A wide variety of processes are commercially available for achieving a hard (1100 - 2500Hv) but usually very thin (typically no more than 4 microns thick) gold coloured titanium nitride layer on titanium. Titanium nitride TiN is inert, biocompatible and will tolerate temperatures up to 480°C in air. Against other nitrided surfaces the coefficient of friction is .05 - 0.15. Titanium Produced by Plasma Nitriding Plasma nitriding is the simplest and most widely available process, able to generate coatings uniformly on the exposed surfaces of components of any configuration. Plasma nitriding poses two problems for titanium, the process temperature, 700°C or above delivers most alloys in the fully annealed or overaged condition, secondary problems are surface roughening and a reduction of fatigue limit, particularly with thicker layers of nitride. At this temperature the titanium oxide film is removed, and nitrogen is used to produce a harder substrate by diffusion before deposition of the titanium nitride is initiated. Lower temperature processes (450°C) are available which deposit very thin films (3 microns), and cause no surface roughening. A problem encountered with these thin layers is the deformation of the underlying titanium and consequent failure of the coating as surface loadings increase. Stiffening and strengthening of the substrate can be achieved by laser surface melting with nitrogen, (sometimes referred to as ‘laser nitriding’), or electron beam melting of preplaced alloying additions. A tenfold increase in the depth of the hardened layer can reduce overall wear rates by two orders of magnitude, placing titanium performance close to that of hardened and tempered steel (En19). Techniques and equipment exist to nitride both relatively small and larger components. Nitrided titanium alloy hydraulic shafts up to 4 metres long (manufactured and coated by Permascand AB) were used for the Snorre Tension Leg Platform subsea tensioning system. The layer thickness was 5 -12 microns with an average hardness of 900HV. Fluidised bed nitriding (Nobleizing) equipment, currently able to handle larger parts up to 750mm diameter produces thicker films without risk of spalling or cracking. Hardness levels above 650HV are reported for titanium. Problems Associated with Nitride Coatings One of the problems associated with nitride coatings is reduction of component fatigue life due to surface layer cracks developing and propagating through the parent metal. This effect increases with increasing film thickness as second and associated problem is chipping of heavier films (6 microns plus). Applications of Titanium Nitride Coated Parts Motorsports The motor racing industry has been a major user of nitrided titanium components, with successful applications on valves, and valve gear, connecting rods, bearings, hubs and other sliding and wearing surfaces. Nitride and nitrocarburised coatings are an effective treatment against scuffing. In one case, the life of Grand Prix car front and rear hubs was extended from a single race to a full season. Ball Valves Ball valve bodies represent another successful application for sea water and chemical plant duties. 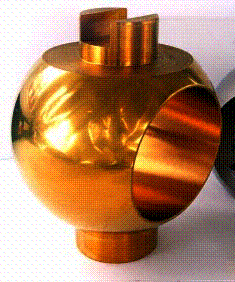 | Figure 1. Titanium nitride coated ball valve. | Implants Parts for implantation may require polishing after nitriding to reduce surface roughness. |