By Surbhi JainReviewed by Susha Cheriyedath, M.Sc.Jun 1 2022
In an article recently published in the journal Additive Manufacturing Letters, researchers discussed the utility of laser sintering and stereolithography (SLA) in a multi-process additive manufacturing (AM) system.
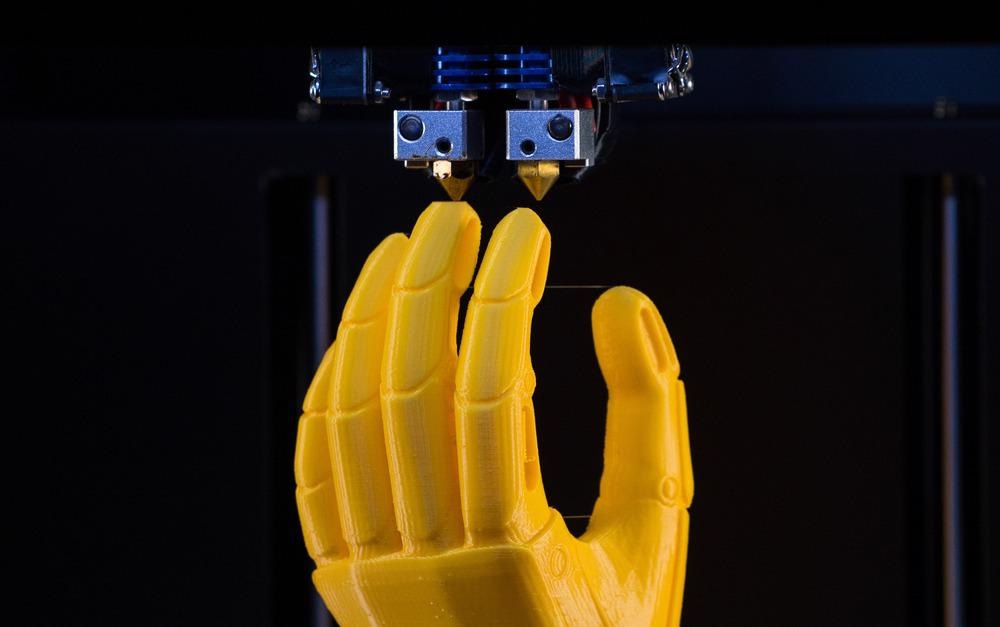
Study: Multi-Process Printing Combining Powder and Resin Based Additive Manufacturing. Image Credit: stockddvideo/Shutterstock.com
Background
AM is a broad term that encompasses a variety of processes and materials. Laser-based powder bed fusion, or selective laser sintering (SLS), and resin printing or stereolithography (SLA) are two of the most versatile AM methods. Users have traditionally been required to choose a single AM machine that produces a specific part using a single printing process with a single type of material, and then make alterations to the printed product using a second material through the post-processing technique. Depending on the adjusting method employed, this could be imprecise or time-consuming.
Inverted laser sintering (ILS) is a technique for layer-by-layer fusing powdered materials to a substrate. Using SLA resins in addition to SLS powders enables the printing of high-strength parts with smooth surface finishes while also expanding the range of materials that can be used in a single object. Previous work in this area has involved printing the SLS core component first, then moving the part to a separate stereolithography machine for the addition of an outer resin surface.
Overview of the proposed multi-process AM. a) Release agent coated glass and powder material layer captured by the release agent b) Substrate is pressed onto the upper surface of the powder and the laser fuses a selected region of powder to the substrate c) The substrate is raised with the fused powder d) The substrate is moved to a separate slide which has a film on the upper surface which has been coated with resin e) The substrate presses the sintered powder down into the resin and the laser is run again, towards the center of the glass it can be seen that the powder region has displaced some resin on the film f) The resin can either be fused as a secondary layer on top of the powder or in the same layer around the powder. Image Credit: Whitehead, J et al., Additive Manufacturing Letters
About the Study
In this study, the authors presented a new AM approach that blended powder-based and resin-based printing. Both resin-based and powder-based technologies had distinct advantages, ranging from powder process strength and material variety to resin printing resolution and surface polish. A unique powder-based printing technology that sent a laser beam upwards to fuse powders through the glass to a substrate was created.
However, in the same print, this arrangement was utilized to solidify resin as secondary material. The proposed hybrid technique was illustrated by the generation of samples comprised of both resins and powders.
The team looked into the possibility of using resin to reduce powder bed fusion part porosity and fine-tune part surface finish. A method was devised for the printing of both SLA resins and SLS powders in the same component. This was accomplished by moving a substrate between glass slides covered with different resins and powders and selective fusion of the sections of each material onto the same component. The researchers performed.
The researchers demonstrated that the proposed method required no additional transport mechanism, and because it was fully hybridized, it could be able to print not just exterior but also within SLA zones. The proposed multi-material technique was used for the printing of samples including both powdered thermoplastic polyurethane (TPU) and resin. The capability of resin to minimize the porosity of SLS components was investigated.
