Cross-sections milled by Ga FIB are typically on the several tens of microns, width, and depth. However, for structures such as displays, TSVs, MEMS, BGAs, or flip-chips, which may require extra-large cross-sections for failure analysis, a plasma ion column is the preferred solution for milling. TESCAN SOLARIS X FIB-SEM equipped with iFIB+™ Xe plasma FIB column delivers the high currents needed to speed material removal for large cross-sections.
Unfortunately, surfaces milled by Xe plasma FIB may cause undesirable curtaining artefacts on the cross-section, similar to Ga FIB at very high beam currents, when a composite material is processed. One method for improving surface quality is polishing the material from different directions, although this makes the cross-sectioning process more difficult, more time consuming and less accurate. To overcome these drawbacks, TESCAN SOLARIS X offers a novel method that greatly improves surface quality, while maintaining simplicity and accuracy throughout the milling process: the Rocking Stage. The Rocking Stage allows users to take advantage of SOLARIS X’s wide field of view and SEM imaging for monitoring the milling process and accurate endpointing.
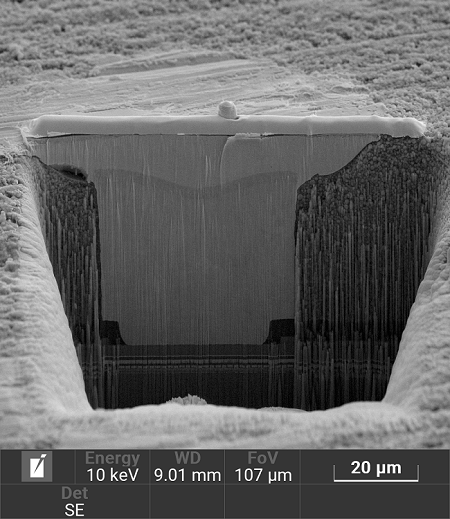
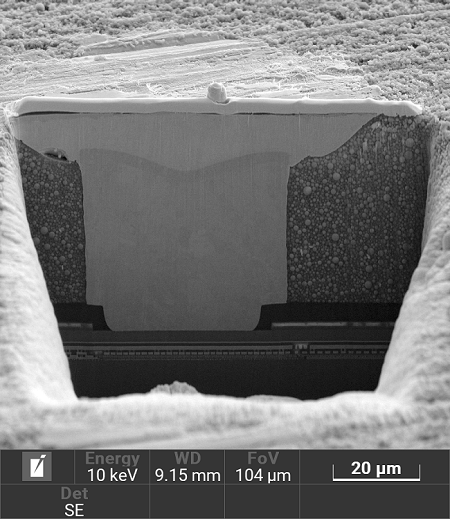
Fig 1. Top: 100 um wide Plasma FIB cross-section through solder bump and copper µVIA. The interface is partially covered by curtaining artifacts making it difficult for failure analysis. FIB milling time 50 minutes.
Bottom: The cross-section after an additional 10 minutes of Rocking polishing. The details at the bump and µVIA interface can be clearly recognized and investigated!
Eucentric sample stages allow tilting only around the axis perpendicular to both the FIB and SEM columns. The main problem to this approach is the inability to perform SEM imaging during the FIB milling process, in the case that the sample requires milling from different directions to reduce the curtaining effect. Without the ability to implement SEM imaging during the polishing process, polishing becomes time consuming, challenging and less accurate. It requires pausing the polishing process and then changing the stage position to check the cross-section quality from time to time. It is difficult to stop milling when the desired point/structure is reached and also minimize the curtaining artifacts. TESCAN’s novel Rocking Stage adds tilting in the plane of the cross-section. This method (Fig. 1) allows monitoring the entire milling and tilting process with SEM imaging, which is essential for precise end-point detection.
Want to know more? Click here to read the full article.
TESCAN Group
Founded in 1991 by a group of managers and engineers from Tesla with its electron microscopy history starting in the 1950’s, today TESCAN is a globally renowned supplier of Focused Ion Beam workstations, Scanning Electron Microscopes and Optical Microscopes. TESCAN’s innovative solutions and collaborative nature with its customers have won it a leading position in the world of nano- and microtechnology. The company is proud to participate in premier research projects with prominent institutions across a range of scientific fields. TESCAN provides its clients with leading-class products in terms of value, quality and reliability. TESCAN Group is the North American arm of TESCAN Group, a multinational company established by the merger of Czech company TESCAN, a leading global supplier of SEMs and Focused Ion Beam workstations, and the French company ORSAY PHYSICS, a world leader in customized Focused Ion Beam and Electron Beam technology.

This information has been sourced, reviewed and adapted from materials provided by TESCAN Group.
For more information on this source, please visit TESCAN Group.