By Surbhi JainReviewed by Susha Cheriyedath, M.Sc.Apr 18 2022
In a review recently published in the journal Bioprinting, researchers presented an extrusion-based bioprinting platform made of biodegradable polyester.
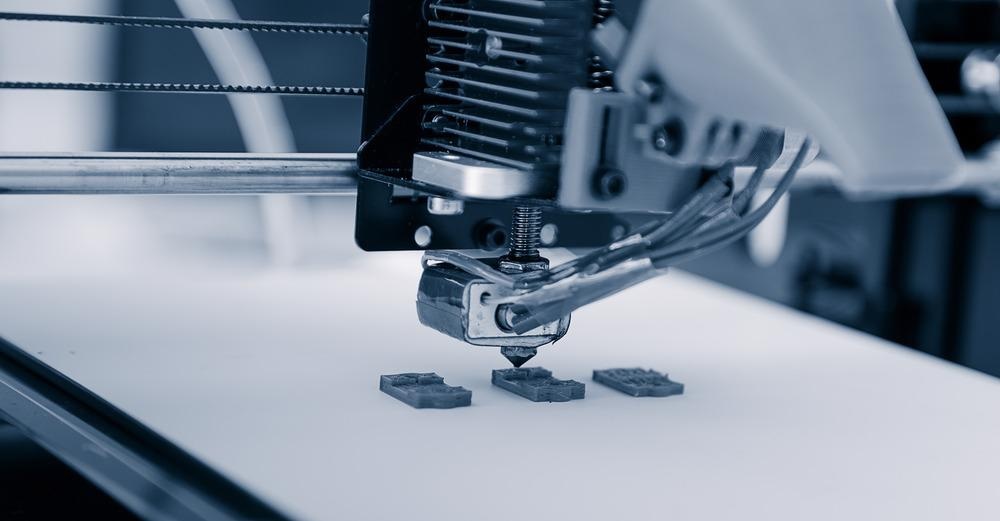
Study: Biodegradable polyester platform for extrusion-based bioprinting. Image Credit: nortivision/Shutterstock.com
Background
In recent years, 3D bioprinting has emerged as a cutting-edge additive manufacturing technology that allows for the processing of widely known (bio)polymers into scaffolds for the development of functional biological structures. Due to its compatibility with numerous cell types and (bio)materials, cost-effectiveness, and the ability to generate both viscous hydrogels and thermoplastic polymers containing suspended cells, extrusion-based bioprinting is one of the most frequently explored methods.
Most extrusion-based bioprinters now have two or more print heads, allowing them to print multiple (bio)materials to create a single item. Artificial tissue structures with enhanced mechanical properties can be created with multi-material and/or coaxial bioprinting for a wide range of bio-applications.
Poly(lactide-co-glycolide), poly(ε-caprolactone), and polylactide are the most popular biocompatible polyesters used for 3D extrusion-based printing due to their appealing biocompatibility and mechanical properties, printability into complex architectures, and tolerance to hydrolytic degradation to form non-toxic products. To sustain cell viability and meet mechanical criteria for 3D complex tissue/organ fabrication, proper selection of (bio)polymeric materials is critical. Furthermore, the use of smart (bio)polymers transforms 3D bioprinting into 4D processing since the resulting scaffolds alter size, shape, and/or functionality when subjected to changes in pH, temperature, ionic strength, or other stimuli.
About the Study
In this study, the authors presented a review focused on using the most appealing aliphatic polyesters in the domains of 3D and 4D bioprinting of bioartificial tissue and organs. An overview of the most relevant synthetic polyesters for fabricating anatomically structured constructions using 3D extrusion-based bioprinting, which had been widely explored for tissue replacement and regeneration was provided. The 3D bioprinting process was also depicted in detail. The current state of the art in the 3D bioprinting of cartilage, nerve, bone, and liver tissues was also examined.
More from AZoM: An Overview of Post Irradiation Examination (PIE) Techniques
The researchers discussed the use of 3D extrusion-based bioprinting to create sophisticated biomimetic structures for the reconstitution of live tissues. The production of functional 3D constructs with both bioactivity (bio-ink) and defined design and shape was reviewed. The potential of aliphatic (co)polyesters as the materials of choice for fabricating biocompatible and biodegradable 3D scaffolds was illustrated. Recent research related to the polyester frame's function that could be stretched from current mechanical support to a composite matrix with smart stimuli-responsive behavior was revealed.
Observations
The presence of hydroxyapatite nanoparticles in the poly(lactide) (PLA) matrix was found to affect shape memory capabilities when an additional fixed phase in the PLA composite was created. 4D-printed porous scaffolds made of PLA with 15wt.% hydroxyapatite filler had shape memory and induced active cell proliferation, which made them promising candidates for self-fitting bone implants. Copolyesters with soft segments were produced by copolymerizing lactide with trimethylene carbonate at a transition temperature of about 37°C. At 40°C, the copolyester matrix weakened, which allowed the scaffold to be easily deformed and inserted into the syringe. After the injection into the Petri dish, the scaffold returned to its original shape after 30 seconds of higher temperature.
Tg for amorphous PLA was 55–60°C, while Tg for semi-crystalline PLA was 60–80°C. The highest printing temperature for poly(L-lactide) (PLLA) was 220°C. Young's moduli of up to 57.3 MPa and yield stress of 1.22–1.15 MPa were achieved in 3D porous bone constructions. They produced lysozyme protein that was active for up to 9 days after incubation.
Conclusions
In conclusion, this study elucidated that 3D bioprinting has enormous potential in the biomedical profession as a whole. It was also discovered that it has endless possibilities from medicine formulations to organ printing.
The authors believe that 3D bioprinting opens up new possibilities for the manufacture and design of multifunctional scaffolds that can transport bioactive compounds in situ. They determined that custom-made co-polyesters and their blends enabled shape modification in 3D-bioprinted scaffolds and were the most frequent technique to integrate the fourth dimension into 3D bioprinting.
They could be used to make modern biodegradable stents (e.g., esophageal, ureteral, or neonatal stents) that can be inserted noninvasively into the body using a needle (catheter).
The team also mentioned that current research on 4D bioprinting of polyester composites with stimuli-responsive polymers is still in the proof-of-concept stage, and 4D-bioprinted implants are often designed to respond to only one stimulus. They emphasized that to precisely design and create multifunctional biomimetic constructions that reversibly change their shape according to the stimulus in situ, a combination of many domains, including material engineering, mathematical modeling, biology, and medicine, should be implied. They believe that because 3D bioprinting is still in its infancy, it is predicted to revolutionize biomedicine in the same manner that 3D printing revolutionized manufacturing and engineering.
Disclaimer: The views expressed here are those of the author expressed in their private capacity and do not necessarily represent the views of AZoM.com Limited T/A AZoNetwork the owner and operator of this website. This disclaimer forms part of the Terms and conditions of use of this website.
Source:
Gliozzi, V., Pozzato, G. L., Valese, A., Biodegradable polyester platform for extrusion-based bioprinting. Bioprinting 26 e00198 (2022). https://www.sciencedirect.com/science/article/pii/S2405886622000082