The OmniScan® SX is a flaw detector that shares the OmniScan DNA and benefits from more than 20 years of phased array knowledge. The OmniScan SX has a new, more user-friendly software interface that is presented on an 8.4 in. (21.3 cm) touch screen for increased usability.
The OmniScan SX is a single-group, non-modular instrument that is practical and affordable for less demanding applications.
The SX PA and SX UT are the two variants of the OmniScan SX. The SX PA, a 16:64PR phased array device, contains a traditional UT channel for pulse-echo, pitch-catch, or TOFD inspection, just like the SX UT. The OmniScan SX offers an unprecedented degree of mobility for an OmniScan since it is 33% lighter and 50% smaller than the OmniScan MX2.
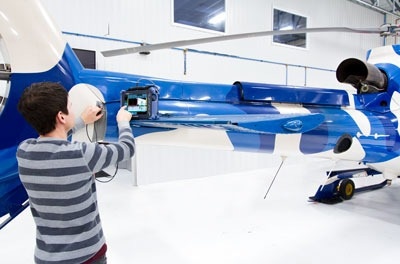
Image Credit: Evident Corporation
Full-screen mode, which enhances visibility and effectively turns numerous menu tasks into simple touch-screen actions, is an option on the OmniScan SX touch screen. The user-friendly interface offers fluid cursor motions, menu selection, zooming, gate changes, and text and value input.
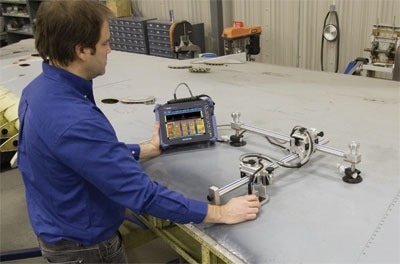
Image Credit: Evident Corporation
These, along with other premium integrated features, including easy-to-follow setup and calibration Wizards, a rapid refresh rate for both the S-scan and A-scan displays, and a fast pulse repetition frequency (PRF), make the OmniScan SX a highly efficient inspection tool.
Our comprehensive line-up of scanners, probes, and accessories, as well as its specialized software partners, NDT SetupBuilder and OmniPC, are all fully compatible with the OmniScan SX.
From design and setup through to acquisition and analysis, the whole range of software and hardware works together to provide a simplified and effective inspection workflow.
Software Features
More functional improvements in the weld and corrosion sectors are included in the new OmniScan software.
The software interface was made simpler and the response time was reduced as part of a continual improvement effort to give clients the greatest experience possible.
Some of the new features include:
- Interleave
- Improved accessibility with more interactive menus
- Curved geometry ray-tracing for longitudinal welds
- Export C-Scan
- Onboard compound scan
- Analysis attenuation gain
- New End-View with group merge
- Optimized main menus and wizards
- Scrolling layouts for easy interpretation
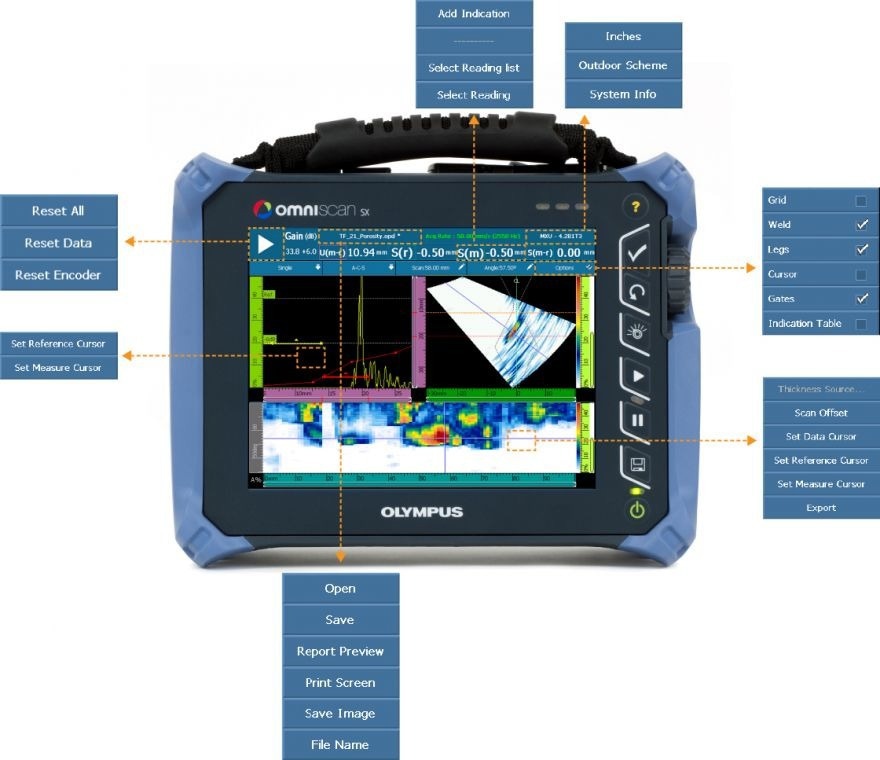
Image Credit: Evident Corporation
The multi-group layouts were enhanced such that the software interface reflects the scanner setup for applications needing a multi-probe configuration. The arrangement is clear and appealing since the placement of the several scans is based on how far they are from the center of the weld.
