A paper published in Additive Manufacturing has demonstrated how embedding mica platelets into polyetherketoneketone, a popular thermoplastic that has utility for sectors including the automotive industry, can improve its properties.
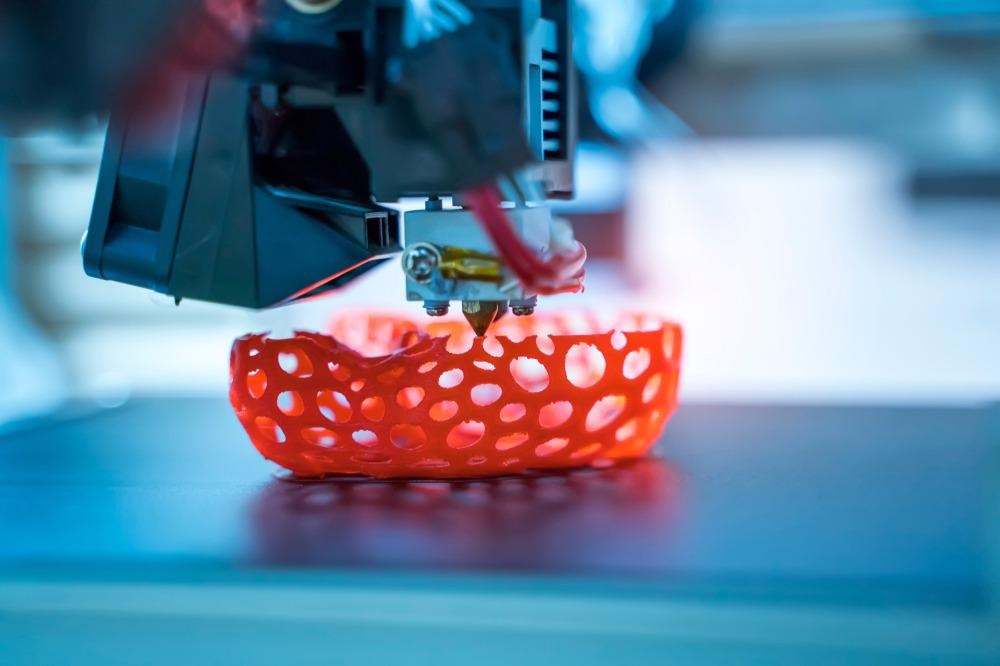
Study: Mica filled polyetherketoneketones for material extrusion 3D printing. Image Credit: asharkyu/Shutterstock.com
Extrusion-based 3D printing has become a vital technology for several key industrial and research fields over recent years. Improving the properties of materials such as thermoplastics is central to many research studies.
PAEKs
Polyaryletherketones (PAEKs) are a class of thermoplastics that are used increasingly in the automotive, aerospace, and medical industries due to their tolerance to high temperature, resistance to chemicals, strength, lightweight properties, and high glass transition temperatures. Additionally, due to their wear and fatigue properties, they are used to replace metal in various applications. PAEKs are semi-crystalline, with high performance.
In the past decade, this class of thermoplastics has received significant attention in additive manufacturing as feedstocks. Recent developments such as the reduced cost of 3D printing equipment that can handle high temperatures and with finely tuned printing conditions and the availability of commercial feedstocks have facilitated their applications in the field.
Polyetheretherketone (PEEK) has been the most utilized feedstock in additive manufacturing in recent years. These applications include laser sintering, fused deposition modeling, and fused filament fabrication. Additionally, there has been use of PEEK in room temperature direct ink writing methods using binder chemicals.
Polyetherketoneketone (PEKK) has emerged as a promising PAEK for use as an additive manufacturing feedstock. The development of FFF-specific feedstocks has expanded the use of PEKK. Moreover, PEKK has advantageous properties compared to PEEK as a feedstock. These include the presence of rigid ketone groups in the polymer’s backbone that increase its glass transition temperature and a nearly 30 oC lower processing window and melting temperature that decreases the thermal demands and processing difficulties in printers.
Additionally, PEKKs have a relatively lower rate of crystallization. This facilitates the formation and maintenance of crystals at lower temperatures which are more favorable to rheological properties such as complex viscosity. Furthermore, PEKK can be tuned by controlling the ketones in the polymer backbone. Another attractive property of PEKK is its low coefficient of thermal expansion, which reduces the instances of warping in materials.
Challenges with PEKKs
Despite their attractive properties, there are still some challenges that hinder the widespread adoption of PEKKs as feedstocks for additive manufacturing methods. These challenges facilitate the need for further research and innovation. One challenge that must be addressed is the high levels of shrinkage which are associated with crystallization events. This shrinkage can severely impact the performance of printed materials, including issues with warping, interlayer adhesion, delamination, and defects.
Improving the print quality and properties of polymers such as PEKK can be achieved by optimizing process parameters and improving printing equipment. However, the upper bound of performance is limited by the intrinsic polymer properties.
More from AZoM: Promoting the Breakdown of Plastic with Nickel Catalysts and CO
Some of the intrinsic FFF printing challenges can be circumvented by using composite materials and favorable properties can be augmented to produce more viable end-products. The use of fillers helps to reduce warping and improve mechanical properties and thermal conductivity. Additionally, thermal expansion can be reduced by using fillers. Different fillers have been explored in recent studies such as glass fibers and composites have been produced that include nanomaterials and high-performance polymers.
Using Mica Fillers to Improve the Properties of PEKKs
The new study published online in Additive Materials has explored the use of mica fillers in PEKKs to improve their properties for additive manufacturing applications. Micas are sheet-like phyllosilicate materials that possess favorable electrical and mechanical properties, chemical resistance, and relatively high aspect ratios. Additionally, they are low-cost, abundant, and safe when embedded into matrixes. This makes them attractive fillers for additive manufacturing.
Composite polymers using mica fillers have properties that are determined by the size of the mica flakes, polymer matrix crystallinity, volume fraction, physical interaction with the polymer matrix, and other factors. Although mica fillers have attractive properties, the authors have stated that there is almost no literature on their integration into high-temperature thermoplastics such as PEKK for additive manufacturing.
In the study, the authors compared the performance of FFF processed PEKK which included conventional compatibilizer molecule treated mica fillers with metal oxide-coated mica fillers. The team hypothesized that mica fillers would enhance the PEKK’s mechanical strength if suitably compatible and improve dimensional stability via crystallization. Additionally, the team state that the materials would not have an adverse effect on the chemical reactivity of PEKK and undermine properties such as stability in extreme environments.
The study demonstrated that PEKK with mica fillers have several enhanced properties such as higher stiffness when printed and that thin metal oxide layer-coated pigment-based micas reduce the melting temperature of PEKK materials without significantly changing the glass transition temperature. Other favorable properties were observed, which facilitate further research into these composite materials which will aid the commercial uptake of mica-filled PEKK composites for additive manufacturing.
Based on the observations in the study, the team has stated that micas and other similar fillers may have broad application for inclusion in PAEKs and other high-performance thermoplastics in the future.
Further Reading
Kennedy, Z.C et al. (2022) Mica filled polyetherketoneketones for material extrusion 3D printing [online] Additive Manufacturing 49 | sciencedirect.com. Available at: https://www.sciencedirect.com/science/article/abs/pii/S2214860421006400
Disclaimer: The views expressed here are those of the author expressed in their private capacity and do not necessarily represent the views of AZoM.com Limited T/A AZoNetwork the owner and operator of this website. This disclaimer forms part of the Terms and conditions of use of this website.