The Discovery Hybrid Rheometer (DHR) from TA Instruments can now characterize the behaviors of powders during storage, dispensing, processing, and end use, thanks to the Powder Rheology Accessory.
Quantitative assessments of the dynamic flowability and shear characteristics of the consolidated powder speed up the process of product development.
The detection of unexpected behavior in new formulations or incoming raw materials helps producers prevent production problems on a broad scale. Granular-level insights into changes in powder shape also help producers find solutions to difficult processing concerns.
Features and Benefits:
- Walk-up usability for every operator – TRIOS Powder test forms streamline routine test methods while enabling complete customizability
- Simplified data interpretation with optional Powder Analysis software, reporting quantitative key performance indicators in one click
- Flexibility to switch from liquid or solid samples to powders in less than 10 seconds, keeping pace with rapidly changing testing needs
- Measurements of powder behavior during processing, dispensing, storage and end-use with interchangeable tools for dynamic flowability and shear properties
- Repeatable results enabled by fast, easy intuitive sample loading and automated conditioning protocols
Repeatable Sample Loading
The production of reproducible powder samples is essential for accurate results. Sample-to-sample variability is reduced to as little as 0.2% by the accessory’s special loading tools and automated conditioning methods.
Flow Cell
To report unconfined and confined Total Flowability Energy, an impeller rotor is rotated helically through the powder while measuring torque and force.
Flow Cell Volume: 21.2 mL
Shear Cell
The powder is combined in a serrated cup and plate and gradually sheared until yield under varied normal stress is obtained, reporting cohesiveness, yield strength, flow function, and other characteristics.
Shear Cell Volume: 13.1 mL
ASTM D7891
Formulation
Formulators often seek insight into bulk powder behavior during development. During scale-up, unanticipated processing problems could arise, necessitating re-formulation and delaying the marketing of the product.
Powder Rheology Insights
To prevent future large-scale issues, powder rheology measurements on tiny lab-scale samples (less than 25 mL) show the effects of formulation adjustments on processability and performance.
Characterizing Effects of Additives on Powder Shear Properties
The necessary ingredients must be included in formulations for them to achieve the best rheological behavior. Even at very low concentrations, a new ingredient can alter the bulk properties.
The Powder Shear Cell is sensitive to these changes, as is shown by measuring sand before and after blending with 5% silicone oil. Under low normal stress, this modest increase has a significant impact on behavior, boosting cohesion and yield strength by a factor of 10. Major Principal Stress, which gauges the amount of stress that can be consolidated, is unaltered.
When adjusting all powder formulations to satisfy performance requirements, Powder Shear testing quantifies the well-known effect of soaking sand to build a sandcastle.
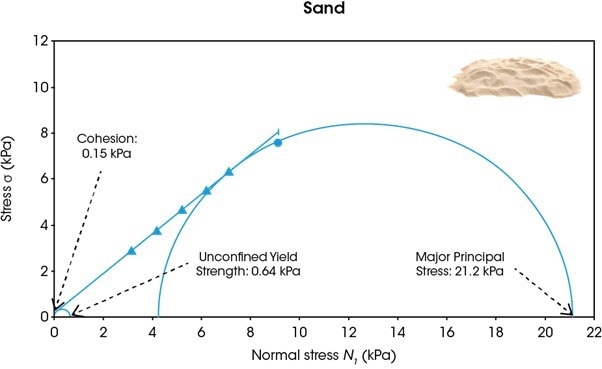
Image Credit: TA Instruments, Inc.
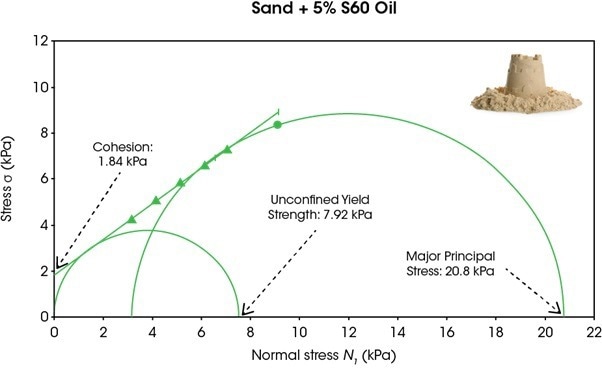
Image Credit: TA Instruments, Inc.
Storage
To provide reliable, regulated dispensing and prevent obstructions, rat-holing, or avalanching, hoppers and silos must be tailored to the characteristics of the powder being used.
Powder Rheology Insights
Consolidated powder shear measurements provide information on the following parameters: cohesion, unconfined yield strength, major principal stress, flow function, and angle of internal friction.
Stability
When mixed or stored for a long time, powder morphology can change. Processing performance is affected by instability, which lowers the caliber of the finished product.
Powder Rheology Insights
Inconsistent active ingredient dosage is caused by changes in agglomeration, caking, or segregation of blends, which are detected by flowability testing.
Processing
In the production process, the powder goes through several steps including feeding, mixing, granulating, and milling. Continuous flow is necessary for successful processing at every level to maintain production.
Powder Rheology Insights
In both confined and unconfined settings with a range of flow speeds, flow energy measurements forecast processability at crucial production phases.
Impact of Lactose Morphology on Flowability During Processing
Critical process parameters (CPP) are impacted by the excipients used in pharmaceutical powders for solid dosage tablets. Although lactose is frequently employed in pharmaceuticals, particle shape has a significant impact on rheological behavior.
Compared to the smooth, spherical particles of spray-dried lactose, the jagged, irregular particles of milled lactose display increased flow resistance due to interlocking. The Powder Flow Cell was utilized to evaluate both materials over a variety of speeds, highlighting the total flow energy increases at slower rates for milled lactose, predicting insufficient flow rates during dispensing or mold filling
Pre-screening CPPs, like flowability, help to prevent expensive production problems and guarantee product quality.
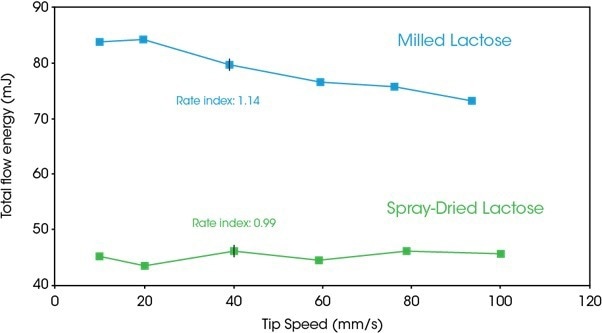
Image Credit: TA Instruments, Inc.
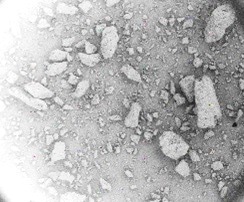
Milled. Image Credit: TA Instruments, Inc.

Spray-Dried. Image Credit: TA Instruments, Inc.
End Use
Food, personal care products, and consumer goods must adhere to consumer expectations. Consumer acceptance is compromised by powder caking or agglomeration, which affects dispensing.
Powder Rheology Insights
Powder rheology studies the effects of storage conditions such as consolidation or ecological factors and measures dispensing behavior directly.
Powder Rheology for the Discovery Hybrid Rheometer
Video Credit: TA Instruments, Inc.