Article Updated on 24th February 2021
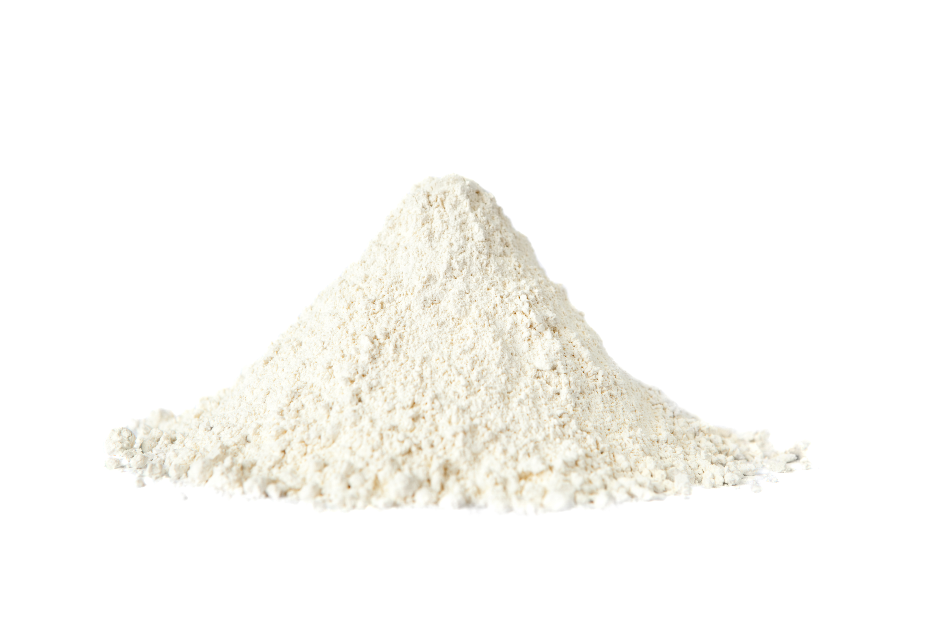
Image Credit: Mona Makela/Shutterstock.com
Both powders and other granular materials can be found in a wide range of industries ranging from material science to pharmaceutical formulations. Despite their widespread use, researchers and manufacturers of such industrial powders often face various challenges during the characterization of their powder samples’ properties. Powder rheology is a useful scientific field aimed at addressing these challenges; however, it is also associated with its inherent limitations.
What is Powder Rheology?
The study of powder rheology is primarily focused on evaluating the various properties of powders when exposed to a range of different stress and/or shear conditions. Powder rheology can be conducted when the sample is stationary, in motion or about to move.
The Restrictions of Characterizing Powders
Industrial powders and bulk materials exhibit a wide range of dynamic properties, many of which are often difficult to characterize and understand. Furthermore, these characteristics can be further complicated by several factors including particle shape, size, and distribution, as well as environmental conditions including humidity, temperature and consolidation history.
The inherent limitations associated with investigating the rheological properties of powders often leads to highly frequent problems during scaling manufacturing processes through their production and storage.
Current Powder Rheology Methods
The appropriate powder rheology method is chosen based on the composition of the sample. The four primary characteristics used to determine a powder sample’s characteristics include high load, low load, aerated and fluidized.
Shear testing, which involves the application of shear or horizontal force onto an upper layer of powder while the lower layer remains stagnant, is a method that is often used to characterize the shear strength of both high and low load powders. Wall friction, caking, flowability, bulk density, and compressibility tests can also be used to assess the rheological characteristics of both high and low load powders.
The rheological assessment of both low load and aerated powders can be achieved by cohesion strength, permeability, and tensile strength tests. Similarly, fluidized bed viscosity and segregation tests can be used to assess both aerated and fluidized powders, whereas pressure drop and air retention tests are strictly used for the evaluation of purely fluidized powders.
In addition to the methods discussed above, several other well documented rheological techniques can be used to assess industrial powders, some of which include Angle of Repose (AOR), flow meters and tapped density tests.
Limitations of Modern Powder Rheology
Despite the availability of several powder rheology techniques, manufacturers are often unable to precisely characterize many of the fundamental properties of industrial powders outside of their particle size and crystal habit. The methods typically used to evaluate the impact that external factors like humidity and temperature have on powders can often be expensive and limited in their ability to characterize the full lifespan of a powder.
In addition to these broad limitations, each powder rheology method is associated with its specific insufficiencies. AOR and flow meter analyses, for example, require the placement of the powder sample through a funnel, which eliminates any cohesive powders from being analyzed by these techniques.
Furthermore, tapped density tests, which involves the persistent tapping of powder over a defined period of time, is also not ideal for studying cohesive powders since the inter-particular bonds of such powders are stronger than the tapping forces typically used in these density tests.
Overcoming the Limitations
The deficiencies associated with most powder rheology techniques demand the manufacturers and researchers of this field to establish a multivariate approach capable of adequately assessing the diverse and complex behavior of powders.
As powders continue to emerge as key players in a greater number of industries, such as additive manufacturing, it will become even more pressing for researchers to develop methods capable of obtaining the rheological measurements of powders to determine their in-process performance and beyond.
Sources and Further Reading
Disclaimer: The views expressed here are those of the author expressed in their private capacity and do not necessarily represent the views of AZoM.com Limited T/A AZoNetwork the owner and operator of this website. This disclaimer forms part of the Terms and conditions of use of this website.