Feb 8 2009
This year, BASF is once again showcasing new products and applications in the realm of engineering plastics, styrenics, polyurethanes and foams at the technical conference “Plastics in Automotive Engineering” organized by the Association of German Engineers (VDI) to be held on March 25 and 26, 2009 in Mannheim, Germany. These products include not only hydrolysis-resistant Ultradur® (PBT), tribologically optimized Ultrason® (PESU) and particularly low-squeaking Neopolen® (EPP) but also the following innovations:
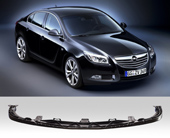
Safety for the Opel Insignia
Following in the footsteps of the Opel Corsa, now the Opel Insignia also has a lower bumper stiffener (LBS) made of a crash-optimized BASF polyamide, namely, Ultramid® B3WG6 CR. This part – developed by BASF using its expanded computer program for Integrative Simulation ULTRASIM™ – meets stringent requirements in terms of pedestrian safety. Other innovative components used in the Opel Insignia were also created with BASF plastics and know-how.
Easy-flow blend
Terblend® N – BASF’s ABS/PA blend – has long been known to be ideal for demanding automobile interiors, dispensing with the need for complex and expensive coatings. Two new members have now joined this product family: both bear the suffix EF, which stands for excellent flow. Thanks to its superior flow behavior, Terblend N NM-21 EF is even easier to process, so that large and intricate visible parts, center consoles in car interiors and motorcycle fairing parts can now all be manufactured with an even better surface quality. The other novelty, glassfiber-reinforced Terblend N NG-02 EF, combines this easy flowability with high mechanical strength. Moreover, its impact resistance makes this styrenic blend so sturdy that it lends itself very well for thin-walled parts that are subjected to high loads.
High Speed for light colors
BASF’s Ultramid® High Speed assortment has also been expanded. New variants of the easy-flow polyamides (PA66) such as Ultramid A3EG7 High Speed will be available as of April 2009, in sample quantities. Thanks to their light intrinsic color, these products are suitable for any of the customer’s coloring – an aspect that is often needed with electronic components and connectors. These plastics also entail the classic advantages of the High Speed family. The easy flowability ensures that even thin ribs can be reliably filled. On top of it all, the lower injection pressure exerts considerably less stress on filigree inserts and on the mold during the injection procedure.
Ultraform rendered electrically conductive with nanoparticles
Ultraform® N2320 C owes its extraordinary electric conductivity to carbon nanoparticles. The first serially produced part made of this new BASF polyoxymethylene (POM) will be introduced at the VDI event. It is a fuel filter housing from Bosch, designed to comply with the SAE J1645 standard (separate news release to be published in March).
Dual-clutch transmissions – the next generation
BASF’s highly oil-resistant Ultramid® A3WG6 is being used by the manufacturer for the integrated controls in the new generation of dual-clutch transmissions. Transmission controls are complex mechatronic components that are positioned directly on the transmission, where they are surrounded by hot oil (separate news release to be published in March).
Miramid: polyamides that are even more tailor-made to customers’ needs
BASF Leuna GmbH has two new products to report: Miramid® B3EG3 GIT, a PA 6 with excellent surface quality, is now available in the interior colors (trim colors) used by automotive manufacturers. This material has already gone into serial production for the beige and black seat-adjustment levers of the Opel Insignia. Up to now, GIT grades had been considered to be difficult to color. Work is also under way on Miramid grades with improved tribological properties. The first variant of this new family is Miramid B3EG4 TR.
Polyurethanes from Elastogran GmbH
Lightweight but not to be taken lightly: the PUR car body of the Artega GT
New in the fast lane: the Artega GT, weighing a mere 1100 kilograms, is setting new standards in its class with its power-weight ratio of 3.72 kg/HP. But that is not all: this new German sports car is the world’s first serially produced vehicle whose body is made entirely of polyurethane (PUR) – a clear commitment to lightweight construction. The combination of several PUR materials from the Elastolit® family, which has outstanding mechanical properties, makes this streamlined two-seater a true lightweight while also offering additional advantages in terms of cost and safety.
Elastoclear: scratch-proof polyurethane coating for wood trim
For many years now, wood finishes made with Elastoclear® have been used for the interior trim of luxury vehicles. They stand out for their high transparency and extremely low emission levels as well as for their unique depth effect. The newly developed generation of Elastoclear products exhibits not only the familiar benefits of this line but also considerably higher scratch-resistance. Elastoclear wood coatings are two-component PUR systems on the basis of aliphatic isocyanates.
Cellasto-Ultramid combination for shock absorber bearings
Annoying shock absorber rumbling and the tendency to shudder: for years, the tried and true Cellasto® shock absorber bearings have come to the rescue, ensuring greater driving comfort and better driving dynamics. The combined use of Cellasto and Ultramid® CR (PA) accounts for major advances in the realm of shock absorber integration. To put it in a nutshell: 30% weight reduction, improved shock absorption behavior and even better acoustic insulation.