The production of solid oxide cells is a complex, challenging process. Recently, additive manufacturing (AM) otherwise known as 3D printing, has emerged as an advantageous production method. A pre-proof journal in Additive Manufacturing has explored the production of solid oxide cells using robocasting and inkjet printing.
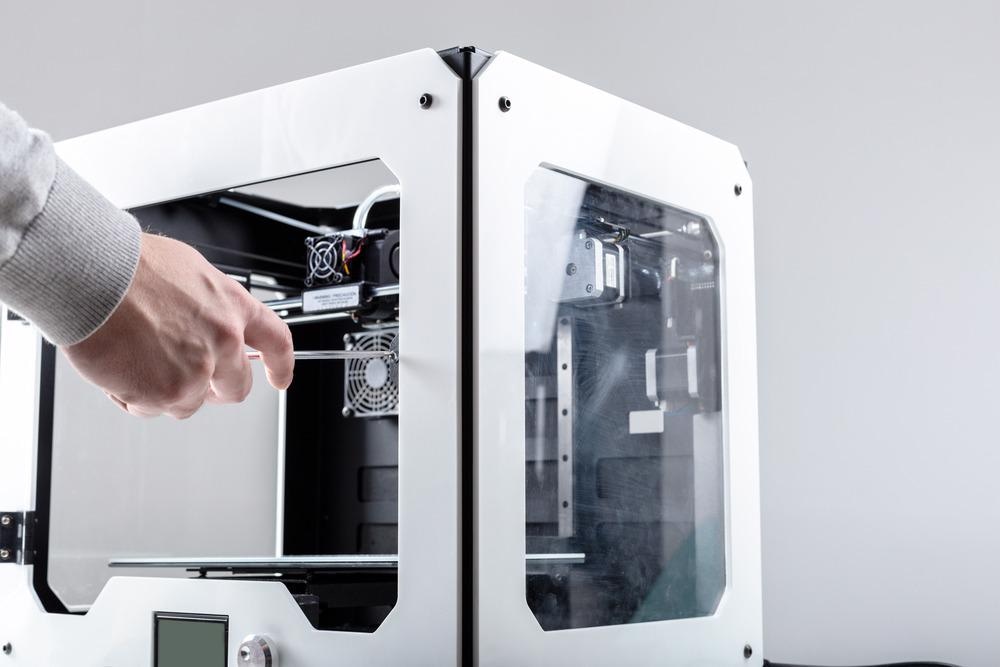
Study: Hybrid-3D printing of symmetric solid oxide cells by inkjet printing and robocasting. Image Credit: FabrikaSimf/Shutterstock.com
Solid Oxide Cells
Ceramic devices have been explored recently for use as supercapacitors, environmental and energy technologies, separation membranes, all-solid-state batteries, chemical sensors, and solid oxide cells. Solid oxide cells are multi-layer ceramic devices that can be utilized as efficient solid oxide electrolysis cells for hydrogen production or as fuel cells which can be used to generate energy using hydrogen as a fuel source.
Solid oxide cells consist of dense electrolytes usually based on yttria-stabilized zirconia (YZM). Mixed ionic-electronic conducting membranes are deposited on either side of the zirconia layer. Yttria stabilized zirconia is an ionic conductor which has high stability under elevated temperatures, which ensures the required gas tightness of the electrodes.
Composite electrodes using perovskite and pure ionic conductors have been explored as mixed-ionic-conducting membranes.
Fabrication Methods
Solid oxide cells are traditionally manufactured by combining standard ceramic fabrication methods such as screen printing and tape casting. In the past, fully dense electrolytes were obtained by at low temperatures by using sintering aids. Porous electrode layers were obtained by using pore formers in the formulation of printing inks.
Whilst these methods can produce large numbers of cell units, challenges such as materials waste and size and geometrical limitations exist. Additionally, they can be complex, multi-step fabrication processes.
Additive manufacturing, which includes methods such as direct ink writing, inkjet printing, fuse deposition modeling, stereolithography, and robocasting, has been proposed as an alternative fabrication process for these complex, multi-material device components.
Traditionally, ceramic additive manufacturing methods have employed feedstocks which contain ceramic materials dispersed in organic solvents. This requires debinding and sintering steps to remove the organic feedstock components and optimize the printed ceramic pieces. Optimizing the thermal treatment process is crucial. Fabrication of 3D multi-material ceramic devices is a cornerstone of many innovative technologies.
Robocasting: A Useful Fabrication Method
Additive manufacturing provides many advantages for the manufacturing of solid oxide cells, including reducing waste, reducing processing steps, limiting their environmental impact, and overcoming geometrical constraints.
Robocasting is a potentially advantageous fabrication method for ceramic materials and devices. Analogous to direct ink printing and other extrusion-based techniques, a filament-like material (usually a ceramic slurry) is extruded from a nozzle as it is moved across a platform according to a 3D CAD model.
Further Reading: How Can AI Overcome 3D Printing Defects?
The CAD model is divided into different layers which are printed in a liquid state and then immediately solidify, based on the rheological property of shear thinning. The printed parts retain their shape without the need for solidification or drying.
Whilst robocasting has been explored in recent years as a 3D printing method, there is little literature on using it specifically for the deposition and fabrication of solid oxide cell electrodes.
The Study
The study in Additive Manufacturing (currently in pre-proof) has presented a novel hybrid fabrication method for printing multi-material solid oxide cells using robocasting and inkjet printing. The method combines porous electrodes printed using robocasting with thin dense electrolytes which are deposited using inkjet printing. The hybrid printing process was followed by a co-sintering step.
LSM-YSZ, a ceramic composite, was used for the electrodes, with YSZ used for the electrolytes. LSM is a perovskite material. Inkjet printing was chosen for its ability to produce extremely thin layers of electrolyte due to its superior control when depositing small amounts of materials. The printed cells have the structure LSM-YSZ/YSZ/LSM-YSZ. The study characterized the microstructure and electrochemical performance of the printed cells. SEM-EDX, EIS, and XRD were used for this characterization.
Printability and rheological characterizations were performed on both the robocast slurries and the water-based YSZ inks for inkjet printing. Silicon oxide fuel cells were produced with free-standing robocast electrodes and inkjet-printed electrolytes in a single step. The feasibility of the process and its reproducibility were confirmed by microstructural analysis, and electrochemical characterization demonstrated performance comparable to state-of-the-art results for similar composite materials.
The results of the study demonstrated the potential of the hybrid robocasting/inkjet printing process for the fabrication of functional multi-material solid oxide fuel cells which can be used as next-generation energy devices.
Further Reading
S. Anelli et al. (2022) Hybrid-3D printing of symmetric solid oxide cells by inkjet printing and robocasting [online] Additive Manufacturing | sciencedirect.com. Available at:https://www.sciencedirect.com/science/article/pii/S2214860422000422
Disclaimer: The views expressed here are those of the author expressed in their private capacity and do not necessarily represent the views of AZoM.com Limited T/A AZoNetwork the owner and operator of this website. This disclaimer forms part of the Terms and conditions of use of this website.