By Susha Cheriyedath, M.Sc.Reviewed by Skyla BailyNov 19 2021
A group of researchers from Finland has fabricated a piezoelectric composite at an ultra-low temperature using an organotitanate based precursor gel binder, which showed improved performance. This research has been published in the journal Composites Part B: Engineering.
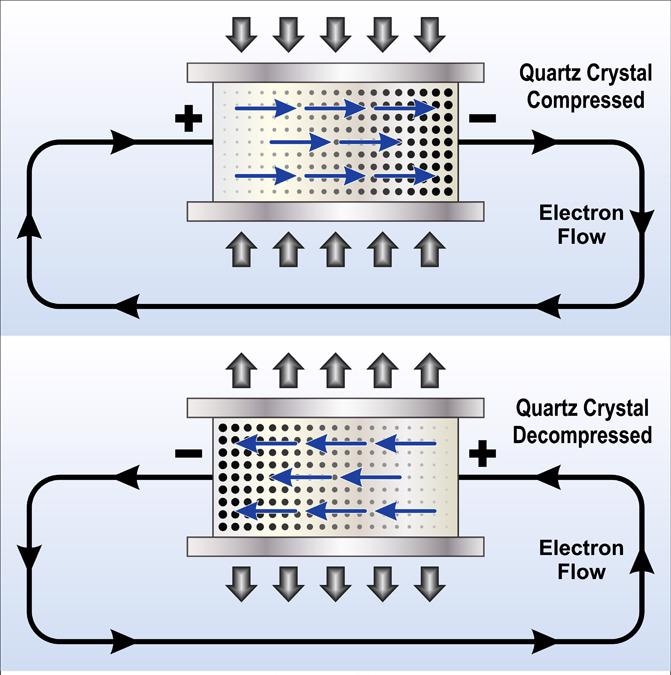
Study: High-performance piezoelectric composite fabricated at ultra-low temperature.Image Credit: Fouad A. Saad/Shutterstock.com
What are Piezoelectric Materials?
Piezoelectric materials accumulate electric charge in response to applied mechanical stress and vice versa. These are used in electromechanical transducers such as sensors, actuators, and acoustic imaging devices. They can be specific ceramics, polymers, or a composite of both.
Piezoelectric ceramic materials show higher performance than piezoelectric polymers, but piezo-polymers have their advantages including light weight, thinness, high flexibility, and low cost.
Lead zirconate titanate (PZT, PbZrxTi1-xO3) is one of the best piezo-ceramic materials with high electromechanical performances and good manufacturability, but it is synthesized using a power-sintering method at a very high temperature over 1000◦C.
This hampers direct utilization in monolithic devices and increases the emissions and production costs due to the high energy consumption. Also, it causes unwanted diffusion and evaporation of volatile elements from the compound during manufacturing.
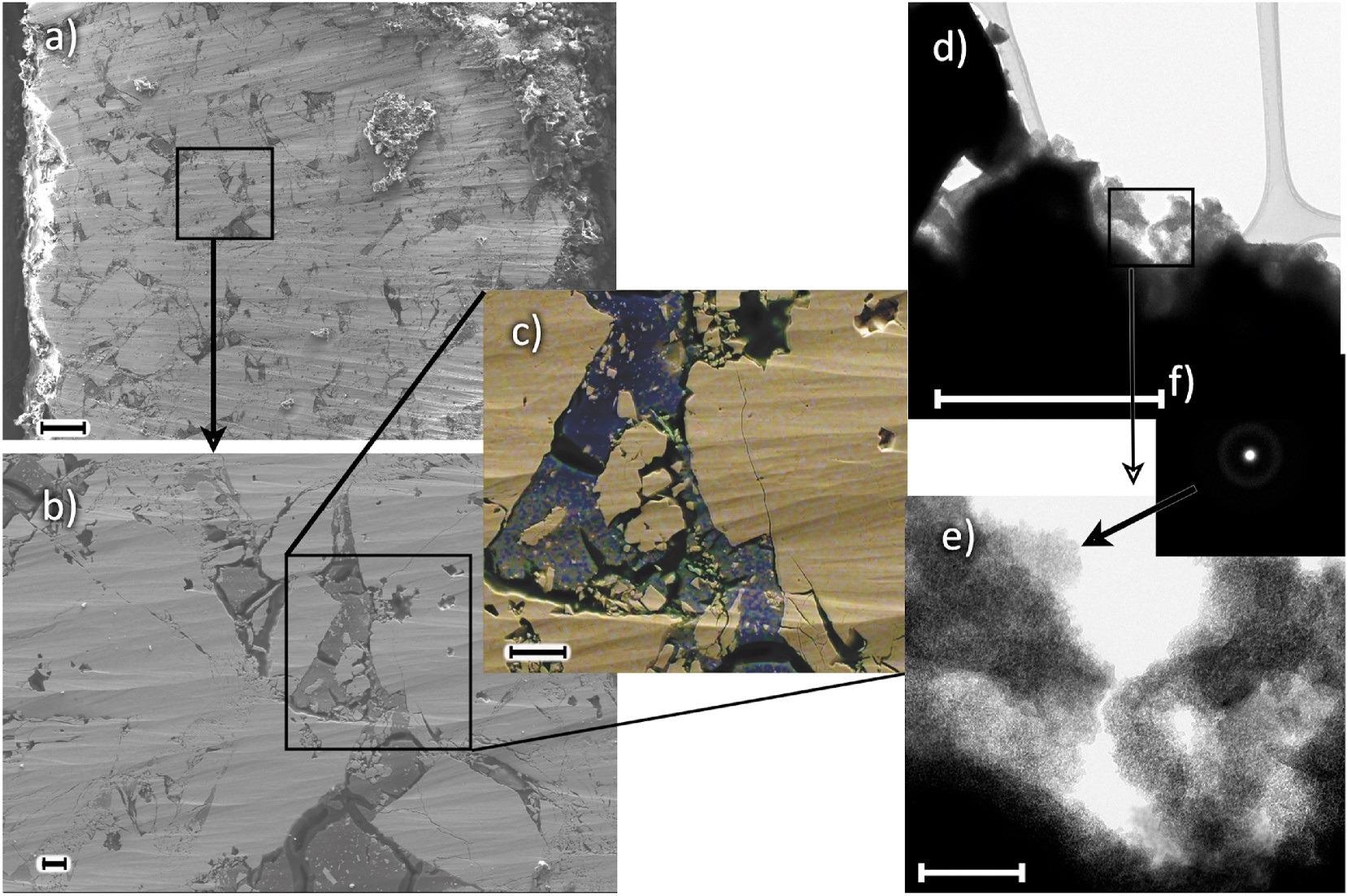
