A paper recently published in the journal Additive Manufacturing demonstrated the feasibility of using a new three-dimensional (3D) printing algorithm to print parts with filaments oriented according to the input orientation field at different infills.
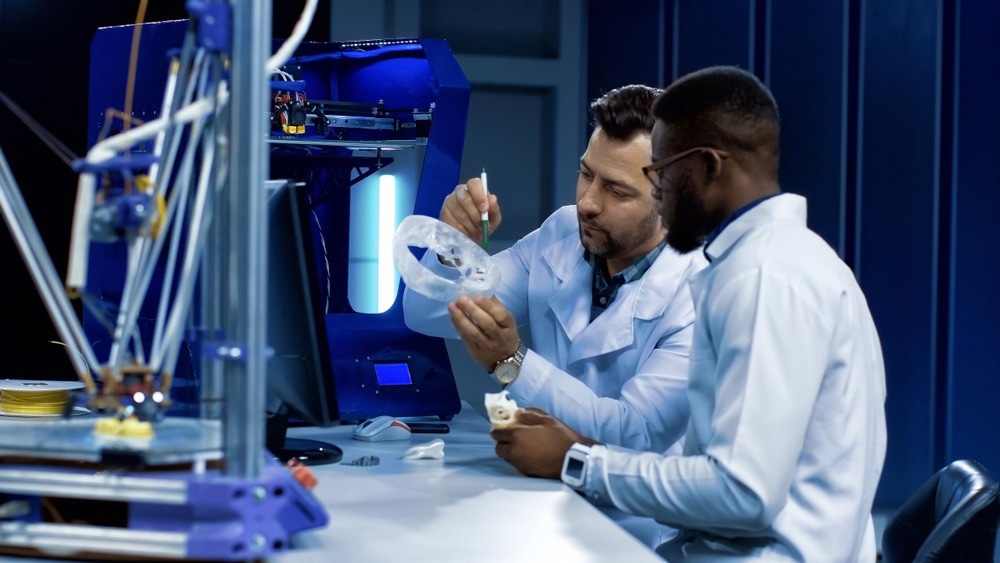
Study: An orientation-field based algorithm for free-form material extrusion. Image Credit: Frame Stock Footage/Shutterstock.com
Background
Additive manufacturing (AM)/3D printing technologies based on the material extrusion principle, such as fused filament fabrication (FFF), are used extensively in several industries. The FFF working principle involves heating and extruding a thermoplastic filament along a fixed path and then stacking it in a layer-wise manner to fabricate a part.
Although FFF is a suitable AM technique to fabricate highly complex designs as it offers unprecedented design freedom, the method is not preferred for the manufacturing of functional components.
The slicing software used during AM fabricates parts with the desired surface density and quality by precisely controlling different printing parameters, such as infill percentage, extrusion width, layer height, flow rate, and printing speed. However, the software does not allow the maximum design freedom required in FFF-like AM techniques.
Thus, limited improvements were made to exploit the ability of FFF to freely deposit filaments. FFF induces a mechanical anisotropy in the fabricated component due to the in-plane orientation of deployed filaments. Thus, adjustments in the filament orientations can yield a superior structural performance by tailoring the mechanical properties in several directions.
However, the slicing software can only offer the layers of predefined filament patterns by slicing the computer-aided design (CAD) model and does not consider any orientation information potentially available resulting from a topology optimization process or recovered from imaging data obtained from magnetic resonance or computed tomography.
Until now, such situations were addressed using approximated techniques. However, these processes were cumbersome, time-consuming, and not entirely effective. A limited number of studies have exploited the mechanical anisotropy in FFF printed parts through customized filament placement.
For instance, a stress line AM (SLAM) method was proposed in a study in which the principal stress directions were utilized to generate curvilinear filament paths. Similarly, volumetric deposition path generation (VDPG) that depends on the streamline placement algorithms was proposed for deposition path generation from an arbitrary orientation field.
The Study
In this study, researchers developed a new algorithm that can freely deposit filaments along any orientation field by fully exploiting the potential of the FFF technology. The proposed algorithm can factor in most of the design requirements and process constraints typically considered in the commercial slicing software and provide a ready-to-use geometric code (G-code) as output.
A set of two-dimensional (2D) positions indicating the geometrical bounds of the part slated for printing, an orientation field that informs the orientation of the material in the infill domain at a discrete set of points, and a 2D position set used as seed points were used in this proposed algorithm in place of an input CAD model.
