The goals of scaffolding for bones and cartilage-related damage therapies include tissue repair, proliferation, and cell adhesion. The most recent study published in the journal Bioprinting intends to examine solid freeform additive manufacturing methods based on slurry ejection for the construction of bioactive glass and associated composite scaffolds, as well as their controlled design and permeability.
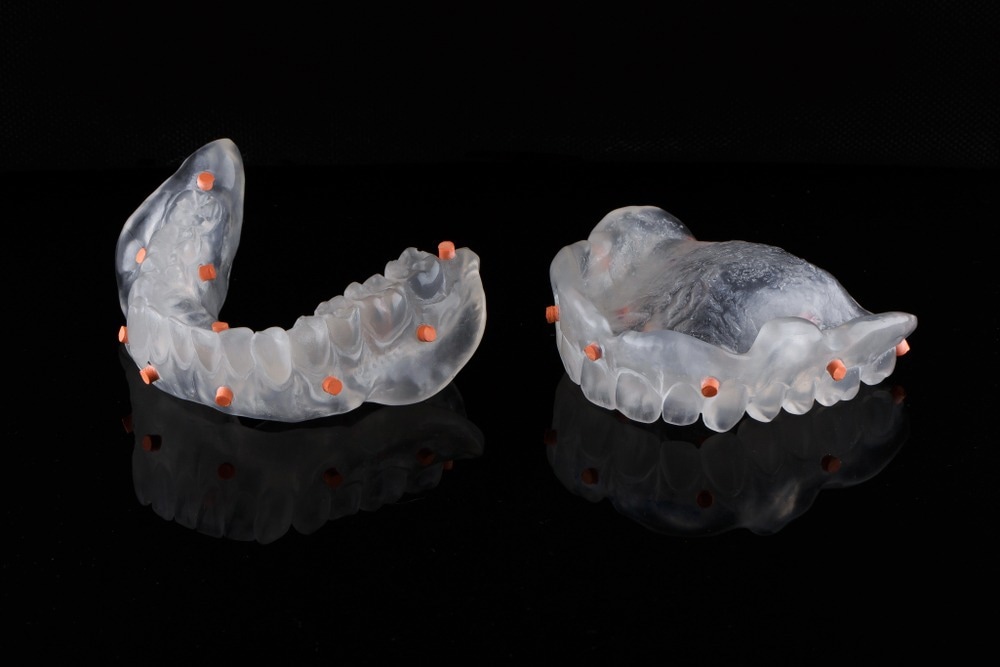
Study: Extrusion-based 3D printing of bioactive glass scaffolds-process parameters and mechanical properties: A review. Image Credit: Dental Pro Content/Shutterstock.com
Fabrication Techniques for 3D Porous Structures
The motivation for constructing three-dimensional porous structures came from the complicated functioning requirements in tissue engineering, construction, computing, energy production, and so on. Porous structures have traditionally been synthesized using procedures such as gas foaming, particle leaching, and solvent casting.
However, some difficulties arose often throughout procedures. The downsides of these older techniques were interconnection, a lack of effective control over porosity, poor repeatability, and the necessity for specialized tools and molds, leading to unpredictable mechanical qualities. The goal of creating freeform manufacturing processes is to minimize or reduce these limitations.
Freeform Fabrication Techniques
Using colloidal inks, freeform manufacturing methods construct a constituent layer by layer. The deposition is done according to a design provided by a computing device, like hot melt printing, robotic-assisted casting or robocasting, and straightforward inkjet printing.
Which Freeform Fabrication Technique is Extensively Utilized?
Robocasting is one such method that has grown in popularity in recent years. It is an additive manufacturing process focused on extrusion. A three-dimensional layer-by-layer structure is highly automated and formed as a thick sludge at room temperature. The system produced with ceramic inks is consolidated by robocasting through fluid gel transformation.
What is Bioactive Glass?
Bioactive glassware is bioceramics that are hard, non-porous, and strong, with silicon dioxide as the major component. Bioactive glassware is a unique collection of glass components that react with bodily fluids to generate the same material that our bones are formed of.
Preparation Methods of Bioactive Glass
For the production of bioactive glass, numerous approaches are widely employed. The classic technique of cooling molten fluid at its liquid temperature to make glass is quenching or fast cooling. In an electrically powered furnace, a platinum furnace calculates individual compounds in oxides or carbonates at 600 °C - 800 °C.
The sol-gel process is a popular alternative to the melt-quenching approach. The chemical precursors undergo hydrolysis and condensation processes at room temperature to generate a gel in the sol-gel method's chemistry-based synthesis pathway.
Micro-Emulsion and Laser Spinning Process
The micro-emulsion technique is comprised of two non-miscible liquids that are maintained by translucent surfactant molecules, resulting in an isotropic and entropically stable distribution.
In laser spinning, a small volume of parent substance is rapidly heated, melted with a high-power laser, and chilled with a supersonic gas stream. Because heating is controlled by rapid cooling, the final result of this process is an amorphous state.
Other Methods for Bioactive Glass Formation
Solvent casting is the method of joining polymer and bioactive ceramic materials in an organic liquid and pouring the solution into a readymade 3D mold to prepare composite scaffolds. The solution is released by heating and evaporation once it has been cast.
Flame spray synthesis has been used to manufacture megatons of silicon and titanium-based nanoparticles every year since 1940. High-temperature ranges yield nano-sized particles. It is also employed in the production of bioactive glasses in a variety of sectors.
Production of Scaffolds Based on Slurry Extrusion
Traditional techniques for fabricating 3D scaffolds include gel casting, solvent casting, slip casting, polymeric foam reproduction, and freeze casting. Over older procedures, solid freeform fabrication (SFF) techniques may accurately manage the scaffold design through CAD.
During fabrication, a paste is typically extruded onto a construction table through a nozzle. In particular, slurry in the form of a paste is put in a cartridge and extruded utilizing air pressure from the nozzle tip. Scaffolds are produced by layer-by-layer deposition by moving in the x- and y- directions utilizing computer program controls.
Future Perspective
Combining 3D printed bio-ceramics with hydrogels allows for the use of a wide range of materials to create clinically bio-functional bone replacements. Features less than 100 m in length and scaffolds with extensive internal elements are still difficult to build due to fabrication time or cracking propensity in post-processing phases. Understanding correlative structure-property relationships are critical for developing and ensuring the mechanical dependability of AM-fabricated scaffolds.
More from AZoM: Reviewing the Use of Computational NIR Spectroscopy
Further Reading
Palivela, B.C. et al. (2022). Extrusion-based 3D printing of bioactive glass scaffolds-process parameters and mechanical properties: A review. Bioprinting. Available at: https://www.sciencedirect.com/science/article/pii/S240588662200029X?via%3Dihub
Disclaimer: The views expressed here are those of the author expressed in their private capacity and do not necessarily represent the views of AZoM.com Limited T/A AZoNetwork the owner and operator of this website. This disclaimer forms part of the Terms and conditions of use of this website.