Feb 23 2015
Engineers at NASA are exploring an advanced composite that could be used to create more powerful rocket boosters.
Standing more than two stories tall and almost 8 feet in diameter, the composite test structure was pressurized with water until it burst. Image Credit: Orbital ATK
In March, NASA plans to test the solid rocket booster designed for the Space Launch System (SLS) rocket.
The rocket launch process creates immense strain for the structure of the rocket booster itself.
Engineers have conducted a test to determine the ability of the materials used to withstand such strain.
The composite structure was subjected to high pressure to its breaking point. The data from these tests was then compared with the properties of currently used metallic booster cases.
In order to determine the loads that could be withstood by the composite material, the team performed a "case burst" test on a booster case that was 25ft in length and 92” in diameter.
The booster case was subjected to a pressure of 3,000lb/in², which is more than the actual pressure encountered under actual flight conditions. This immense pressure competely destroyed the booster casing.
Angie Jackman, SLS Spacecraft/Payload Integration and Evolution (SPIE) office at NASA's Marshall Space Flight Center, commented:
The test is very dramatic. When composites fail, it’s the glue or the resin that fails first -- not the fiber that fails. There’s a big boom, and it’s all spaghetti.
The engineers had caused intentional damage at multiple points on the booster case to observe how the damage affected the performance of the case. After the test, they found that in terms of performance, the damaged case performed on the same level as the intact case. This showed that even in a damaged condition, the composite case was able to withstand the harsh conditions of the launch.
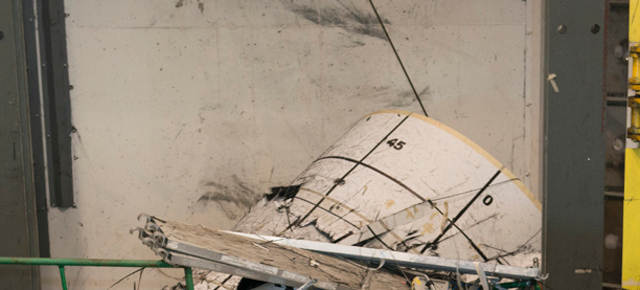
Composite rocket booster structure after the "case burst test". Image credit: Orbital ATK
Orbital ATK of Promontory, Utah had conducted the test. Orbital ATK had manufactured the solid rocket boosters that were flown on the space shuttle. This company is to provide the boosters for the initial SLS flights.
The test validated the model for the composite material’s strength. The failure of the case was within 1% of the pretest estimates. The data about the case failure was provided by 112 channels of instrumentation. Composite materials are comparatively less in weight when compared to steel cases and they would deliver better payload performance. This test is an effort to create a composite case design that would be comparatively lighter, more affordable and stronger than conventional steel cases.
The initial configuration of the rocket is designed to deliver 77t to low-Earth orbit. After the initial SLS flights are completed, the configuration of this rocket is to be upgraded so that it would be capable of launching 143t. More powerful boosters are to be used to achieve this capability.
For the future of human space exploration, NASA is collaborating with industry partners to test technologies for developing solid or liquid rocket boosters.
A Composite Booster Gets a Burst of Energy (Real Time)