The advent of printing technologies was a defining factor in the mass transmission and reproduction of information and knowledge. A paper in the journal ChemPhysMater considers new printing technology for use in supercapacitors.
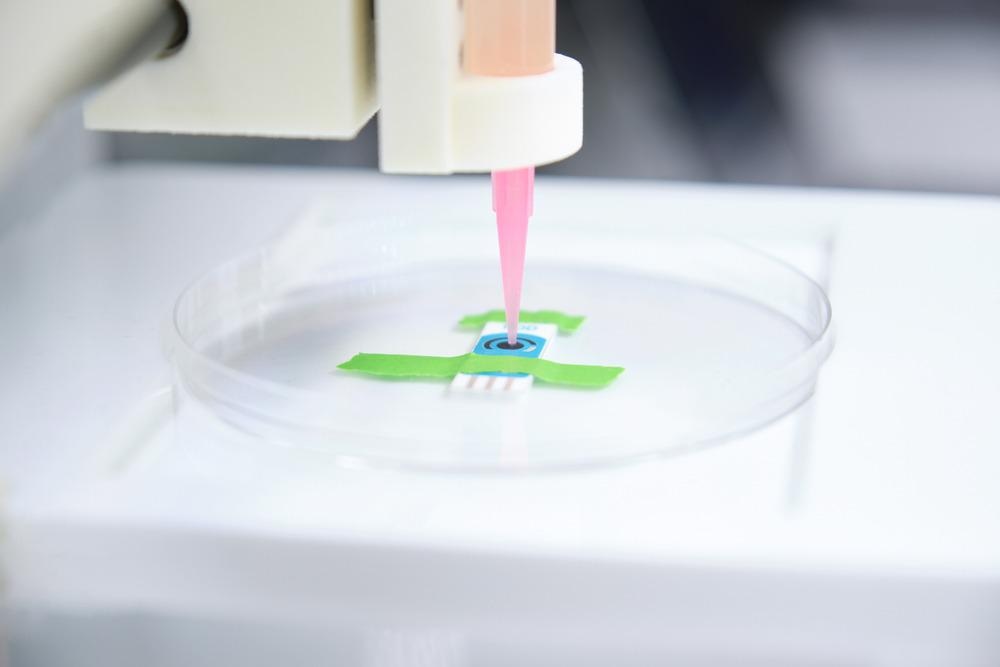
Study: Printable Electrode Materials for Supercapacitors, Image Credit: Ladanifer/Shutterstock.com
Contemporary, computer-controlled design and printing technology has taken these printing capabilities further than ever before, allowing a diverse array of printed materials to be produced, leading to a series of revolutionary breakthroughs in the manufacture of high-performance electrochemical energy storage systems using electrode ink printing systems.
It is now possible to formulate energy storage device components such as electrodes into functional inks, increasing the number of materials and devices suitable for use in energy storage – most notably in supercapacitors.
A review presented in the ChemPhysMater journal has provided a useful summary of these printing technologies, exploring the methods for designing and preparing electrode links, their application potential for use in supercapacitors, and an overview of future challenges and opportunities for this technology.
Supercapacitors (SCs)—also referred to as electrochemical capacitors—offer a range of advantages over conventional batteries. Their compact and thin size, flexibility, easy integration, and transparency make them an ideal option for a wide range of next-generation energy storage devices such as flexible and wearable electronics, storage backup systems, and consumer electronics.
SCs are not limited by the electrochemical charge transfer kinetics of batteries, meaning that they can accommodate extremely high charge and discharge rates while offering a working lifespan of more than one million cycles.
SCs are generally made up of electrolytes, high-performance electrodes, current collectors, and appropriate packaging materials. The most commonly employed electrode materials are robust, two-dimensional materials with large specific surface areas and excellent mechanical properties.
Producing SCs on an industrial scale requires a cost-effective means of producing large-area thin-film electrodes – a process that typically employs conventional microfabrication techniques, therefore severely hindering manufacturers’ ability to deliver economic, high-throughput production.