a) – c) Cross-section of composite sample fabricated at 350 ◦C. Squares show the close-up areas. Close packing of PZT particles can be observed, as well as darker TiO2 phase in between the particles. Colored EDS elemental map in c) shows the multimodal PZT particles as the location of lead in PZT is shown as brownish color and TiO2 phase as blue color. Figures d) and e) show the TiO2 phase on the surface of PZT particles ground off from the sample cross-section, seen as partly transparent material. Figure f) shows the diffraction image with no indication of crystallinity. The arrow shows the analyzed spot. Scale bars: a) 100 μm, b) and c) 10 μm, d) 1 μm, e) 100 nm. Image Credit: T. Siponkoski et al., Composites Part B: Engineering.
As a solution to this, alternative approaches such as the use of sintering aid glasses, particle size reduction, and the development of piezo-polymers or piezo-polymer and piezo-ceramic composites have been incorporated.
Although the ceramic-polymer composites enable very low manufacturing temperatures, the electromechanical performance and temperature stability have been compromised to that of powder-sintered piezo-ceramics.
Recently, a water-soluble ceramic binder Li2MoO4 (LMO) is used to enhance the temperature resistance and the electrical properties with carefully selected particle size distribution and compatible filler materials.
This approach incorporated a higher filler to matrix ratio, hence the composite is called an “upside-down composite”. However, the water-solubility of LMO compels these composites to add another layer of protection when used in high humidity conditions.
What is Soft Solution Processing?
In soft solution processing (SSP), gel-like precursors are used to fabricate piezoelectric thin films at very low temperatures.
However, the maximum thickness of these films is limited due to the large shrinkage of the solution during the crystallization stage. The same happens in upside-down composites; the binder material forms a very thin layer between the particles.
