A technician cleans an infrared camera from the deck of the USS Cleveland (LPD 7). The U.S. Naval Research Laboratory (NRL) is making transparent ceramics, called spinel, that could one day replace the glass in military imaging systems. (Photo: U.S. Navy/Mass Communication Specialist 2nd Class Michael Russell)
A team of researchers headed by Dr. Jas Sanghera of the U.S. Naval Research Laboratory (NRL) have been involved in a research spanning over 10 years to create transparent spinel, a special ceramic which is as tough as armor, scratchproof and unbreakable.
Spinel is actually a mineral, it's magnesium aluminate. The advantage is it's so much tougher, stronger, harder than glass. It provides better protection in more hostile environments—so it can withstand sand and rain erosion.
Dr. Jas Sanghera
The high durability of spinel ensures that even a thin layer can provide higher performance in comparison to glass.
For weight-sensitive platforms-UAVs [unmanned autonomous vehicles], head-mounted face shields—it's a game-changing technology.
NRL used the sintering technique to create transparent spinel. Sintering is a low-temperature method and the size of the spinel pieces will depend upon the size of the press.
"Ultimately, we're going to hand it over to industry," says Sanghera, "so it has to be a scalable process." In the lab, the team built pieces measuring eight inches in diameter. "Then we licensed the technology to a company who was able then to scale that up to much larger plates, about 30-inches wide." NRL also used the sintering method to build optics in many shapes, "conformal with the surface of an airplane or UAV wing," based on the shape of the press.
In addition to being tougher, stronger, harder, Sanghera says spinel has "unique optical properties; not only can you see through it, but it allows infrared light to go through it." That means the military, for imaging systems, "can use spinel as the window because it allows the infrared light to come through."
NRL also plans to use spinel for windows on lasers functioning in maritime and other aggressive environments. "I've got to worry about wave slap and saltwater and things like that, and gun blasts going off—it's got to be resistant to all that. And so that's where spinel comes into its own," says Sanghera.
Says Sanghera, "Everything we do, we're trying to push the mission. It's designed to either enable a new application, a new capability—or enhance an existing one."
It is possible to mine spinel as a gemstone. For instance the famous Black Prince's Ruby, is in fact spinel having a color dopant. The NRL team has managed to even synthesize an ultra-high purity spinel powder, and other artificial versions have been made available in the market. "The precursors are all earth abundant, so it's available in reasonably low cost," says Sanghera.
The spinel created by NRL is a polycrystalline material, or numerous crystal particles pressed together. Whereas with glass, "A crack that forms on the surface will go all the way through," spinel might chip but it won't crack. "It's like navigating through the asteroid belt, you create a tortuous path: if I have all these crystals packed together, the crack gets deflected at the hard crystals: you dissipate the crack energy."
Initially, when scientists began trying to make glass-like spinel, instead of a press they used a crucible. "A big problem with growing crystals is that you have to melt the starting powder at very high temperatures, over 2000 degrees Celsius," says Sanghera. It's expensive to heat a material that high, and additionally, "the molten material reacts with the crucible, and so if you're trying to make very high quality crystals, you end up [with a] huge amount of defects."
Therefore Sanghera and his team turned to sintering. "You put the powder in [a hot press], you press it under vacuum, squash this powder together—and if you can do that right, then you can get rid of all the entrapped air, and all of a sudden it comes out of there clear-looking."
In case the press has flat plates, the spinel will also be flat shaped. "But if I have a ball and socket joint, put the powder in there, I end up with a dome shape," says Sanghera, "so we can make near net shape product that way."
NRL is not the first laboratory to use sintering. However, previous attempts had yielded "a window where most of it would look cloudy, and there would be an odd region here and there—about an inch or so—that was clear, and that would be core-drilled out."
Subsequently they noticed another issue with the sintering aid they were putting into the spinel powder.
It's about one percent of a different powder, in this case lithium fluoride," says Sanghera. This "pixie dust" is meant to melt and "lubricate the powder particles, so there's less friction, so they can all move together during sintering." They were putting the powders together in shakers overnight, but, "The thing is, on a scale of the powder, it's never mixed uniformly.
By comprehending the issue, the team was able to arrive at an innovative solution for enabling uniform mixing. Now, "there's only one pathway for densification," and the processed spinel will emerge clear across the press.
In order to further enhance the optic’s quality, "You can grind and polish this just like you would do gems," says Sanghera. This process is the most costly step. "One of the things we're looking at is, how do we reduce the finishing cost?" The surface of the press gets imprinted onto the glass. "If we can improve upon that," he says, "make that mirror finished, then—and so that's where we get into a little bit of IP [intellectual property], is what's the best way to do that?"
