Oct 18 2007
When engineers design a seal for feedthroughs and other electrical connectors, four general classes of material are evaluated. At the low end, a simple epoxy or glue may suffice. Alternatively, a mechanical seal with an elastomer o-ring can provide a somewhat more robust solution. For more demanding applications, glass seals are effective in preventing leakage during severe changes in temperature, pressure and humidity.
The highest performance electrical seal systems employ ceramics for exceptional resistance to thermal and mechanical shock, as well as corrosion. However, the superior performance of ceramic versus glass comes at a cost. The ceramic material is typically more expensive than glass and ceramic-to-metal seals require more sophisticated engineering and more complex manufacturing processes.
Therefore, the Alberox Products business of Morgan Advanced Ceramics (MAC), a world leader in the manufacture of ceramic-to-metal assemblies, recommends the use of ceramic seals in situations where glass seals fail to meet demanding performance requirements of an application. For example: high resistance to thermal and mechanical shock is necessary for many aerospace applications; exceptional corrosion resistance and biocompatibility is required by medical implant devices; and superior dielectric properties are critical to high voltage and high current laser applications.
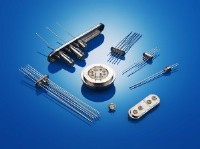
Ceramic-to-metal seals have a number of properties that allow for a more robust, durable hermetic seal and better electrical insulation than glass-to-metal seals. Alberox Products constructs seals primarily with 95% alumina (AL-500R), 97.6% alumina (AL-300R), and 99.5% alumina (AL-995R), as well as 100% pure sapphire and ruby. The polycrystalline alumina materials, such as AL-995, are favored in applications requiring a good heat sink. Sapphire and ruby are single-crystal formulations used for some medical implants and other high-purity applications. Alberox Products also makes ceramic-to-metal assemblies composed of Aluminum Nitride, Zirconia, Silicon Carbide, and Silicon Nitride.
Properly designed ceramic-to-metal seals are able to maintain hermeticity in a variety of harsh conditions, such as high and low (cryogenic) temperature, corrosive, high pressure, and high vacuum environments. The industry standard leak rate for ceramic-to-metal seals is 5x10-9 cc/sec, as tested by Helium mass spectrometer leak testing, which represents at least one order of magnitude lower leak rate (better leak tightness) than the best glass seals.
Ceramic-to-metal seals not only remain stable at extremely high and low temperatures, but they are able to withstand severe thermal shock and repeated thermal cycling. Ceramic functions as an excellent electrical insulator at very high temperatures, unlike glass, which conducts more electricity at elevated temperatures.
Another advantage of ceramic-to-metal seals is their high mechanical strength. Compared to glass, ceramics are less likely to fracture when subjected to high vibration and high g-load conditions. An additional problem for glass is the tendency of a meniscus forming at the surface, leading to small pieces breaking off ¡V an obviously undesirable situation for medical implants and other applications where impurities and contaminants are problematic. Ceramic is also more corrosion-resistant than glass, both in acidic and alkaline environments.
Ceramic-to-metal seals employ brazing to join the ceramic and metal components. The brazing process produces a strong bond and an excellent seal. Brazing works well with metals and alloys to which glass does not bond well. For example, it is difficult to bond glass to copper, which is desired for its electrical conductivity, or nickel, which is favored for its superior temperature resistance. Ceramic-to-metal seals bond well to copper and Cu alloys (CuNi) and to nickel and Ni alloys (e.g. MonelR, AlumelR, NialR).
The presence of brazing metal between the base metal and the ceramic substrate also accounts for the increased robustness of the system, compared to glass seals. The brazing material is more flexible than the ceramic, absorbs some mechanical shock, and helps mitigate any mismatch between the thermal expansion of the ceramic and the base metal. In contrast, the relatively rigid and brittle glass seals are positioned in direct contact with the metal substrate without the benefit of any interstitial brazing material.
Ceramic-to-metal assemblies play a critical role in implantable electronic devices. In the forty-five years since the first cardiac pacemaker was successfully implanted in the U.S., researchers and doctors have created a wide array of implantable electronic devices including defibrillators, cochlear implants and neurostimulators.
For example, medical device companies are testing neurostimulators that pulse various nerves to treat particular medical conditions: the hypoglossal nerve to treat sleep apnea, the sacral nerve to treat bowel disorders, the stomach to treat obesity, the thalamus to treat epilepsy, the vagus nerve to treat chronic depression, and other regions of the deep brain to treat migraines and obsessive-compulsive disorder.
These devices increasingly rely on components utilizing ceramics, including the feedthroughs that allow electricity to pass in or out of the implanted device in order to sense what is going on in the body and/or to administer an electrical charge when needed. A feedthrough can also be used to administer drugs to the patient. The ceramic substrate of the feedthrough acts as an insulator, electronically isolating the pins from each other.
Feedthroughs for implanted devices must be hermetic, with a leak-tight seal around each pin. A braze material, typically 99.99% gold, is used to join each metal pin to the ceramic insulator. To ensure the braze material adheres securely, Morgan Advanced Ceramics employs a process known as ¡§sputtering,¡¨ in which the surface of the ceramic is prepared for brazing by the application of a thin film of biocompatible metal, via physical vapor deposition (PVD).
Developers of new and improved implantable medical devices continually demand smaller and more complex components. For example, Alberox Products has created a one-inch diameter ceramic feed-thru for drug delivery applications that houses 104 separate pins. Voltages pass through each pin activating different combinations of switches and, as a result, a greater number or more complex combination of drugs can be administered at any given time.
To prepare the ceramic for brazing, the surface must be metallized. Alberox Products primarily employs two different metallizing techniques. A refractory metallizing technique applies a specially-formulated, proprietary molybdenum-manganese based ink that creates a metallic coating capable of being nickel-plated.
All components of the ceramic-to-metal assembly must be carefully matched and well-integrated. A diversified company, like Morgan Advanced Ceramics, can ensure quality and consistency by internally sourcing ceramics, alloys and brazing materials, and by drawing on this varied expertise to provide integrated, complete assemblies, fully tested and with total materials traceability.