Superconducting energy storage systems store energy using the principles of superconductivity. This is where electrical current can flow without resistance at very low temperatures.
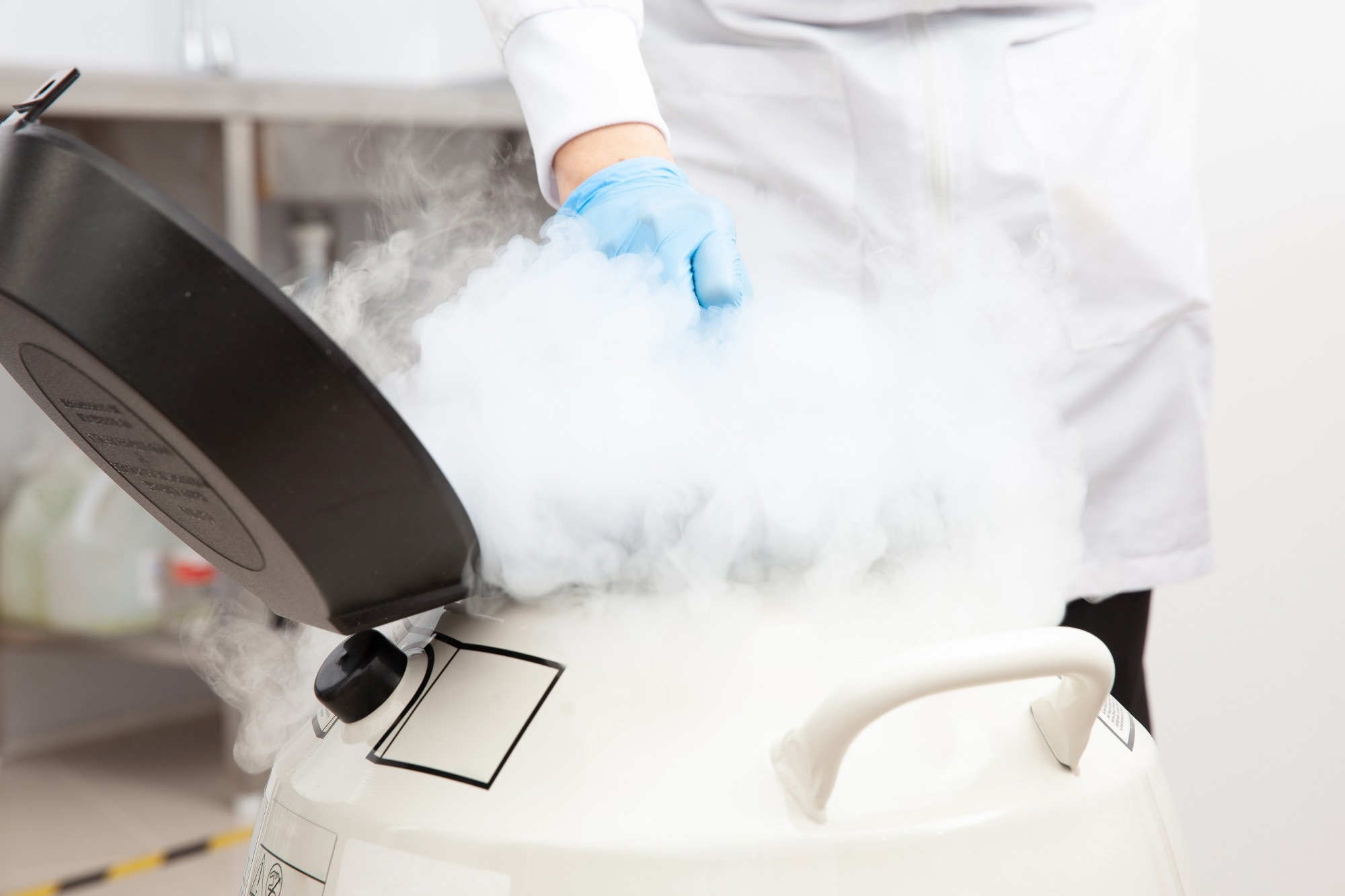
Image Credit: Anamaria Mejia/Shutterstock.com
These systems offer high-efficiency, fast-response energy storage, and are gaining attention for grid stabilization, high-power applications, and renewable energy integration.
The concept is not new. As early as the 1960s and 70s, researchers like Boom and Peterson outlined superconducting energy systems as the future of energy due to their extremely low power losses.
Over time, this vision has evolved into two main technological pathways: Superconducting Magnetic Energy Storage (SMES) and superconducting flywheel energy storage systems. Both use superconducting materials but store energy in different physical forms (magnetic fields versus rotational motion).
How Superconducting Energy Storage Works
Superconducting Magnetic Energy Storage
SMES stores energy in a persistent direct current flowing through a superconducting coil, producing a magnetic field.
The concept was first proposed by Ferrier in 1969 and realized shortly thereafter by researchers at the University of Wisconsin. The technology advanced further in the 1990s with the introduction of high-temperature superconductors, and by 1997, a grid-connected SMES unit was demonstrated in Germany.
A standard SMES system comprises a vacuum-insulated cryogenic chamber that houses the superconducting coil, a cooling system (using liquid helium or nitrogen), a power conditioning system (PCS), and a control and protection system.
The PCS manages the conversion between AC and DC power, enabling fast charge and discharge cycles. Once current is induced in the superconducting coil, it continues to flow indefinitely without loss, thanks to the zero electrical resistance at cryogenic temperatures.
SMES coils can maintain this current even when the voltage source is removed. Variations in the current create changes in the surrounding magnetic field, and this energy can be efficiently recovered.