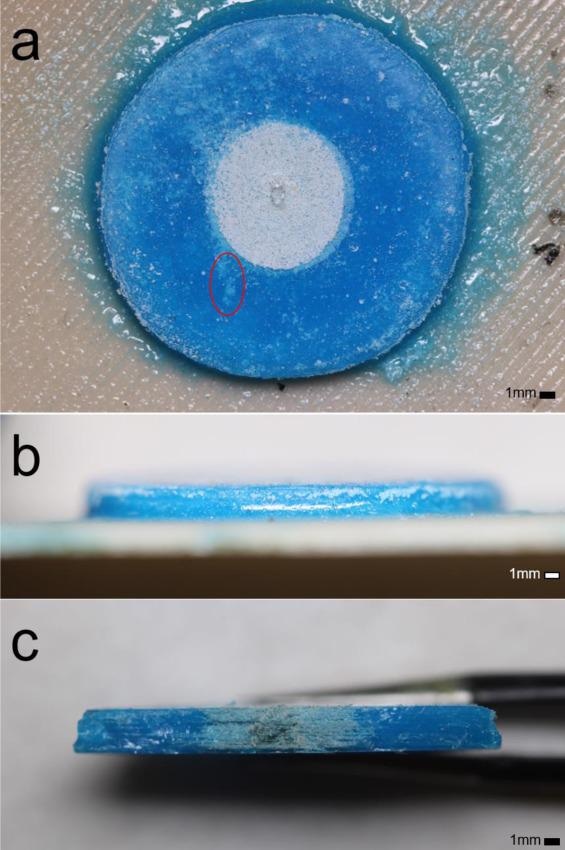
Close up of result. a) Upper view of the powder, resin nested cylinder. b) Profile view of the nested cylinders c) Sliced sample profile view. Image Credit: Whitehead, J et al., Additive Manufacturing Letters
Observations
The average sample thickness was discovered to be about 2.86mm, which corresponded to an average layer height of 95.3 µm. This thickness was well within the draught resin's resolution range. This height was also within the SLS layer boundaries, which normally ranged from 20 to 150 µm. Overexposure of the material to the laser caused the somewhat darkening sections near the center of the TPU in both the top and sliced profile views.
Using SLA resins and the SLS powders enabled the printing of highly strengthened parts with smooth surface finishes and expanded the range of materials that could be used in a single object. In addition to surface polish, this broader material selection allowed prints to have a larger range of attributes, such as variable strength, variable conductivity across the part, and variable thermal resistance.
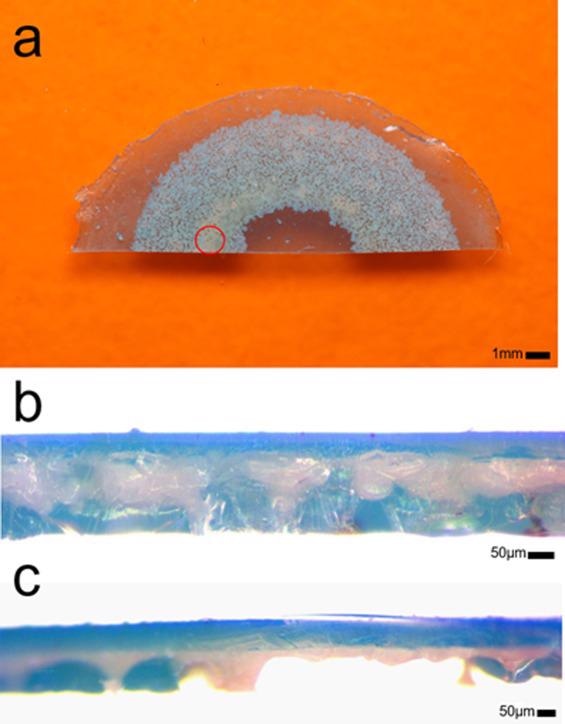
Coating SLS parts using SLA. a) Upper view of a resin-coated powder layer sample b) Profile view of a sliced sample showing resin permeation c) Print region without resin permeation. Image Credit: Whitehead, J et al., Additive Manufacturing Letters
Conclusions
In conclusion, this study proved that an inverted laser setup can print both SLS powders and SLA resins in the same test sample. It was also shown that doing so has a direct impact on porosity. This significantly expanded the range of materials that can be used in a single print.
The authors mentioned that more material options provide designers and engineers more control over what attributes they want in their prints and where they want them, such as surface gloss, modifying strength, and porosity. This has consequences in a variety of industries, including medicinal research, aerospace, and higher education. They also stated that while there is a risk of cross-contamination at present time, future production of an automated setup should considerably reduce this risk.
The team believes that incorporating metal particles rather than plastic would also allow users to print conductive pathways directly inside an insulating medium, resulting in 3D printed circuit boards. They mentioned that their next step will be to completely develop an inverted printer capable of autonomously producing components including both powder and resins.
Disclaimer: The views expressed here are those of the author expressed in their private capacity and do not necessarily represent the views of AZoM.com Limited T/A AZoNetwork the owner and operator of this website. This disclaimer forms part of the Terms and conditions of use of this website.
Source:
Whitehead, J., Lipson, H., Multi-Process Printing Combining Powder and Resin Based Additive Manufacturing. Additive Manufacturing Letters 100062 (2022). https://www.sciencedirect.com/science/article/pii/S2772369022000366