Mar 4 2014
Arkema is launching its first range of liquid thermoplastic resins under the brand Elium®, which is transformed using the same processes as composite thermosets. The exciting new technology won an award in 2013 at JEC and is being used in 2014 because it is lightweight, cost-effective and recyclable.
Elium® resins polymerize quickly and can be used to design structural parts as well as aesthetic elements in a number of applications anywhere from the automotive and transportation industries to wind power, athletic equipment and the building sector.
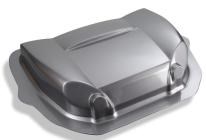
"The name Elium® is a great symbol that stands for an innovative brand in the community of material weight reduction. Elium® resins are multifunctional, lightweight, easy to use in manufacturing and high-performance," says the product range's manager, Sébastien Taillemite. "They are based on conventional technologies and processes that processors were already using – an undeniably value-added product."
Elium® is it an easy resin to use for lightweight and resilient composite parts
Composite parts made from Elium® are 30-50% lighter than the same parts made from steel, but offer the same resistance. When combined with Arkema Luperox® peroxide initiators, Elium® can be molded into complex design forms for composite parts and perfectly blends with glass or carbon fibers. As a bonus, it is also compatible with conventional thermosetting resin transformation technologies (Resin Transfer Molding, Infusion, Flex-molding), which cuts down the costs of transformers.
Elium® is designed for high-performance parts that are recyclable and easy to thermoform
Unlike unsaturated polyesters, Elium® resins do not contain styrene. And because of their thermoplastic properties, they can be used to design composite parts that are easily thermoformed and recyclable with comparable mechanical performance to epoxy parts. Parts made from Elium® assemble effortlessly by welding and/or gluing, especially with adhesives from Arkema's subsidiary, AEC Polymers.
Parts made from Elium® cost less to manufacture than other thermoplastic technologies
Elium® technology reduces the cost of long staple thermoplastic composite parts. Three compelling factors contribute to its cost-effective advantage: the resins are easy to use in conventional thermoset resin processes, it transforms at room temperature and it does not contain any fabricated products like organo-sheets.
A comprehensive composite line that largely solves the challenge to find lighter materials.
Out of a growing interest in biomaterials and recycling and to meet the insatiable demand of composite manufacturers for higher performance, Arkema has developed resins and polymers that offer the perfect solution to the quest for lighter materials.
In addition to the Elium® range, Arkema is developing a polyetherketoneketone (PEKK) called Kepstan® to replace metal in extreme conditions (offshore, aviation), the Rilsan® range, a high-performance powdered or granulated polyamide that is 100% bio-sourced and makes thermoset composites resistant to abrasion and shock at very high or low temperatures.
Additives like Nanostrength®, Orgasol® polyamides and Luperox® organic peroxides significantly improve the natural resistance properties of composites.
Lastly, AEC Polymers, an Arkema subsidiary specialized in structural glues and adhesives, markets BlackManba® waterproof sealant adhesives and SAF® structural adhesives – imperative bonding agents for complex composite assemblies.
Elium® technology and all of Arkema's composites will be displayed at JEC Europe 2014 on March 11-13 at booth D42 in Hall 7.2.