel is known to have low ductility.
Related: How Structural Steel is Produced
High carbon steel can be processed further to reduce carbon and increase ductility. On the other hand, medium carbon steel is material that contains approximately 0.3% to 0.6% carbon. While medium carbon steel has some applications, it still lacks ductility.
Finally, low-carbon (or mild) steel is made when up to 0.4% manganese is added. This increases the steel’s hardness while reducing the carbon content to 0.05%-0.25%, thus ensuring that the material is more ductile. Though low-carbon steel has modest ductility and is sensitive to atmospheric elements, it can be used in a variety of applications.
ASTM A36: The Core Mild Steel Grade
ASTM A36 is widely used across a variety of applications and is easily North America’s most common grade of structural steel.
A36 is produced by adding manganese, phosphorus, sulfur, silicon, and copper. When combined, these elements increase ductility (phosphorus and sulfur), hardness (manganese), and corrosion resistance (silicone and copper).
Element |
A36 |
Carbon |
0.25-0.29% |
Manganese |
0.80-1.2% |
Phosphorus |
0.03% |
Sulfur |
0.03% |
Silicon |
0.40% |
Copper |
0.20% |
A36 features reasonable strength, represented in the below table by yield, tensile and elongation.
Strength Point |
Min. Value |
Yield Point (psi) |
36,000 |
Tensile Strength (psi) |
58,000-80,000 |
Elongation % (200 mm) |
20% |
A36 features reasonable strength, represented in the below table by yield, tensile and elongation.
A36 ensures the right combination of hardness, ductility, durability, and price. As one of the most economical grades of steel available, A36 can be easily procured from mills, steel suppliers, and steel retailers.
What is HSLA Steel?
Mild steel can be transformed into high-strength low-alloy (HSLA) steel with the addition of a few alloys – such as phosphorus, sulfur, silicon, and molybdenum. HSLA boasts high strength, good machinability, and ductility, but significantly lower weight as compared to other materials with similar strength.
Related: The Chemistry Behind Low Carbon Alloy Steel
A large range of grades can be classified under HSLA steel, but there are three grades that mainly comprise a large percentage of HSLA steel demand in North America.
ASTM A572
Similar to A36, ASTM A572 is an economically priced – and therefore widely used – structural steel material. Used in infrastructure such as bridges, buildings, construction equipment, transmission towers, and more, A572 has a higher yield point and tensile strength than A36. Thus, it can bear more weight than A36.
Strength Point |
A572-50 |
A36 |
Yield Point (psi) |
50,000 |
36,000 |
Tensile Strength (psi) |
65,000 |
58,000-80,000 |
Elongation % (200 mm) |
18% |
20% |
What’s more, like A36, identical elements are added to achieve the material’s enhanced strength and hardness:
Element |
Grade 42 |
Grade 50 |
Grade 60 |
Grade 65 |
Carbon |
0.21% |
0.23% |
0.26% |
0.23-0.26% |
Manganese |
1.35% |
1.35% |
1.35% |
1.35-1.65% |
Phosphorus |
0.03% |
0.03% |
0.03% |
0.03% |
Sulfur |
0.03% |
0.03% |
0.03% |
0.03% |
Silicon |
0.15-0.40% |
0.15-0.40% |
0.40% |
0.40% |
A572 is available in multiple grades – four of which will be explored here – that offer varying strength and hardness. Of these, the most common is ASTM A572-50.
ASTM A656
The first grade of A572 is ASTM A656, which is an ideal HSLA steel choice for construction equipment, crane booms, truck frames and general fabrication, among other applications.
Comprising the common alloys added to A572 grades, ASTM A656 also includes vanadium, columbium, titanium, and nitrogen. The first three add strength and nitrogen helps add corrosion resistance.
Element |
% |
Carbon |
0.18% |
Manganese |
1.65% |
Phosphorus |
0.03% |
Sulfur |
0.03% |
Silicon |
0.60% |
Vanadium |
0.08-0.15% |
Nitrogen |
0.03% |
Columbium |
0.008-0.10% |
Titanium |
0-0.15% |
Compared to both A36 and A572, A656 has a higher yield point and tensile strength, thus making it perfect for load-bearing projects. However, this added strength means that A656 can cost more.
Strength Point |
A656-60 |
A572-50 |
Yield Point (psi) |
60,000 |
50,000 |
Tensile Strength (psi) |
70,000 |
65,000 |
Elongation % (200 mm) |
17% |
18% |
CSA G40.21
A widely used HSLA, CSA G40.21 steel is made to adhere to Canadian standards. Though it is similar to ASTM A572 in terms of yield point, tensile strength, and elongation, three grades of CSA G40.21 – 44W, 50W and 50A – have a chemical makeup that differs from G40.21’s American cousin.
Element |
Grade 44W |
Grade 50W |
Grade 50A |
Carbon |
0.22% |
0.23% |
0.02% |
Manganese |
0.5%-1.5% |
0.5%-1.5% |
0.75%-1.35% |
Phosphorus |
0.04% |
0.04% |
0.03% |
Sulfur |
0.05% |
0.05% |
0.04% |
Silicon |
0.04% |
0.04% |
0.15%-0.5% |
Chromium |
|
|
0.07% |
Nickel |
|
|
0.09% |
Copper |
|
|
0.2%-0.6% |
Other Less Common HSLA Steel Grades
HSLA steel is a large branch of the carbon alloy steel family. Here, five less commonly used HSLA grades are looked at, which are widely used across a variety of applications.
Grade |
Common Uses |
A709 |
Bridges. Available in standard grades and higher performance grades, specifically designed for extreme climates. A709 is also commonly purchased to meet AASHTO M270 standards. |
AASHTO M270 |
Bridges. M270 is very similar to A709, and also meets AASHTO’s specific standards. |
A588 & A606 |
Welded bridges and buildings, as well as general construction applications. The added advantage of these grades is their high degree of corrosion-resistance. |
A871 |
Tubular structures and poles. |
A573 |
Storage tanks. This grade is fully killed, and is perfectly suited to atmospheric conditions that require improved notch toughness. |
Performance Over Composition
No doubt that composition guidelines are important for HSLA steel grades, but it is the performance of the material that helps engineers determine the choice of HSLA steel for their specific project.
To determine the amount of energy a material can absorb at varying temperatures, charpy impact tests are conducted. This is an important test in the construction of bridges, especially in situations where the bridge may need to endure cold atmospheric conditions.
Other measurements that help engineers determine material need are yield point, tensile strength, and elongation percent. These measurements accurately identify the point at which the material will incur irreparable damage, the point where the material will fail, and the percentage difference between those two points.
After determining the material needs for a specific project, partnering with an experienced steel supplier – like Leeco Steel – will ensure the timely delivery of the desired material, along with documentation showing composition and performance.
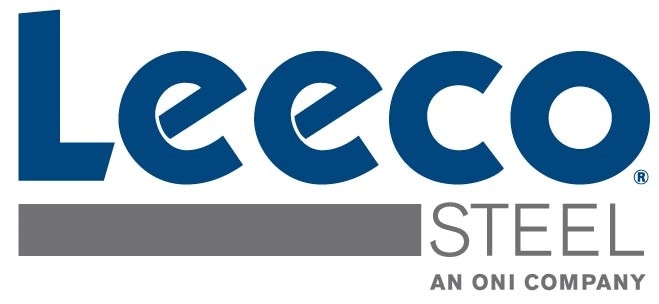
This information has been sourced, reviewed and adapted from materials provided by Leeco Steel, LLC.
For more information on this source, please visit Leeco Steel, LLC.