Jun 19 2001
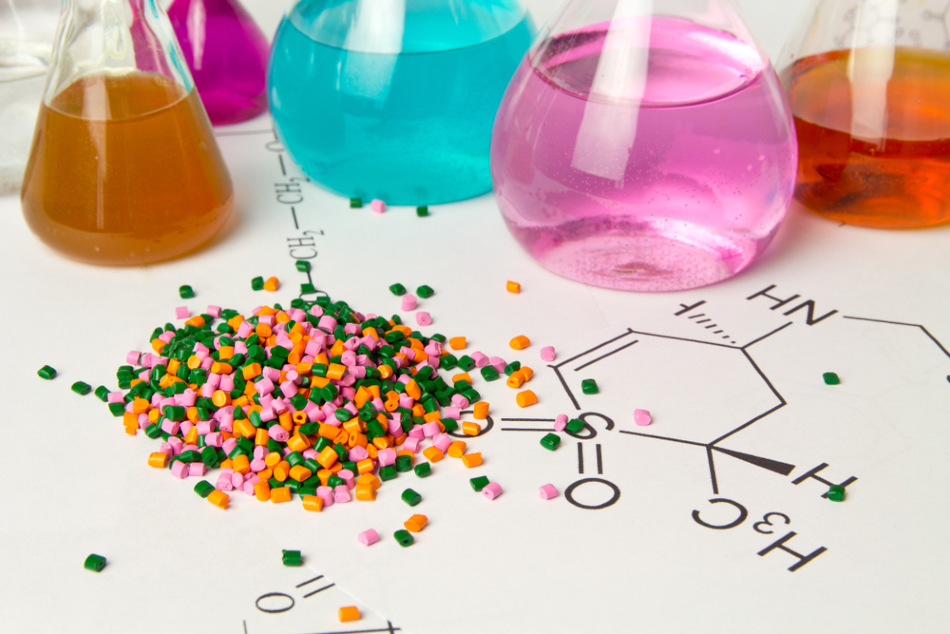
Image Credit: SMAK_Photo/Shutterstock.com
Article updated on 12/02/2020 by Ben Pilkington
A designer often needs to combine soft and hard materials in a single item. For example, an engine mount usually has a rubber cushion attached to a metal base. This example also illustrates another common engineering problem - joining together soft and hard items. This issue is further complicated by mechanical stresses that can concentrate at the boundary between hard and soft parts of a composite structure, which can increase the risk of failure occurring along the boundary.
Several attempts have been made to avoid this type of boundary issue from occurring between soft and hard materials, some of which include mixing rubbers and plastics or gradually changing their proportions so that it becomes soft at one end and hard at the other. However, such an item tends to creep under stress somewhere between the hard and the soft parts, which renders the whole component useless. Moreover, the position of this creeping transition zone is very sensitive to temperature, as even a slight temperature change could cause the whole item to become either plastic or rubbery.
Physical States of Polymers
Polymers can exist in three main physical states that include glassy, rubbery and viscous flow states. The elasticity modulus (EM) of each state varies greatly with the glassy state having an EM anywhere between 2000 and 3000 MPa, whereas the rubbery will have an EM value between 0.1 and 10 MPa. Comparatively, the EM of the viscous flow rate will typically depend upon the speed of deformation. Between the glassy and rubbery states, there is a glass-to-rubber transition zone, which every known polymer, including the rubber-plastic mixes mentioned above, inevitably passes through.
Glass Transition Zone
This glass-to-rubber transition zone is characterized by intermediate EM values between the range of 3 MPa and 3000 MPa. Furthermore, this transition zone is also associated with viscoelastic behavior that causes pronounced creep to occur, which ultimately renders nearly all rubber-plastic mixes to be unusable for practical purposes. The glass-to-rubber zone is sensitive to temperature; in fact, this zone within rubber-plastic mixes will ‘float’ along the material if the temperature changes. Polymers with a variable degree of crosslinking also suffer from the same defect.
A New Physical State
Due to recent intense R&D, a novel method of modifying conventional materials, such as polybutadienes and other rubbers, as well as silicones, has been developed to control mechanical properties like the EM, coefficient of thermal expansion and refractive index (RI). As a result of this method, it is now possible to have a modified rubber with EM between 1 MPa and 3000 MPa, thereby eliminating the glass-to-rubber transition zone and its viscoelastic behavior. In other words, a new physical state for polymers has been created.
This new state offers a wide working temperature range from -70 °C to 120 °C. At higher temperatures, the material goes into the rubbery state and behaves like conventional rubber at temperatures as high as 300 °C. In fact, it is estimated that this figure might be even higher for silicones and fluoro silicone. The material is also associated with a low mechanical loss factor within the range of 0.01 to 0.05, as well as a low rate of stress relaxation and creep.
Methods have been developed for performing this modification on a number of commercially available polymers, using commercially available reagents. This allows the EM of a polymer to be varied gradually, from that of hard plastic material to that of rubber, within one piece of material without any joints (Figure 1).
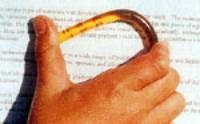
Figure 1. Gradient rigidity in a polymer sample.
Applications
Although the technology itself seems simple, it requires lengthy experience of the operator and sophisticated calculations. An item with a predetermined EM gradient can be molded, or components like gaskets can be carved out of prefabricated sheets. Samples of rods, disks and flat sheets have been manufactured with EM gradients along each axis.
The technology has a huge number of potential applications. Complicated items having parts with different EMs can be developed without using conventional methods of joining such as gluing, riveting, screwing and welding. Apart from reducing production costs, jointless gradient materials are much more robust because, instead of being concentrated on a joint, the stress is distributed throughout the volume of the material.
The range of applications for this new material includes one-piece shoe soles, noiseless cogwheels and rollers, artificial limbs and various other applications where rubber parts need to be joined to metals or ceramics.
Gaskets
Gaskets are another application for the new modified polymer. Rubber materials have a relatively low density of crosslinks, and they perform best when compressed hydrostatically. In the case of a gasket, the material is compressed in one direction only, which may contribute to its failure. Such compression could be brought closer to triaxial compression by reducing the thickness of the gasket. The minimum thickness is limited by the roughness of the surfaces. To this end, gaskets having a thin compliant outer layer on both sides which gradually becomes hard towards the middle have been manufactured and tested.
Lenses
The same technology could also be used to produce transparent polymers with a variable RI. For example, a material with a RI value between 1.38 and 1.90 could allow for the production of lenses with uniform thickness.