Feb 20 2006
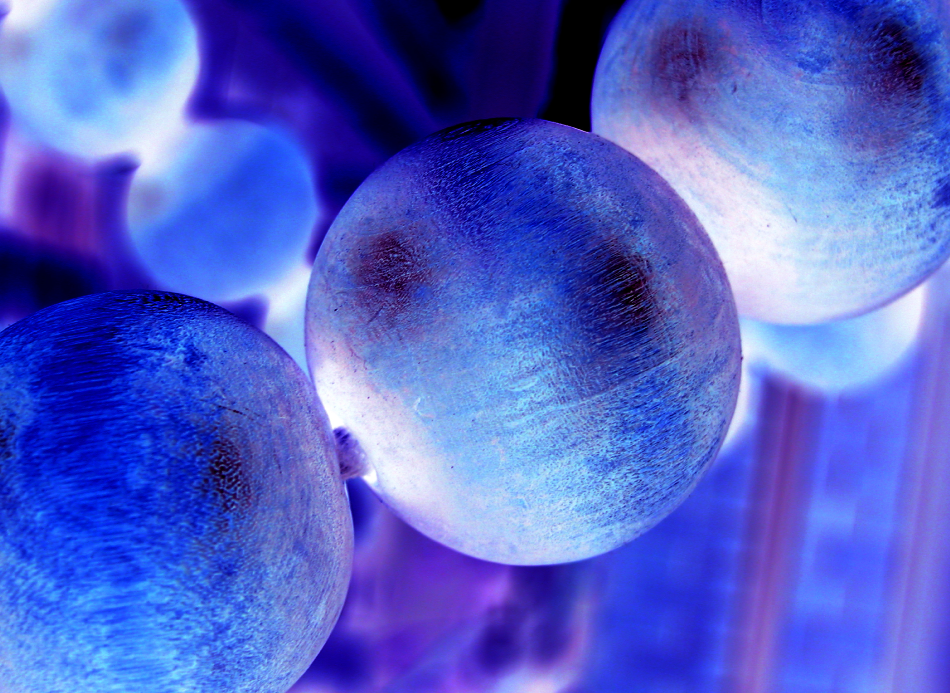
Radu Razvan / Shutterstock
Metallurgy is vital to the industry for developing and making products from metals, composites, alloys, and other metal-related materials. Usually, product development and quality control processes employ microstructure analysis for the characterization of metals.
The microstructure of metals can differ based on composition, heat treatment, fatigue, or stress distribution. For failure analysis, it is important to inspect fracture surfaces.
Physical metallurgy research pays attention to the variations in the microstructure of metals under different conditions. For instance, the thermodynamics of defect formation, grain boundaries migration, and precipitation are known by examining morphology evolution. Furthermore, morphological studies are beneficial in understanding dislocation flow, stress-strain distribution, and crack propagation.
The most universally used tools for examining metals in both industry and research are the scanning electron microscope, the optical microscope, and the transmission electron microscope. The Atomic Force Microscope (AFM) is emerging as a crucial tool for metallurgy.
The AFM offers the following benefits for metallurgical studies:
- Three-dimensional surface topograms: The AFM provides magnification in the X-Y and Z axes, unlike the other types of microscopes. This is very useful in comprehending the depth of surface features.
- Very high magnification: Magnifications of up to 1,000,000x can be easily acquired with an AFM.
- Optical microscope: AFM instruments include a video optical microscope for quickly visualizing the metals’ surface.
- Simplified sample preparation: Requires little or no sample preparation before metal samples are analyzed with an AFM.
- Easy to use: Compared to other microscopes with extreme magnification, the AFM is quite user-friendly. With the cutting-edge technology used in AFM systems, users can efficiently measure images within a day.
AFM is used in many metallurgical studies. Two of these applications are given below.
Dendrite Structure
Dendrite (from Greek “dendron” meaning a tree) is a crystal with a tree-like branching pattern that is most apparent in cast metals that are gradually cooled through the solidification range. Generally, the dendrite structure can be observed using an optical microscope; however, the resolution of the video optical microscope is restricted to 1 µm.
Other microscopy techniques such as the SEM do not enable the dendrite structure to be observed. With the AFM, it is quite easy to see the dendrites’ structure with a resolution far greater than 1 µm. Such studies can offer beneficial information to gain a deeper understanding of interface instability during the solidification process.
Precipitation Study
Precipitate hardening (aging) is hardening induced by the precipitation of a constituent from a supersaturated solid solution. Aging is a microstructure alteration caused typically by precipitation. This precipitation takes place in certain alloys after initial heat treatment or cold working operation. Precipitate hardening alloys (superalloys) have superior mechanical properties at higher temperatures and are generally used for industrial applications.
Observation of the precipitate’s size of <1 µm is not possible using an optical microscope because of limitation in resolution. SEM visualization is sufficient, but it offers neither a 3D image nor accurate line profile measurements for the features of interest.
TEM is the most generally used method for precipitation research, but it needs complicated sample preparation as well as a highly skilled operator. Sample preparation and AFM usage are very easy. AFM images have considerable lateral and vertical resolutions.
The AFM can perform accurate line profile measurements along X, Y, Z, as well as any random direction in the XY plane. Studies and measurements can help in comprehending the underlying problems such as the kinetics of coarsening and the impact of internal and external stresses on the equilibrium shape of inclusions.