"Cost is a big driver, and so it's important for us to make product that can be affordable" especially for both the Department of Defense (DoD) and private sector.
"There are a lot of applications," says Sanghera. He lists out consumer electronics such as smart phone, and watches as examples. Spinel will find use in the military as a transparent armor for face shields and vehicles.
For instance, the currently used "bullet-proof" window consists of many plastic and glass layers measuring about five inches in thickness. "If you replaced that with spinel, you'd reduce the weight by a factor of two or more," says Sanghera.
The military will also adapt the spinel to enhance protection of visible and infrared cameras on aircraft and other platforms.
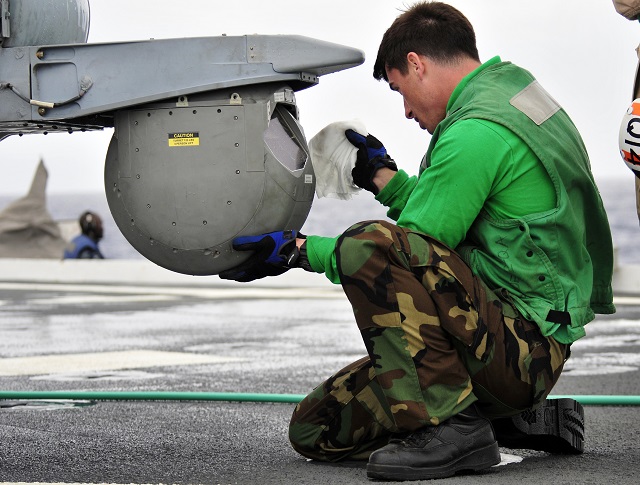
Image Credit: U.S. Navy/Mass Communication Specialist 2nd Class Michael Russell
Glass does not transmit infrared, thus current optics are made of "exotic materials that are very soft and fragile," and consist of several layers to make up for color deformation.
"So that's what we've been doing now, developing new optical materials," says Sanghera. Spinel windows could possess the ability to protect sensors on space satellites as well, which is being studied by Sanghera.
"You could leave these out there for longer periods of time, go into environments that are harsher than what they're encountering now, and enable more capabilities," he says."
NRL will also adapt the spinel for next generation (NEXTGEN) lasers. "Lasers can be thought of as a box comprised of optics," he says. "There's passive and there's active components: passive is just a protective window; active is where we change the color of light coming out the other end."
In the case of passive laser applications such as exit apertures or windows, high quality is paramount.
"That window, if it's got any impurities or junk, it can absorb that laser light," says Sanghera. "When it absorbs, things heat up," the window could break. Sanghera’s team has clearly illustrated the functions of ultra high purity spinel powder, which they created in NRL clean rooms. They also illustrated how sintering can be used to create a high quality laser even with other materials for active laser applications. The other materials instead of spinel can be yttria or lutecia doped with rare earth ions. NRL has managed to alter both types of laser materials and applications to suit industry purposes.
Sanghera joined NRL in 1988 after finishing his PhD in materials science at the Imperial College, London. "Little by little—talking to people, asking questions, going to conferences—you find out that what makes this place tick is solving problems," he says. "No two days are the same, it's very exciting."
Initially he experimented with glass, focusing on its optical fibers. His current success with spinel can be attributed to the persistence for purity and quality. "An optical fiber's very long: it can go from 1 meter to 100s of kilometers. Purity's very important, because if there's any junk in there, the light will either be absorbed or it can be scattered."
His lab is also involved in creating lightweight, economical fibers that can be applied for infrared countermeasures applications on helicopters and other platforms. By weaving it through the platform, "This fiber can remote the energy from the laser, which is inside the platform, to a device on the outside, which can then track and then shoot the laser beam out, confuse the missile."
He acknowledges, "In DoD, we are the premier place for development of fiber lasers. It's something we are heavily involved with, all the different types of fibers and configurations and materials required to enable these eye-safer and NEXTGEN lasers."
Sanghera explains that transition is happening, for example the improvement seen in the current capability by enhancing size, weight, and performance/power (SWAP); "But revolution is when you come up with some new idea, you just enabled completely new capabilities." He credits all this to the various disciplines NRL is known for. "We have a lot of smart people, we have a lot of what I call head-banging sessions, where we discuss new ideas and opportunities. If you don't ask the questions, you won't get answers and you won't stimulate new ideas."
He also credits a close relationship with industry and with those NRL serves. "We talk to the warfare centers, the systems people—so that what you're doing really is going to be of value. There's already the application there in mind, and we're just trying to solve that problem; so it's very focused in that sense."
References