Discharge efficiencies of up to 95 % are possible, with system lifetimes exceeding 30 years. SMES systems are also known for their rapid response times, making them suitable for stabilizing power grids and handling high-frequency power fluctuations.
Recent developments in SMES include efforts to improve power system stability using artificial intelligence. Techniques such as fuzzy logic controllers (FLCs) and artificial neural networks (ANNs) are being tested to optimize real-time decision-making and fault tolerance.
However, despite the technological maturity (SMES are considered to have reached Technology Readiness Level 7), widespread industrial deployment remains limited. Future research is expected to focus on integrating SMES into live grid environments, where long-term performance and cost-effectiveness can be validated under real-world conditions.
Download your PDF copy now!
Superconducting Flywheel Energy Storage
In contrast to SMES, superconducting flywheel energy storage systems store energy in the form of kinetic energy. The system uses a motor to spin a rotor at high speed, converting electrical energy into rotational energy. When energy is needed, the motor acts as a generator, converting the rotor’s kinetic energy back into electricity.
These systems first gained attention in the 1960s and 70s, particularly in aerospace applications. NASA, in collaboration with the United States Flywheel Systems (USFS), explored flywheel batteries as a power backup solution for deep space missions and electric vehicles. Early designs used fiber-composite rotors, and while initial systems lacked long-term durability, they laid the foundation for current high-efficiency flywheel storage technologies.
A modern flywheel system typically includes power electronics, a tachometer for rotational monitoring, analog-to-digital converters, and a real-time control computer. These components regulate motor speed and conversion efficiency, ensuring the flywheel operates safely and reliably across load cycles. The amount of energy stored is proportional to the flywheel’s moment of inertia and the square of its angular velocity.
There are two main configurations in high-temperature superconducting flywheel systems. One design uses axial superconducting magnetic bearings (SMBs) to support the rotor’s thrust, with passive magnetic bearings (PMBs) and active magnetic bearings (AMBs) providing radial stabilization and vibration control. These components operate in a vacuum chamber to minimize friction and energy loss.
The second design adopts a radial configuration, where radial SMBs carry the weight of the rotor and both radial and thrust AMBs ensure stability. These systems allow for high rotational speeds and can deliver quick bursts of energy.
While early flywheel batteries suffered from material fatigue and limited energy density, advances in magnetic bearing technology and control systems have renewed interest in flywheels, particularly for applications requiring rapid discharge and high cyclability.
The Future of Superconducting Energy Storage Tech
Superconducting energy storage technologies have demonstrated strong potential for high-efficiency, low-loss energy management. Among these, SMES stands out for its rapid charge–discharge response, high cycle life, and minimal environmental impact.
However, deployment at an industrial scale remains limited. Bridging the gap between laboratory success and real-world application is a key priority. Ongoing research is expected to focus on optimizing cost, expanding thermal management strategies, and validating system performance under live grid conditions.
As clean energy targets drive demand for more sustainable storage solutions, superconducting technologies are well-positioned to support future high-performance power systems.
References and Further Reading
- Boom, R. et. al. (2003). Superconductive energy storage for power systems. IEEE Transactions on Magnetics. 8(3). 701-703. Available at: https://doi.org/10.1109/TMAG.1972.1067425
- Bitterly, J. et. al. (1998). Flywheel technology: past, present, and 21st century projections. IEEE Aerospace and Electronic Systems Magazine, 13(8), 13-16. Available at: https://doi.org/10.1109/62.707557
- Kwon, K. (2021). Flywheels Turn Superconducting to Reinvigorate Grid Storage Potential: Energy losses defeated previous-gen flywheels as viable big batteries; so new ones levitate more efficiently. IEEE Spectrum. [Online]. Available at: https://spectrum.ieee.org/superconducting-flywheel-grid-energy-storage [Accessed on: March 04, 2025].
- Tang, J. et. al. (2010). Superconducting energy storage flywheel—An attractive technology for energy storage. Journal of Shanghai Jiaotong University (Science). 15. 76-83. Available at: https://doi.org/10.1007/s12204-010-7151-9
- Gandolfi, C. et. al. (2018). Study of a universal power SMES compensator for LV distribution grid. In 2018 AEIT International Annual Conference (pp. 1-6). IEEE. Available at: https://doi.org/10.23919/AEIT.2018.8577335
- Buckles, W. et. al. (2000). Superconducting magnetic energy storage. IEEE Power Engineering Review, 20(5), 16-20. Available at: https://doi.org/10.1109/39.841345
- European Energy Research Alliance (EERA) Joint Program SP5-Superconducting Magnetic Energy Storage. (2019). Fact Sheet 1. [Online]. Available at: https://www.eera-energystorage.eu/component/attachments/?task=download&id=566:EERA_JPES_SP5_Factsheet_final [Accessed on: March 05, 2025].
- Adetokun, B. et. al. (2022). Superconducting magnetic energy storage systems: Prospects and challenges for renewable energy applications. Journal of Energy Storage, 55, 105663. Available at: https://doi.org/10.1016/j.est.2022.105663
- Khaleel, M. et. al. (2023). Technical challenges and optimization of superconducting magnetic energy storage in electrical power systems. e-Prime-Advances in Electrical Engineering, Electronics and Energy, 5, 100223. Available at: https://doi.org/10.1016/j.prime.2023.100223
Disclaimer: The views expressed here are those of the author expressed in their private capacity and do not necessarily represent the views of AZoM.com Limited T/A AZoNetwork the owner and operator of this website. This disclaimer forms part of the Terms and conditions of use of this website.