Industrial machinery parts experience wear and tear, significantly decreasing their operational lifetime. Lubricants help by allowing machinery components to move freely, reducing friction between them. This enables improved equipment performance, increased efficiency, and extended system life cycles.1
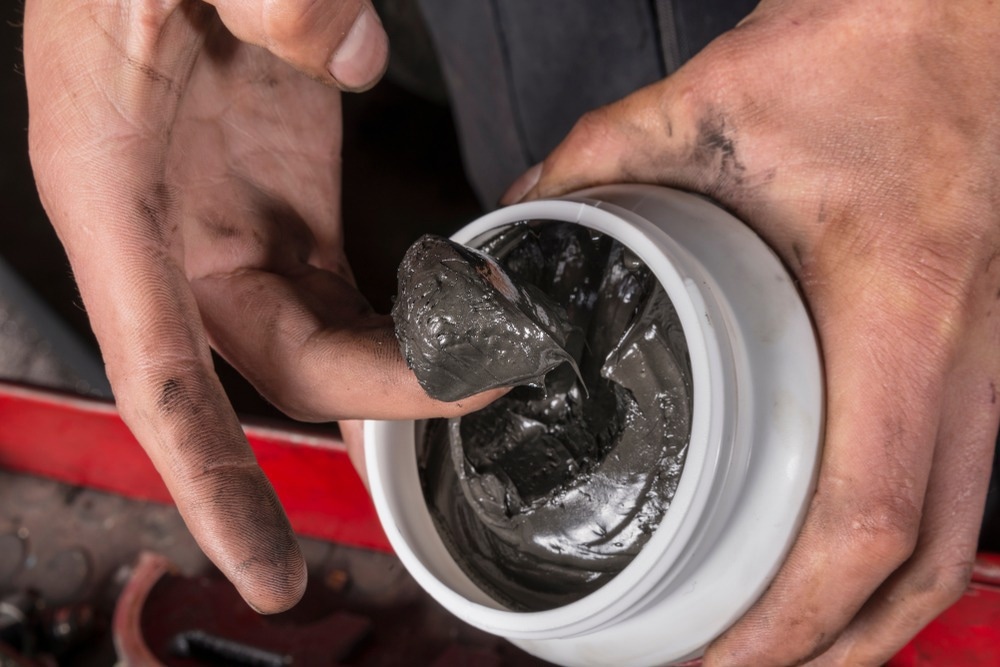
Image Credit: Leon Rafael/Shutterstock.com
Solid lubrication has become essential in materials science. The first United States patent for these materials was issued in the mid-1940s.2 Since then, significant progress has been made in the industrial applications of solid lubricants, along with rapid improvements in their properties.
The Basics of Lubrication
Industrial lubricants vary widely in their chemical and physical properties based on their application, encompassing gases, liquids, greases, and solids.3
The most commonly used liquid lubricants are hydrocarbon oils derived from refining crude petroleum. These oils come in various viscosities, providing options for different load, speed, and temperature conditions.
Naphthenic oils, used for industrial purposes, have low viscosities, high oxidation resistance, and low pour points, differing significantly from paraffinic oils. Synthetic lubricants, though more expensive, are essential for specialized applications and complex machinery.4
Traditional liquid lubricants are ineffective at high temperatures due to volatility, flammability, and susceptibility to oxidation. While easy to handle, oil-based lubricants offer moderate performance and can be contaminated by dust. They can also combust at high operating temperatures, necessitating the use of alternative lubricants, particularly solid lubricants.5
What are Solid Lubricants?
Solid lubricants significantly reduce friction and wear between moving components, protecting surfaces at the atomic level. These lubricants are used where liquid-based lubricants are unsuitable and are applied in various forms, such as thin films, surfaces, and self-lubricating composite materials.6
Solid lubricants are categorized into organic and inorganic types. Inorganic examples include molybdenum disulfide (MoS₂), hexagonal boron nitride (hBN), molybdenite, and graphite. Organic lubricants include polymers like polytetrafluoroethylene (PTFE), polyimide, fullerenes, and diamond-like carbon.
Inorganic lubricants, also known as lamellar lubricants, have weak van der Waals forces between layers, resulting in low friction and minimal wear. These layers align parallel to the motion, facilitating easier sliding.7
Advancements in Solid Lubricant Technology
Graphite, MoS₂, and PTFE are predominant solid lubricants with high cost-efficiency. Graphite is most widely used due to its excellent lubrication properties, stable structure, self-lubricating nature, and high thermal conductivity, making it suitable for high-temperature applications.8
MoS₂ is significant for modern solid lubricants, used as a dry film, additive in oils or greases, or as a lubricant coating. It provides excellent lubrication even without humidity and improves in humid, oxygen-deficient environments. MoS₂ is preferred for space systems due to its effectiveness across various temperatures and pressures.9
PTFE, known as Teflon, is a polymeric solid lubricant with superior antifriction characteristics. It is water-repellent, heat-resistant, and exhibits a low coefficient of friction, making it useful in engineering applications such as non-stick cookware, corrosive substance pipes, and surgical grafts.10,11
Graphene, an allotrope of carbon with a honeycomb structure, provides effective lubrication in dry conditions. A significant difference between graphite and graphene is its ability to provide effective lubrication even in very dry conditions.
hBN, another industrial solid lubricant, has a laminar structure similar to graphite, excellent thermal conductivity, and superior chemical and oxidation resistance, making it suitable for high-temperature applications.12
MXenes: An Advanced Class of Solid Lubricants
MXenes, an emerging class of 2D nanomaterials, are attracting attention for their tribological and mechanical applications due to their compositional variety, chemical and structural properties, strong intralayer bonding, and weak interlayer bonding.13
Researchers have discovered that MXene nanosheets exhibit self-lubricating properties, making them ideal for self-lubricating surface coatings. Incorporating MXenes as lubricant reinforcement in polymeric composites effectively improves their anti-friction attributes. When used as a lubricant, MXenes form a durable tribofilm between contacting surfaces, preventing microfractures and extending machinery life.