Applications
Olympus now has a fresh, adaptable tool to add to its collection of original, creative, comprehensive market solutions designed to streamline the workflow and boost productivity.
Phased Array Weld Inspection
The manual and semi-automated phased array weld inspection solutions created by Evident/Olympus for the oil and gas sector are built around the OmniScan PA. These systems provide high-speed detection capabilities, make it easier to read indications, and can be utilized for inspection under the ASME, API, and other code standards.
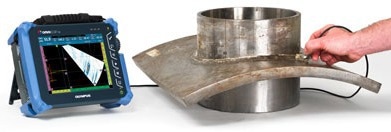
Image Credit: Evident Corporation
Corrosion Mapping and Composite Inspection
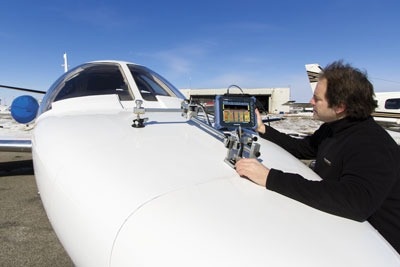
Image Credit: Evident Corporation
The OmniScan SX has now made zero-degree examination even more accessible. Evident/Olympus provides solutions that have been successfully used in the field for corrosion or composite inspection to find abnormalities or wall loss.
TOFD Weld Inspection
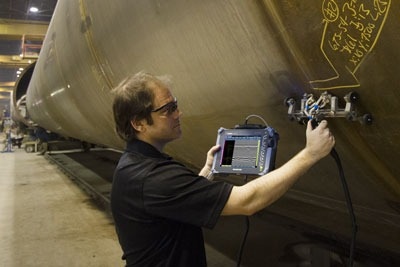
Image Credit: Evident Corporation
A quick and effective method for finding weld faults is TOFD. It is rapid, economical, and capable of sizing manufacturing flaws in the volume of the weld, which is a difficult area to weld.
Component Inspection
Cracks, wall loss, and other damage can be found in components during inspections using ultrasonic methods. The OmniScan SX is a particularly cost-effective option for this kind of single-group inspection since it can accommodate both angle and linear zero-degree beams.
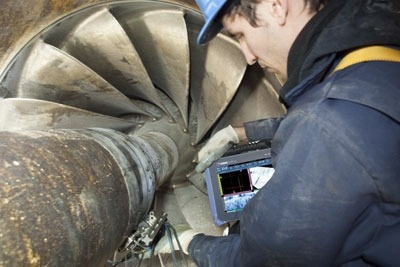
Image Credit: Evident Corporation
Specifications
The basic instrumentation and software criteria outlined in ASME, AWS, API, and EN regulations are met or exceeded by the OmniScan SX.
Source: Evident Corporation
. |
Housing |
Overall dimensions (W x H x D) |
267 mm × 208 mm × 94 mm (10.5 in. × 8.2 in. × 3.7 in.) |
Weight |
3.4 kg (7.5 lb) with battery |
Data Storage |
Storage devices |
SDHC card* or most standard USB storage devices.
