14 million motor vehicles are scrapped in the EU each year, representing an enormous waste problem. Seventy-five percent of a modern car is composed of ferrous and non-ferrous metals, which are readily recycled back into the metals industries. However, the remaining 25% is composed of plastics, rubber and other components, which are currently disposed of in landfill. Compounding this problem is the automotive industry’s desire to use new, lighter materials, particularly plastic composites, to reduce weight and so improve fuel efficiency. Unfortunately composite plastic materials are generally regarded as being unrecyclable owing to the reinforcing fibres.
Recycling of Automotive Composites by Pyrolysis
The expertise of Leeds University in waste pyrolysis is now being applied to the problem of composite plastic waste. A two-year research project between the university and partners from British industry has led to a defined process to recover the glass fibres from composite plastic waste, and to produce an oil/wax product suitable for use as a liquid fuel or as a chemical feedstock to produce new plastics.
How Much of a Modern Car is Consists of Composites
Replacement of traditional metal components by composite plastics in applications such as bumpers, under bonnet components, body panels and exterior trim has significantly reduced the weight of the average car. Typically, 10% of a vehicle’s weight (wt%) is made up of plastics and plastic composites, and for some lightweight vehicles this may be up to 20 wt%. Composites are increasingly used since they have the advantages of strength, durability and corrosion resistance together with low weight.
Materials Used in Automotive Composites
Composites are composed of many different components, including glass fibre reinforcement, filler material and the thermoset or thermoplastic polymer, which is the matrix or continuous phase. The plastic polymer components commonly used include thermoset polyester, phenolic resin, epoxy resin, polypropylene and vinylester resin. It is the mixture of components embedded in the matrix that make composites difficult to recycle and the reason why such a high percentage is sent to landfill. Consequently, there is a need to identify novel process routes to enable the recycling of composite materials, particularly in light of the European Union End of life Vehicle (ELV) Directive (2000), which requires Member States of the EU to reuse and recover 85 wt% of the average vehicle weight by 2006, increasing to 95 wt% by 2015.
What is Pyrolysis and What is Its Advantage?
The research group at Leeds University has researched the application of pyrolysis for waste processing for more than 15 years funded mainly through research grants from the UK Engineering and Physical Sciences Research Council (EPSRC). Pyrolysis is the thermal degradation of the waste polymer component in the absence of oxygen. The polymer breaks down to produce an oil/wax a gas and a char product, leaving a solid friable residue. Pyrolysis has the advantage that potentially all of the products from the process can be used.
What is The Process Designed to Do?
To date the group’s work has involved collaborations with industrial partners investigating the pyrolysis of scrap tyres, plastic wastes and municipal solid wastes. In this latest project, the research concentrated on developing a process to separate and clean the glass fibre in composite components, and to investigate its use in new products.
Product Yields for Pyrolysis of Various Polymer Matrix Composite
The term composites covers a broad range of mixed components, and pyrolysis will consequently produce a range of products. Table 1 shows the product yield for a range of composite materials pyrolysed at 500°C. Pyrolysis depolymerises the polymer chain producing wax, oil and gas (the gas has sufficient energy content to provide the energy requirements of the pyrolysis process plant) derived from the original plastic. The gas composition produced is again dependent on the original plastic used in the composite. For oxygen-containing plastics such as polyester and phenolic resins, the main gases are carbon dioxide and carbon monoxide. For other plastics, higher concentrations of hydrogen and hydrocarbons, such as methane and ethane, are dominant. The wax and oil are given off as gases during pyrolysis but are condensed downstream. The oil and wax have a high calorific value and can be burnt to provide energy. Alternatively, they can be used as a source of valuable chemicals. The solid residue left behind after pyrolysis is a friable solid containing the glass fibre and filler, and a small amount of carbonaceous char derived from the plastic degradation.
Table 1. Product yield from the pyrolysis of various composite wastes in wt%.
|
Polyester resin/CaCO3/glass fibre
|
45.8
|
45.7
|
8.5
|
Phenolic resin/MgO,CaCO3/ glass fibre
|
90.2
|
8.8
|
1.0
|
Epoxy resin/glass, carbon fibre
|
67.4
|
31.3
|
1.2
|
Polyester resin/silane bonder/glass fibre
|
30.0
|
59.4
|
10.6
|
Propylene resin/silane binder/glass fibre
|
44.8
|
46.8
|
8.4
|
Polyethylene terephthalate resin/glass fibre
|
74.4
|
13.0
|
12.6
|
Vinylester resin/glass fibre
|
83.4
|
15.0
|
1.6
|
Led by Pera Technology, the research partnership, which included industrial partners from the British Plastics Federation, Society of Motor Manufacturers and Traders, Filon Products, Cray Valley, OSS Group, Reichold and Shanks Waste Solutions, decided to concentrate on glass fibre reinforced styrene-polyester co-polymer composite as a typical high usage material.
Properties and Uses for the Oil and Wax Produced by the Pyrolysis Reaction
Pyrolysis converted 40% of the composite plastic waste into oil, which had fuel properties similar to those of a petroleum-derived gas oil. In addition, the oil contained 25 wt% of styrene, which was used in the production of the styrene-polyester copolymer. As well as producing the oil, the plastic was thermally degraded into a wax composed of more than 95 wt% of phthalic anhydride, which was used in the production of the composite material. The use of the oil and wax as a chemical feedstock in the production of new plastic materials has much greater value than the their use as substitute
Low Temperature Benefits of the Pyrolysis Process
One of the major and valuable constituents of composite plastic wastes is glass fibre. The problem for glass fibre recovery is to use process conditions that do not degrade the fibre strength, and the key parameter is the temperature. Above 800°C the fibres become very brittle and quickly lose strength. Pyrolysis has the advantage of low process temperatures of less than 500°C which retains the strength and flexibility of the virgin glass fibre.
Separation of the Glass Fibres
Separation of the glass fibre from the filler was achieved using a drum carder machine, which gently separates the fibres from the friable char and filler matrix. The fibres can then be used as char-coated fibres to produce new composite plastic materials. Alternatively, the blackened glass fibre can be cleaned using low-temperature furnace oxidation to burn off the char to produce cleaned fibre.
Re-Using Recycled Glass Fibre
The recovered glass fibre, both cleaned and char-coated, were made up into test samples of a new composite by the industrial partners. Test samples incorporating 25 wt% of the recovered glass fibre and 75 wt% virgin glass fibre were compared to a controlled sample containing 100 wt% virgin glass fibre. The results showed that up to 25 wt% of recycled fibre could successfully be incorporated into a new composite while still meeting manufacturers specifications.
Summary
Overall the application of pyrolysis as a process route for a difficult waste stream in the form of composite plastic waste appears to show potential. The next step will involve scaling up the process to pilot plant scale, and the partnership is investigating further funding opportunities. Figure 1 shows a schematic diagram of the proposed pyrolysis recycling process. A cost-effective recycling process is an essential step towards sustainable manufacturing. It will be particularly important for the automotive industry as it prepares to meet the requirements of the European End of life Vehicle Directive. Additionally, for plastics manufacturers, the process could have a major impact in overcoming resistance to composites for new applications in an increasing range of advanced, lightweight components.
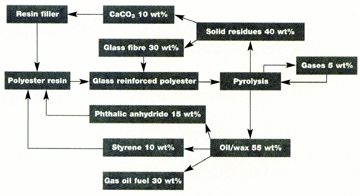
|
Figure 1. Schematic diagram of the proposed pyrolysis recycling process for composites.
|
|