Studies have shown that the amount of MXenes added greatly influences lubrication, with an optimal concentration of around 1 % leading to significant reductions in wear volume/rate. However, the hydrophilicity of MXenes’ surface terminations can reduce their effectiveness as oil-based lubricant additives.
To address this issue, chemical modifications are commonly employed to adjust MXenes’ hydrophobicity. As water- and oil-based lubricant additives, MXenes’ excellent lubrication performance primarily stems from the formation of tribofilm on the friction surface.14
Solid Lubricants: Major Challenges and Future Perspectives
No single material can meet the full lubrication requirements from room temperature to extremely high temperatures (approximately 1200 °C). Additionally, there is a significant lack of atomistic- and nano-level analysis of the evolving physical and chemical properties of solid lubricating surfaces and sub-surfaces.
The specifics of feedstock/precursor compositions and their systematic study are also unclear, raising concerns about the accuracy of experimental inputs.
Efforts have been made to address these challenges, but significant work remains to improve solid lubricants. Experts have extended the operational temperature range by blending various solid lubricants, increasing efficiency for temperatures up to 700-800 °C.
To meet extreme temperature lubrication needs, high-temperature solid-lubricating materials must be designed with a wear rate below 10⁻⁶ mm³/Nm and capable of functioning across a broad temperature range, from cryogenics to high temperatures.
The emergence of materials like MXenes, which show great potential as solid lubricants, presents opportunities to explore a wider range of synergies with textures. Studies could systematically vary both the solid lubricant and texture design.
Hybrid/composite solid lubricants, combining two or more materials to blend their advantages, offer a promising avenue for further research. However, results will likely be condition-dependent, so multiple operating conditions relevant to the target application should be considered.15
Green lubrication has become an interesting field of study, with a focus on sustainability and reducing harmful emissions. Researchers are developing novel solid lubricants and coatings, and significant improvements in their lubrication properties are expected over time. An extensive study of additive manufacturing for solid lubricant coatings is needed, and it is expected to revolutionize this essential technology.
More from AZoM: Alloy vs. Steel Wheels: Comparing Performance, Durability, and Design
References and Further Reading
[1] Lisa (2022). The importance of lubrication for machine reliability. [Online] Oil-Store. Available at: https://www.oil-store.co.uk/blog/the-importance-of-lubrication-for-machine-reliability/ [Accessed at: June 11, 2024].
[2] Sunil, T., et al. (2016). A critical review on solid lubricants. Journal of Mechanical Engineering and Technology. https://www.researchgate.net/publication/313470850_A_critical_review_on_solid_lubricants
[3] Roy, MM., Fox, M. (2010). Chemistry and technology of lubricants. Dordrecht: Springer (Vol. 107115, pp. 56-75). Available at: https://download.e-bookshelf.de/download/0000/0048/40/L-G-0000004840-0002333661.pdf
[4] Robertson, WS. (1983). Types and Properties of Lubricants. Lubrication in Practice. doi.org/10.1007/978-1-349-06731-2_2
[5] Afonso, I., et al. (2023). Conventional and Recent Advances of Vegetable Oils as Metalworking Fluids (MWFs): A Review. Lubricants. doi.org/10.3390/lubricants11040160
[6] Sutor, P. (1991). Solid Lubricants: Overview and Recent Developments. MRS Bulletin. doi.org/10.1557/S0883769400056864
[7] Kumar, R., et al. (2020). An outline on modern day applications of solid lubricants. Materials Today: Proceedings. doi.org/10.1016/j.matpr.2020.05.558
[8] Huai, W., et al. (2021). Graphite-based solid lubricant for high-temperature lubrication. Friction 9. doi.org/10.1007/s40544-020-0456-2
[9] Vazirisereshk, M., et al. (2019). Solid Lubrication with MoS2: A Review. Lubricants. doi.org/10.3390/lubricants7070057
[10] Xenum. (2023). Solid lubricants: PTFE and Cerflon [Online] Xenum. Available at: https://xenum.com/solid-lubricants-ptfe-cerflon/ [Accessed on: June 14, 2024].
[11] Shamsuddin, M., et al. (2020). Influence of PTFE as a solid lubricant on the mechanical, electrical, and tribological properties of CF reinforced PC composites. Journal of Applied Polymer Science. doi.org/10.1002/app.50346
[12] Kumar, R. et al. (2022). Solid Lubrication at High-Temperatures-A Review. Materials. doi.org/10.3390/ma15051695
[13] Rasheed, T., et al. (2024). Unveiling the power of MXenes: Solid lubrication perspectives and future directions. Advances in Colloid and Interface Science. doi.org/10.1016/j.cis.2024.103186
[14] Lu, X., et al. (2023). A review on the synthesis of MXenes and their lubrication performance and mechanisms. Tribology International. doi.org/10.1016/j.triboint.2022.108170
[15] Rosenkranz, A., et al. (2021). Synergetic effects of surface texturing and solid lubricants to tailor friction and wear–a review. Tribology International. doi.org/10.1016/j.triboint.2020.106792
Disclaimer: The views expressed here are those of the author expressed in their private capacity and do not necessarily represent the views of AZoM.com Limited T/A AZoNetwork the owner and operator of this website. This disclaimer forms part of the Terms and conditions of use of this website.