*Lexar® brand memory cards are recommended for optimized results. |
Data file size |
300 MB |
I/O Ports |
USB ports |
2 USB ports, compliant with USB 2.0 specifications |
Audio alarm |
Yes |
Video output |
Video out (SVGA) |
I/O Lines |
Encoder |
2-axis encoder line (quadrature, up, down, or clock/direction) |
Digital input |
4 digital TTL inputs, 5 V |
Digital output |
3 digital outputs TTL, 5 V, 15 mA maximum per output |
Acquisition on/off switch |
Yes, through configuration of a digital input |
Power output line |
5 V, 500 mA power output line (short-circuit protected) |
Pace input |
5 V TTL pace input |
Display |
Display size |
21.3 cm (8.4 in.) (diagonal) |
Resolution |
800 pixels x 600 pixels |
Brightness |
600 cd/m2 |
Viewing angles |
Horizontal: –80° to 80° Vertical: –60° to 80° |
Number of colors |
16 million |
Type |
TFT LCD |
Power Supply |
Battery type |
Smart Li-ion battery |
Number of batteries |
1 |
Battery life |
Minimum 6 hours under normal operating conditions |
Environmental Specifications |
Operating temperature range |
-10 °C to 45 °C
(14 ºF to 113 ºF) |
Storage temperature range |
–20 °C to 60 °C (–4 ºF to 140 ºF) with battery
–20 °C to 70 °C (–4 ºF to 158 ºF) without battery |
Relative humidity |
Max. 70% RH at 45°C noncondensing |
Ingress protection rating |
Designed to meet requirements of IP66 |
Shockproof rating |
Drop-tested according to MIL-STD-810G 516.6 |
Ultrasound Specifications (applies to OMNISX-1664PR) |
Connectors |
1 Phased Array connector: Olympus PA connector
2 UT connectors: LEMO 00 |
Number of focal laws |
256 |
Probe recognition |
Automatic probe recognition |
Pulser/Receiver |
Aperture |
16 elements |
Number of elements |
64 elements |
Pulser |
PA Channels |
UT Channel |
Voltage |
40 V, 80 V, and 115 V |
95 V, 175 V, and 340 V |
Pulse width |
Adjustable from 30 ns to 500 ns; resolution of 2.5 ns |
Adjustable from 30 ns to 1,000 ns; resolution of 2.5 ns |
Pulse shape |
Negative square wave |
Negative square wave |
Output impedance |
35 Ω (pulse-echo mode);
30 Ω (pitch- catch mode) |
<30 Ω |
Receiver |
PA Channels |
UT Channel |
Gain |
0 dB to 80 dB, maximum input signal 550 mVp-p (full-screen height) |
0 dB to 120 dB maximum input signal 34.5 Vp-p (full-screen height) |
Input impedance |
60 Ω (pulse-echo mode);
150 Ω (pitch- catch mode) |
60 Ω (pulse-echo mode);
50 Ω (pulse-receive mode) |
System bandwidth |
0.5 MHz to 18 MHz (NOTE: The previously stated 0.6 MHz lower limit used a strict -3 dB attenuation for the cutoff frequency.) |
0.25 MHz to 28 MHz (–3 dB) |
Beamforming |
Scan type |
Sectorial or linear |
Group quantity |
1 |
Data Acquisition |
PA Channels |
UT Channel |
Effective digitizing frequency |
Up to 100 MHz |
100 MHz |
Maximum pulsing rate |
Up to 6 kHz (C-scan) |
Data Processing |
PA Channels |
UT Channel |
Number of data points |
Up to 8,192 |
Real-time averaging |
PA: 2, 4, 8, 16 |
UT: 2, 4, 8, 16, 32, 64 |
Rectifier |
RF, full wave, half wave +, half wave – |
Filtering |
3 low-pass, 3 band-pass, and 5 high-pass filters |
3 low-pass, 6 band-pass, and 3 high-pass filters (8 low-pass filters when configured in TOFD) |
Video filtering |
Smoothing (adjusted to probe frequency range) |
Data Visualization |
A-scan refresh rate |
A-scan: 60 Hz; S-scan: 60 Hz |
Data Synchronization |
On internal clock |
1 Hz to 6 kHz |
On encoder |
On 2 axes: from 1 to 65,536 steps |
Programmable Time-Corrected Gain (TCG) |
Number of points |
16: One TCG (time-corrected gain) curve per focal law |
Maximum slope |
40 dB/10 ns |
Alarms |
Number of alarms |
3 |
Conditions |
Any logical combination of gates |
The OmniScan SX meets or exceeds the minimum instrumentation and software requirements as specified in ASME, AWS, API, and EN codes
Inspecting Welds with the OmniScan® SX Flaw Detector