Additionally, the algorithm also considered other parameters relevant for designing the dimensions and trajectories of the filament, including the retraction length, filament diameter, nozzle printing speed, nozzle travel speed, number of layers, the minimum spacing between filaments (gp), layer height, and extrusion width (w).
MATLAB R2019b was used to develop the entire algorithmic framework composed of three major steps, including streamline generation, density control, path linking, and G-code generation.
Three structural problems, designated as case A, case B, and case C, were presented to validate the proposed algorithm. All problems were represented by their corresponding geometries. Case A was represented by an open-hole plate subjected to tensile load, case B by bending of the plate, and case C by a five-holed plate subjected to tensile load.
The algorithm inputs were obtained through the finite element analysis (FEA) of the structural problems. Ansys, a commercial software, was used to perform the FEA. A 3ntr A4v3 machine based on modified MK4duo firmware was employed for 3D printing of the geometries.
The machine consisted of a heating chamber and a 295 x 295 x 200 mm build volume. Additionally, the extruders in this printer can attain a maximum temperature of 390 oC, while the build plate can attain up to 120 oC temperature.
Observations
Initially, the capability of the algorithm to produce various infills was evaluated. The maximum infill percentage was approximately 90% in all cases for -0.05 mm gp. Additionally, the proposed algorithm required 51 min, 18 min, and 30 min to fetch the trajectory solutions of Case C, B, and A, respectively, while the time required to print the corresponding geometries of Case C, B, and A was 107 min, 66 min, and 58 min, respectively.
However, the filaments changed their direction at every point and were prone to develop intra-layer voids as they were following an orientation field. These voids could not be filled entirely using constant width filaments, leading to a reduction in the area coverage for the printed part.
Moreover, the algorithm consumed several minutes for filament trajectory computation in contrast to the instant results delivered by slicing software. Thus, more research is required to improve the computational efficiency of the algorithm through parallelization techniques.
The proposed algorithm allowed complete freedom in tailoring the properties of FFF printed parts based on the desired mechanical performance. Researchers experimentally verified the inter-filament spacing conditions set for the partial- and maximum-filled parts.
Initially, the filament centerline distances for the maximum-filled open-hole plate with -0.05 mm gp and 0.5 mm w were measured. The centerline distances between three filament pairs in a densely filled region were measured as 0.46 mm, 0.48 mm, and 0.45 mm. All measured centerline distances were equal to or greater than w + gp/0.45 mm.
Thus, the distances adhered to the spacing condition imposed in the density control step. Similar results were also obtained for the partially-filed part with a multi-oriented stacking sequence, where the measured values of centerline distances were larger than w + gp.
The effect of seed points on efficiency and area coverage was determined as the number of seed points dispersed throughout the infill domain plays a critical role during the filament trajectory computation. A rising number of seed points increased the number of generated streamlines, which increased the computational effort at the density control section. A rise in computational effort increased the overall computational time.
Although the area coverage expanded initially with the rising number of seed points, it later converged for all three cases as a fixed number of filaments can only be placed in the infill domain for every value of w and gp. Thus, increasing the seed point number was ineffective and adversely affected the computational efficiency once the area coverage was converged for every case.
Conclusion
To summarize, the findings of this study demonstrated that the proposed algorithm can deposit filaments accurately by controlling the filament orientation in line with the input orientation field. Streamlines were generated from seed points distributed throughout the design domain.
A separate density control step was used to eliminate the streamlines that violated the spacing constraint and select the continuous streamlines as filament trajectories. Although the approach was computationally expensive, it reduced the discontinuities and offered better control over design solutions.
The algorithm facilitated the printing of efficiently designed anisotropic structures. Filaments can be directly printed with orientations mandated by the design solutions, which is specifically beneficial for printing fiber-reinforced variable-stiffness (VS) composites through the continuous filament fabrication (CFF) process.
Additionally, the algorithm can be used to produce efficient and customized lattice-type structures and to print toys, art, food, and other consumer products where traditional printing strategies are ineffective.
More from AZoM: How Can Polymer Strips Be Used to Clean Up Oil Spills?
Disclaimer: The views expressed here are those of the author expressed in their private capacity and do not necessarily represent the views of AZoM.com Limited T/A AZoNetwork the owner and operator of this website. This disclaimer forms part of the Terms and conditions of use of this website.
Source:
Murugan, V., Marconi, S., Auricchio, F. et al. (2022) An orientation-field based algorithm for free-form material extrusion. Additive Manufacturing. https://doi.org/10.1016/j.addma.2022.103064