
Induction coil design can have a huge impact on process efficiency, part quality, and cost of manufacturing. Below are five ways to optimize your design and some induction coil basics.
How Induction Heating Coils Work
How efficiently and effectively a workpiece is heated is determined by the induction coil. Induction coils are water-cooled copper conductors created from copper tubing which is readily formed into the shape of the coil for the induction heating process. As water flows through them, induction heating coils themselves do not get hot.
Work coils range in complexity from a coil that is precision machined from solid copper and brazed, to a simple solenoid- or helical-wound coil (made up of a number of turns of copper tube wound around a mandrel).
By producing an alternating electromagnetic field due to the alternating current flowing in them, coils transfer energy from the power supply to the workpiece. The coil’s alternating electromagnetic field (EMF) creates an induced current (eddy current) in the workpiece, which generates heats due to I Squared R losses (core losses).
The coil’s EMF strength correlates with the current in the workpiece. This transfer of energy is known as the eddy current effect or transformer effect.
Transformers and Induction Coils
As coils utilize the transformer effect, properties of transformers can help understand coil design. The inductor is similar to a transformer primary, and the workpiece is equivalent to the transformer secondary (assumed to be a single turn).
There are two key features of transformers which affect coil design:
- (Current in the primary of the transformer * # of primary turns) = (current in the secondary * # of secondary turns)
- Efficiency of coupling between the windings is inversely proportional to the square of the distance between them
As a result of the relationships outlined above, there are five conditions that must be considered when designing any coil for induction heating:
1. The Geometric Center of the Coil is a Weak Flux Path
Closer to the coil turns themselves, flux is the most concentrated. It declines with distance from the turns. If a part was located off center in a coil, the area closer to the coil turns would intersect a larger amount of flux lines and so be heated at an increased rate.
The section of the part away from the copper coil encounters less coupling and would be heated at a lower rate. In high-frequency induction heating this effect is more pronounced.
2. The Coil Should be Designed to Avoid Cancellation of the Magnetic Field
The coil does not have sufficient inductance needed for efficient heating if opposite sides of the inductor are too close. This effect can be offset by inserting a loop in the coil at the center. Then the coil will heat a conducting material inserted in the opening.
3. The Magnetic Center of the Inductor is not Necessarily the Geometric Center
The magnetic field is weaker at the place where the coil and the leads join. This effect is most noticeable in single-turn coils. This condition becomes less important as the amount of coil turns grows and the flux from each turn is added to that from the previous turns.
The part should be offset slightly toward this area in static heating applications due to the impracticality of constantly centering the part in the work coil. The part should be rotated to enable uniform exposure if possible.
4. Higher Flux Density Near the Heating Area Leads to a Higher Current Being Generated in the Part
The coil should be coupled as near to the part as possible, so the largest viable amount of magnetic flux lines intersect the workpiece at the heating point in order to permit maximum energy transfer.
5. The Largest Number of Flux Lines in a Solenoid Coil are Near the Center of the Coil
The flux lines are concentrated inside the coil, allowing the optimum heating rate at that location.
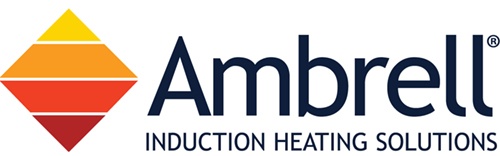
This information has been sourced, reviewed and adapted from materials provided by Ambrell Induction Heating Solutions.
For more information on this source, please visit Ambrell Induction Heating Solutions.