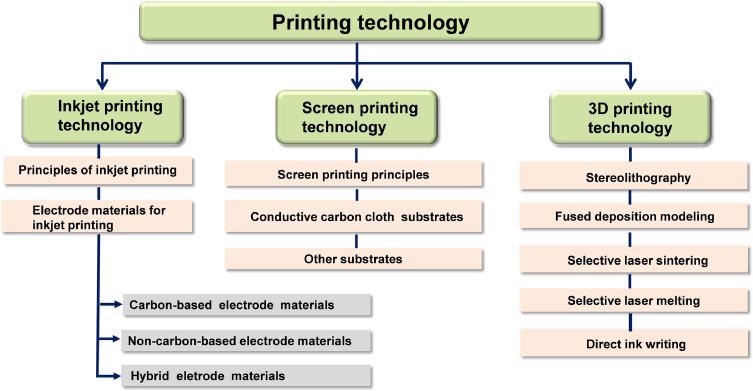
Summary diagram of printing technology. Image Credit: Yidan Gao et al., ChemPhysMater
Printing technologies could offer a viable solution to these cost and throughput challenges, having already demonstrated the flexibility and controllability in the fabrication of high-performance SC devices.
The position, geometry, film thickness, and conductivity of electrodes can all be controlled via printing, allowing manufacturers to optimize both device performance and design flexibility – key considerations in ensuring that SCs’ electrode materials offer the performance required for today’s demanding applications.
Materials used in the manufacture of electrodes have included carbon-based materials, conductive polymers, metal oxide/hydrogen-based materials, metal-organic frameworks (MOFs), and even nanocomposite functional materials.
In terms of SC electrode printing, three methods have thus far dominated this process: inkjet printing – a widely compatible method that uses a nozzle to deposit ink droplets onto a substrate; screen printing – a highly cost-effective method that deposits inks onto a substrate via openings in a mesh screen; and 3D printing (also known as additive manufacturing) – a recently developed method which sequentially builds up 2D layers to construct a 3D structure.
Any printing process used to manufacture SC electrodes must offer sufficient pattern resolution, design versatility, speed, performance, and the ability to accommodate a diverse array of printable materials.
Of these three frequently employed methods, 3D printing represents perhaps the most significant breakthrough in SC electrode manufacturing due to its potential to increase shape complexity while simultaneously simplifying manufacturing processes.
This will also help mitigate the most notable limitation of SCs – their low energy density, which stems from a lack of sufficiently fine electrode structures. 3D-printed electrodes also offer the key benefits of higher porosity and larger specific surface area, increasing the contact area between electrodes and electrolyte and subsequently significantly improving the electrochemical performance
Work is ongoing to develop fully-realized multi-material 3D printing systems able to accommodate the increasingly advanced printable materials used in printed components and devices.
While there have only been limited amounts of research into the use of printing technology to manufacture SC components thus far, this technology offers excellent potential and there is considerable scope for future developments in this area.
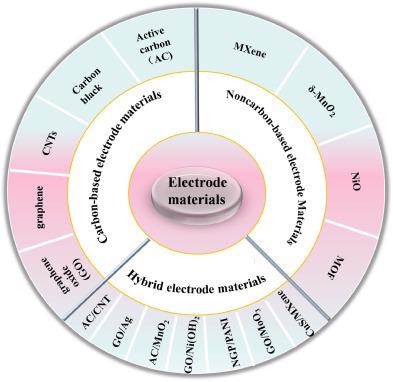
Summary of printable electrode materials. Image Credit: Yidan Gao et al., ChemPhysMater
As new developments such as 5G technology place higher and higher requirements on portable energy storage equipment, SCs offer an excellent opportunity to meet these needs.
Other major opportunities for the use of SCs and printed electrodes stem from the pressing need to move away from fossil fuel use and into the centralization of renewable energy sources. Clean energy is set to become the future of energy production, but sources such as water, solar, wind, and hydrogen can be impacted by external factors which lead to severe fluctuations in power generation.
Advanced battery storage – potentially via SCs – is key to ensuring the efficiency and consistency of these systems. Electrochemical energy storage devices remain the most promising candidates for these applications, not least because these are already widely employed in a number of everyday electronic devices.
Developments in printed electrode technology could be key to SCs meeting the growing demands of this technology.
Disclaimer: The views expressed here are those of the author expressed in their private capacity and do not necessarily represent the views of AZoM.com Limited T/A AZoNetwork the owner and operator of this website. This disclaimer forms part of the Terms and conditions of use of this website.
Source:
Yidan Gao, Xiaowen Guo, Ziming Qiu, Guangxun Zhang, Rongmei Zhu, Yizhou Zhang, Huan Pang, Printable Electrode Materials for Supercapacitors, ChemPhysMater, 2021, ISSN 2772-5715, https://doi.org/10.1016/j.chphma.2021.09.002. https://www.sciencedirect.com/science/article/pii/S2772571521000024