By Surbhi JainReviewed by Susha Cheriyedath, M.Sc.Jun 7 2022
In a review recently published in the journal Additive Manufacturing, researchers discussed the solidification methodologies for ink formulation in additive manufacturing.
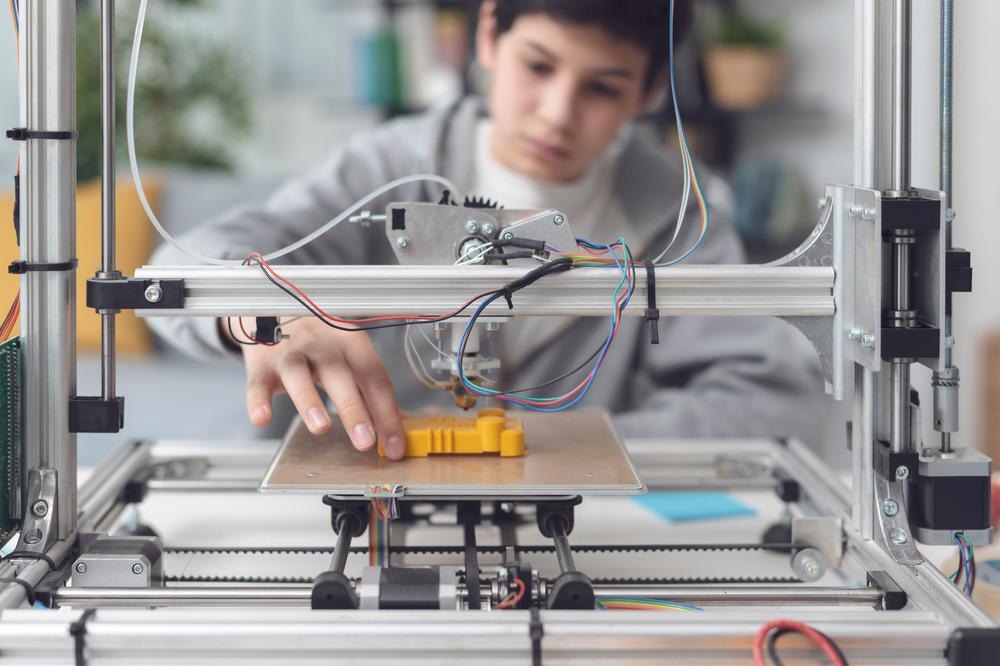
Study: Additive Manufacturing Solidification Methodologies for Ink Formulation. Image Credit: Stokkete/Shutterstock.com
Background
Since the 1980s, additive manufacturing, often known as 3D printing, has attracted much public interest with recent developments in gear, materials, and software making it accessible to a wide range of study fields and enterprises. The advent of benchtop 3D printers and low-cost desktops has accelerated innovation and reinvented manufacturing in a variety of fields. Typical photopolymerization-based printers, such as vat polymerization and materials extrusion which includes direct ink writing (DIW) and fused deposition modeling (FDM), are examples of such 3D printers.
The study of the viscoelastic characteristics of thermoset inks in the ink preparation/formulation process is critical in sustaining the printed architecture after the deposition until solidification or crosslinking occurs. The advancement and development of the 3D printed materials, as well as their wide range of applications, have been amazing.
Several extensive evaluations on process requirements, material design, and performance improvement strategies, particularly for DIW technology, have been published. Despite comprehensive reviews, studies detailing and examining fundamental yet important formulation techniques and solidification mechanisms for 3D printing – in particular, DIW technology – are lacking.
About the Study
In this study, the authors assessed the existing 3D printing technologies that could be used in practice. This review article gathered and reviewed the various ink formulas utilized in 3D printing-related journal papers, as well as their solidification techniques.
The team reviewed the advances, benefits, and drawbacks of three key solidification processes for 3D printing. A suggested outlook was also provided to shed light on the necessity of selecting appropriate approaches and to serve as a guideline for matching materials and application libraries.
The researchers provided a general understanding of the benefits and drawbacks of each solidification process so that they could make informed decisions during the DIW formulation stage. Further, the future of 3D printing and the field of formulations were reviewed briefly. A search of peer-reviewed journals from databases such as Scopus, PubMed, Web of Science, and ScienceDirect was utilized to ensure a comprehensive assessment of extrusion-based 3D printing studies.
Observations
Several studies reported green component strength as a big challenge in 3D printing ink formulas. The solidification stage in the 3D printing of viscoelastic materials had an impact on the product's structure and functionality. Solvent-assisted drying was one of the most prevalent solidification methods. Solvent-based inks were flexible, inexpensive, and reasonably environmentally friendly, despite the fact that they frequently resulted in brittle green portions. In-situ curing technologies such as ultraviolet light assisted, heat-assisted, etc. were used to improve the structural integrity of viscoelastic inks and raised the yield strength of 3D printed structures.
Extrusion-based 3D printing technology could theoretically accommodate a number of green body solidification types. This could be further divided into three categories. The first one was the physical procedures based on solvent behavior, such as water attraction and solvent evaporation/sublimation, which were commonly used in hydrogel systems. The second one was ultraviolet (UV) light-assisted curing, and the third one was thermal-assisted curing.
According to many studies, 3D printing has become one of the most popular technologies in modern civilization, ushering in a new era of industry. Desalination plants and upcycling of material waste would be better equipped to lower operating costs with higher-performing parts with a better understanding and development of 3D-printed materials.
Material selection, structure need, solidification technique, and material performance were all key factors in achieving this goal. Aside from the solidification processes, structure and performance optimization were also essential considerations. Several research groups looked into the impacts of infill density, raster orientation, and printing speed on the green-part strength.
Conclusions
In conclusion, this study described the mechanisms for green part curing of 3D extrusion constructions. Solidification via physical processes, UV curing, and thermal-assisted procedures were among these mechanisms. A roadmap for evaluating 3D ink formulations was also offered, as well as the possibility of a novel 3D printing curing process. The authors mentioned that researchers could deliberately pick and customize their 3D printing formulation for a successful 3D print job by evaluating the functionality of the green part, materials selection, and application of the 3D printed structure.
They also advised that the appropriate 3D printing technique for device fabrication should be carefully selected. The team emphasized that researchers will be better equipped to select 3D printing processes efficiently from the huge array of materials and formulations accessible if they focus more on data-driven methods like machine learning, such as algorithms recently developed by Erps and colleagues. They believe that because ink formulation is such an important part of the DIW process, this study will help readers evaluate the various formulation processes in a methodical way.
Disclaimer: The views expressed here are those of the author expressed in their private capacity and do not necessarily represent the views of AZoM.com Limited T/A AZoNetwork the owner and operator of this website. This disclaimer forms part of the Terms and conditions of use of this website.
Source:
Xu, X., Yang, J., Jonhson, W., et al. Additive Manufacturing Solidification Methodologies for Ink Formulation. Additive Manufacturing 102939 (2022). https://www.sciencedirect.com/science/article/abs/pii/S2214860422003359