Oct 17 2014
For more than 50 years injection moulding and chrome plating specialist Borough, has built a reputation for the quality of both its components and its service.
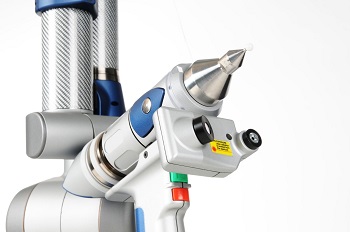
Ensuring the well-earned reputation is not only maintained, but enhanced, Borough has again made significant investment in new technology, with the purchase of an Edge ScanArm from FARO, the world’s most trusted source for 3D measurement technology.
Featuring SmartArm technology, the first ever integrated personal measurement assistant, the Edge with its built-in touchscreen and on-board operating system, sets new standards for portable measuring by providing stand-alone basic measurement capability. It also incorporates Enhanced Scanning Technology, which improves the ability to scan challenging surfaces, something regularly encountered with Borough’s long list of automotive components.
Operations Manager, Peter Oldfield commented: “The FaroArm is a portable co-ordinate measuring machine that allows easy verification of product quality by performing 3D inspections, tool certifications, CAD comparison, dimensional analysis and reverse engineering.
“We can now check engineering changes to the mould by mounting the FaroArm on the mould, verifying the altered area and producing a scan. The scan is laid over the original design to determine if the correct changes have been made or if further adjustments are necessary. This is especially important since Borough’s main goals are to reduce lead times, improve mould performance and help reduce costs to our customers.
“Previously we have had to outsource this service, but with our growing order book and determination to cut deadlines, not quality, now was the right time to invest. The quality of the finished product is dependent upon the design and condition of the original moulding and although it’s easy to claim your products are high quality, it helps when you can prove it within minutes.”
Borough is expected to offer use of its new measuring equipment to smaller firms, keen to take advantage of the speed and accuracy of the system to meet the increasing needs for quality and verification in manufacturing.
This latest investment follows quickly on the heels of purchasing new ENGEL e-motion 300, injection moulding machines, the first developed in Europe to use a sophisticated, electrical low-clamping force and tie-bar-less technology.
Borough Managing Director, David Coombes, said: “This latest addition to our mould shop is the perfect unit for the ever-growing demands of the dynamic markets we service and it’s a machine we’re confident will also help cut our already low reject rates.
“The new machine helps us achieve the greater output demanded by our growing client list, thanks to the advanced tie-bar-less design and our use of robotic arms to remove the moulded components; we have really increased our production speeds without lowering the quality of our mouldings or chrome plating.
“Whilst investing in new machines, we decided it was the right time to also install a large jib crane to help speed up the changing of tools across machines in the mould shop. And although digging its foundations initially made a mess of the factory floor, it’s certainly made up for it in increased productivity.
“These latest investments demonstrate our commitment to the future and our determination to meet the challenges of an evolving market, maintain a competitive edge and drive the business forward through the application of appropriate innovation.”