Apr 7 2009
NASA has chosen the material for a heat shield that will protect a new generation of space explorers when they return from the moon. After extensive study, NASA has selected the Avcoat ablator system for the Orion crew module.
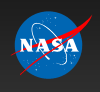
Orion is part of the Constellation Program that is developing the country's next-generation spacecraft system for human exploration of the moon and further destinations in the solar system. The Orion crew module, which will launch atop an Ares I rocket, is targeted to begin carrying astronauts to the International Space Station in 2015 and to the moon in 2020.
Orion will face extreme conditions during its voyage to the moon and on the journey home. On the blistering return through Earth's atmosphere, the module will encounter temperatures as high as 5,000 degrees Fahrenheit. Heating rates may be up to five times more extreme than rates for missions returning from the International Space Station. Orion's heat shield, the dish-shaped thermal protection system at the base of the spacecraft, will endure the most heat and will erode, or "ablate," in a controlled fashion, transporting heat away from the crew module during its descent through the atmosphere.
To protect the spacecraft and its crew from such severe conditions, the Orion Project Office at NASA's Johnson Space Center in Houston identified a team to develop the thermal protection system, or TPS, heat shield. For more than three years, NASA's Orion Thermal Protection System Advanced Development Project considered eight different candidate materials, including the two final candidates, Avcoat and Phenolic Impregnated Carbon Ablator, or PICA, both of which have proven successful in previous space missions.
Avcoat was used for the Apollo capsule heat shield and on select regions of the space shuttle orbiter in its earliest flights. It was put back into production for the study. It is made of silica fibers with an epoxy-novalic resin filled in a fiberglass-phenolic honeycomb and is manufactured directly onto the heat shield substructure and attached as a unit to the crew module during spacecraft assembly. PICA, which is manufactured in blocks and attached to the vehicle after fabrication, was used on Stardust, NASA's first robotic space mission dedicated solely to exploring a comet, and the first sample return mission since Apollo.
"NASA made a significant technology development effort, conducted thousands of tests, and tapped into the facilities, talents and resources across the agency to understand how these materials would perform on Orion's five-meter wide heat shield," said James Reuther, the project manager of the study at NASA's Ames Research Center at Moffett Field, Calif. "We manufactured full-scale demonstrations to prove they could be efficiently and reliably produced for Orion."
Ames led the study in cooperation with experts from across the agency. Engineers performed rigorous thermal, structural and environmental testing on both candidate materials. The team then compared the materials based on mass, thermal and structural performance, life cycle costs, manufacturability, reliability and certification challenges. NASA, working with Orion prime contractor Lockheed Martin, recommended Avcoat as the more robust, reliable and mature system.
"The biggest challenge with Avcoat has been reviving the technology to manufacture the material such that its performance is similar to what was demonstrated during the Apollo missions," said John Kowal, Orion's thermal protection system manager at Johnson. "Once that had been accomplished, the system evaluations clearly indicated that Avcoat was the preferred system."
In partnership with the material subcontractor, Textron Defense Systems of Wilmington, Mass., Lockheed Martin will continue development of the material for Orion. While Avcoat was selected as the better of the two candidates, more research is needed to integrate it completely into Orion's design.