For the aerospace and power generation industries, the highest levels of radiographic quality are required to ensure the integrity of manufactured components such as turbine blades. At the moment such industries nondestructively test each component using X-ray film. Not only is this time consuming but also defect detection is not always reliably obtained. With the development of its new VENLO system, X-Tek industrial is hoping that the aerospace industry, for one, will move away from film altogether by using a system that not only reduces inspection times and ensures high productivity, but also provides resolutions that match existing film techniques. ‘We hope to capture 30-40% of the aerospace blade market,’ says Stephen Drake, Managing Director of X-Tek Industrial. ‘Its ability to achieve the same quality as fine grain film will hopefully encourage the aerospace industry to get rid of film.’
A Digital Alternative to X-Ray Film Non-Destructive Testing
Ideal for a broad range of NDT applications, the VENLO uses a choice of micro and mini-focal X-ray sources, and replaces X-ray film with an amorphous silicon detector. The detector has more than seven million elements and when used with the IMPS III software can achieve a contrast better than 1% and a dynamic range exceeding 4000:1. It has an area of 40cm x 30cm, and even at a resolution of 50 microns (5x resolution) it covers up to 8cm x 6cm of the component. The detector uses a custom Hi-Brite conversion screen with virtually zero burn.
Imaging Capabilities
All VENLO systems are fitted with a large component load tray of 40cm x 30cm, which is similar to a large film format. The mini-focus version can image components almost filling this entire area in a single exposure and produce results in a fraction of the time of film systems. The micro-focus versions have an X/Y motorised component tray enabling the entire imaging area to be covered and computer controlled at high magnification.
Benefits of the Digital X-Ray System
One of the first companies to take advantage of the benefits offered by the system is Eldim. The Netherlands-based manufacturer of precision aerospace and stationary gas turbine components has recently taken delivery of two VENLO systems to inspect its range of precision-drilled turbine blades, which vary in size from those for aero engines to much larger gas turbine blades for power generation. Until the installation of the VENLO machines, Eldim was using two Andrex systems for film radiography. ‘Using VENLO is going to save us a minimum of 100,000 euros in film and processing costs in the first year alone,’ says Harrie Martens, Quality Engineer at Eldim. ‘It is quicker to use than film, yet offers the same quality and resolution.’
X-ray inspection is essential for checking the cooling holes in turbine blades. When using film, it typically takes five minutes to expose each turbine blade and then a further 15-20 minutes to develop the film for inspection. The real time X-ray imaging of the VENLO produces an image within two minutes, offering huge cumulative savings in time and increased productivity. ‘By using digital radiography we have the information much faster so there are fewer production stops and there is better traceability of the images,’ adds Martens.
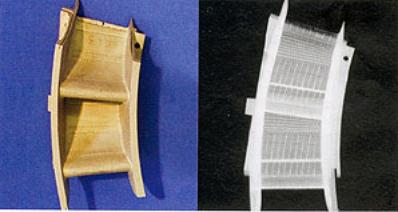
|
Figure 1. A turbine blade with cooling holes (left) and the x-ray image of the same turbine blade showing the holes (right).
|
Resolution of the Digital System Compared to the Film System
A key feature of the VENLO system is its genuine film quality resolution of the images produced. ‘We have extensively compared film samples with our digital results,’ says Steve Alderton, Sales Engineer at X-Tek Industrial. ‘The contrast, resolution and detectability of fine cracks using the digital system compares favourable with the film samples.’ This was essential for Eldim’s own quality control and that of its aero engine and power turbine OEM (original equipment manufacturers) customers.
Penetration Levels
Available either as a vacuum de-mountable microfocus system for the detection of the finest defects, or as a constant potential, sealed-tube system for maximum productivity, VENLO can be supplied with a choice of three penetration levels as standard - 160kV 225kV and 320kV The 320kV X-ray gun featured in the top-of-the range model chosen by Eldim, is claimed by X-Tek Industrial to be the highest powered system of its type available anywhere in the world, allowing engineers to accurately view inside denser materials and thicker components than ever before.
Design Features of the Digital X-Ray System
The VENLO series has been designed for ease of use and high productivity while meeting the most stringent safety standards. The X-ray source, detector and component load tray are enclosed in a durable cabinet designed for quick installation. Once the component has been loaded onto the tray and the image taken, they are then processed by a special version of X-Tek’s image processing software, IMPS III. The images are viewed as a radiograph on a 1600 x 1200 pixel screen and archived onto CD-R or DVD-R discs. The software has been optimised to obtain the maximum performance from the X-ray detector, and automatically compensates for bad pixels and non-uniformity. ‘The way we work is more or less the same, only without the development of the film,’ says Martens. ‘We now have a digital image on a computer screen.’
Summary
With the cumulative benefits offered by digital X-ray, X-Tek Industrial hopes that its demonstration facility and the capabilities of its digital X-ray systems, such as the VENLO will encourage those industries that have relied on the radiographic quality of film and its limitations, to finally make the move from film to digital.
|