Hence, both SSP can be used for the fabrication of thin upside-down composite films. Moreover, in upside-down composites, the shrinkage of the precursor solution can be compensated due to the simultaneous application of pressure while heating.
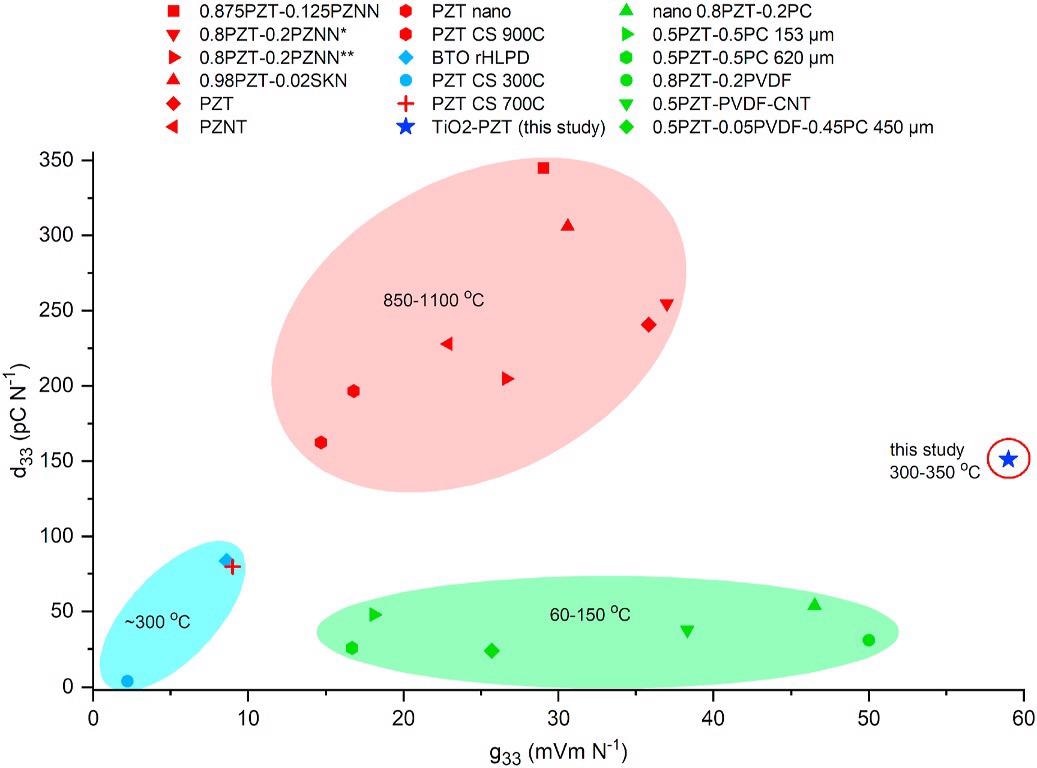
Piezoelectric charge and voltage coefficients of materials fabricated at various temperatures. Red area: bulk ceramics sintered with sintering aids, green area: Portland cement and polymer bound composites, blue area & star: ultra low temperature fabricated all-ceramic materials. *amount of CuO 0.3 wt %, **amount of CuO 0.5 wt%, nano = PZT nanoparticles.Image Credit: T. Siponkoski et al., Composites Part B: Engineering.
How was the Piezo-ceramic Composite Fabricated?
The researchers combined both upside-down and soft solution processes to synthesize the piezo-ceramic. PZT with suitable particle size distribution was combined with titanium dioxide using an organotitanate precursor and simultaneously applying pressure and temperature.
The fabrication was based on two major performance-enhancing approaches. One is the multimodal particle size distribution of the filler that enhanced the packing ratio. The other one is the utilization of a gel-like binder that forms ceramic material through a reaction when heat and pressure are applied. This compensates for the shrinkage of the precursor by transforming the organometal precursor into titanium oxide.
The TiOx –precursor gel was synthesized by heating the mixture of titanium-di-isopropoxide-2-acetoacetate with 2-methoxy ethanol and ethanolamine. Then the precursor gel was mixed with lead-zirconate powder followed by pressing at 250 MPa at room temperature and heating to 200–350 ◦C at constant pressure. The theoretical density was 4–5% less than that of LMO-bound upside-down composites.
