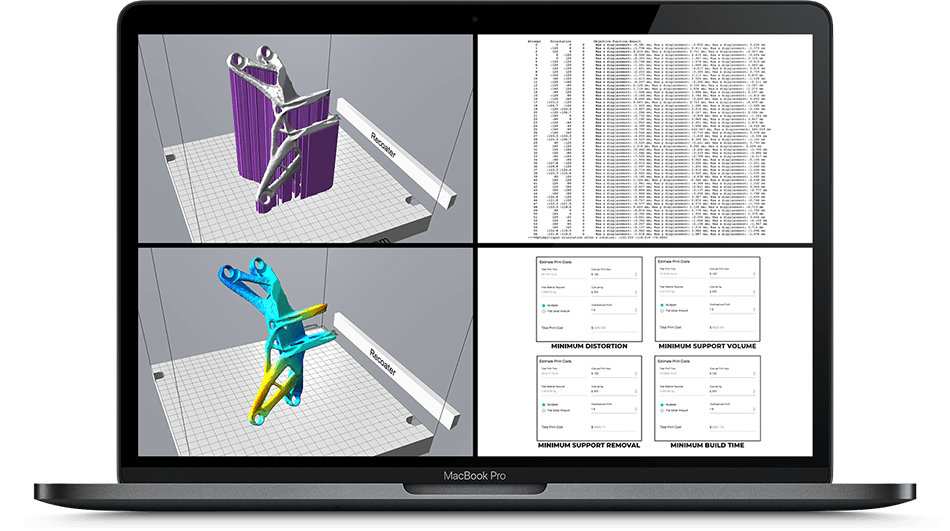
Insights into the optimal part build orientation in order to minimize supports, distortion, effort to remove supports, part material, and printing time. Image Credit: Atlas 3D
Last week it was announced that Siemens had signed an agreement to acquire Atlas 3D, adding its print preparation software for Direct Metal Laser Sintering (DMLS) 3D printers, Sunata, to its cache of additive manufacturing solutions.
A Strategic Partnership
The acquisition sees Europe’s largest industrial manufacturing company taking another step to strengthen its position as a leader in additive manufacturing, automation, and digitalization. For the Plymouth, Indiana-based Atlas 3D, it presents an opportunity to capitalize on a partnership that will see it play a fundamental role in expanding Siemens Xcelerator portfolio of additive manufacturing software.
Promoting an Industry Shift
The motivation behind the acquisition was initiated by the goals of Siemens Digital Industries Software to find a solution that can address the commonplace 3D printing errors caused by thermal distortion. It recognized the potential offered by Atlas 3Ds software innovation that automates optimal print and orientation calculations and offers necessary support structures in near real-time.
As a major player in the additive manufacturing space, well established in supplying cutting edge technologies to large enterprises, design firms, 3D printing service bureaus and CAD designers, this move will see Siemens and Atlas 3D provoking a significant advancement in the industry by making a problem-solving solution widely accessible.
The Software
Released in 2018, Sunata, Atlas 3D’s additive manufacturing software can reduce the rate of 3D print failures within high-volume production. Often, the production process can be dominated by design requisites, meaning that factors such as distortion, part orientation, and heat extraction uniformity can be overlooked.
Don’t just simulate it, SUNATA™ it!
To address this, Sunata uses its patent-pending Thermal Circuit Network (TCN) technology to enhance the process of optimization. The software has been developed to optimize build orientation and generate support structures automatically, significantly reducing failures in production.
To achieve this, the Sunata software applies thermal distortion analysis to additive manufacturing designs, resulting in a simple, fast, and automated way of optimizing production. The result is that, in addition to reducing errors, it cuts down on the reliance on analysts to perform simulations as they can be done by the designer. The plan for Siemens is to introduce this software into its online Additive Manufacturing Network, making it easily accessible to a wide range of clients.
The impact will be that designers are in control of the process of producing their designs. The software enables them to decide for themselves what the optimal way is of 3D printing the necessary parts with a high-quality result that can be confidently repeated. The software supports the 'right first-time' approach, minimizing the time, labor, and costs associated with errors in the additive manufacturing process.
Solving an Industry Problem
Companies operating in the 3D printing space are finding print failures a fundamental obstacle to achieving optimal productivity and manufacture success when aiming for high-volume production. Usually, new products are required to go through several rounds of design and analysis before the optimal build orientation and support structures can be identified.
This process is costly to companies, utilizing significant resources in terms of workers’ time and materials. What’s more, product designers often don’t have the skills to contemplate part orientation, distortion, and heat extraction uniformity, which is usually managed by an analyst or engineering specialist. Sunata is posed to change this, equipping designers with the software that automates this process for them.
Sunata brings something different to the additive manufacturing space, it’s been proven to deliver results up to one hundred times faster than comparable available build simulation solutions. It uses GPU-accelerated computing, which encompasses deep learning, analytics and engineering applications. Siemens and Atlas 3D look set to make an impact on the 3D printing industry, helping to advance its methods and offering a solution that will make manufacturers more efficient and profitable.
Disclaimer: The views expressed here are those of the author expressed in their private capacity and do not necessarily represent the views of AZoM.com Limited T/A AZoNetwork the owner and operator of this website. This disclaimer forms part of the Terms and conditions of use of this website.