How was the Performance of the Fabricated Piezo-Composite?
Dielectric properties such as the relative permittivity and the dielectric loss tangent were measured at room temperature at frequencies from 100 Hz to 1 MHz with an LCR meter.
The relative permittivity increased with increasing fabrication temperature up to 300 ◦C and then saturated close to the level of 280. The permittivity was about 27% higher than lithium molybdate-PZ29 (LMO-PZT) piezoelectric upside-down composite, while the losses remained the same.
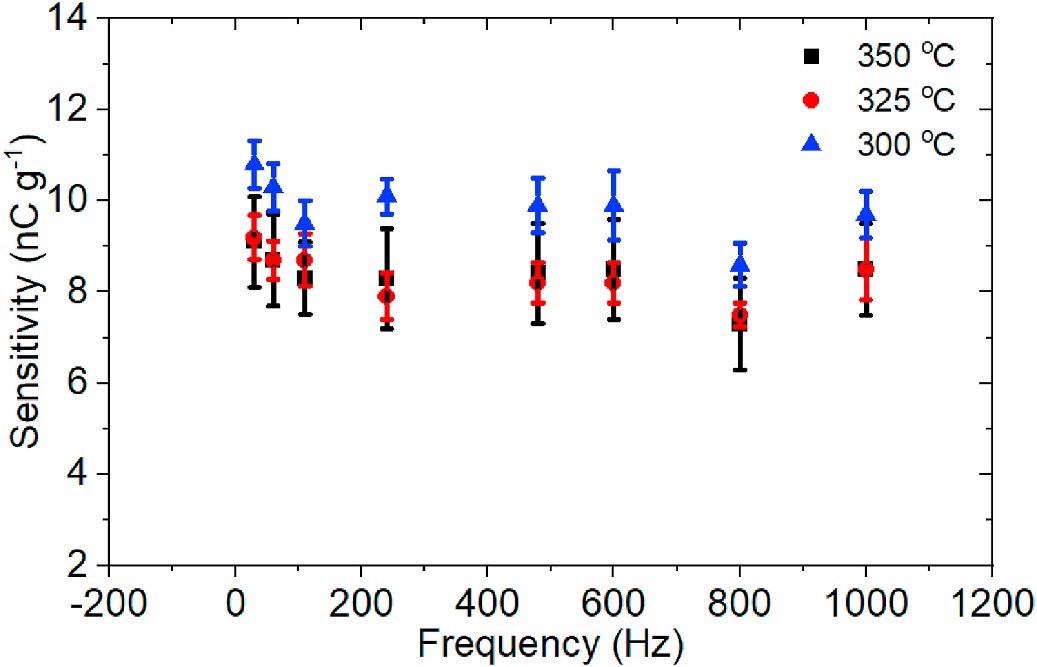
Sensitivity of the charge mode accelerometers in frequency range 30–1000 Hz. Image Credit: T. Siponkoski et al., Composites Part B: Engineering.
The piezoelectric coefficient d33 was measured using direct and converse piezoelectric effects using a d33 meter. The measured piezoelectric coefficients d33 and g33 were about 80% and 70% higher, respectively than those reported for upside-down composite with the same filler ceramic, but with LMO as a binder. It was found to be the consequence of enhanced coupling of the electric field in the titanium oxide-bound composite.
Additionally, the achieved piezoelectric coefficients d33 and g33 corresponded to about 26% and 157% of the lead-zirconate values, respectively, which were one of the highest among ultra-low temperature fabricated piezo-ceramics. The study found that the fabricated composite is ideal for water-resistance sensor applications due to its high and almost frequency-independent sensitivity.
Reference
T. Siponkoski, M. Nelo, N. Ilonen, J. Juuti, H. Jantunen, High-performance piezoelectric composite fabricated at ultra-low temperature. Composites Part B: Engineering. 2021;229:109486. https://www.sciencedirect.com/science/article/pii/S1359836821008532?via%3Dihub
Disclaimer: The views expressed here are those of the author expressed in their private capacity and do not necessarily represent the views of AZoM.com Limited T/A AZoNetwork the owner and operator of this website. This disclaimer forms part of the Terms and conditions of use of this website.