Ceramic matrix composites are lightweight alternatives to metal alloys with superior physical and thermal properties. Hence, they are promising candidates for high-temperature applications, including use in internal engine components. This article looks into the applications of ceramic matrix composites in high-temperature gas turbine engines.
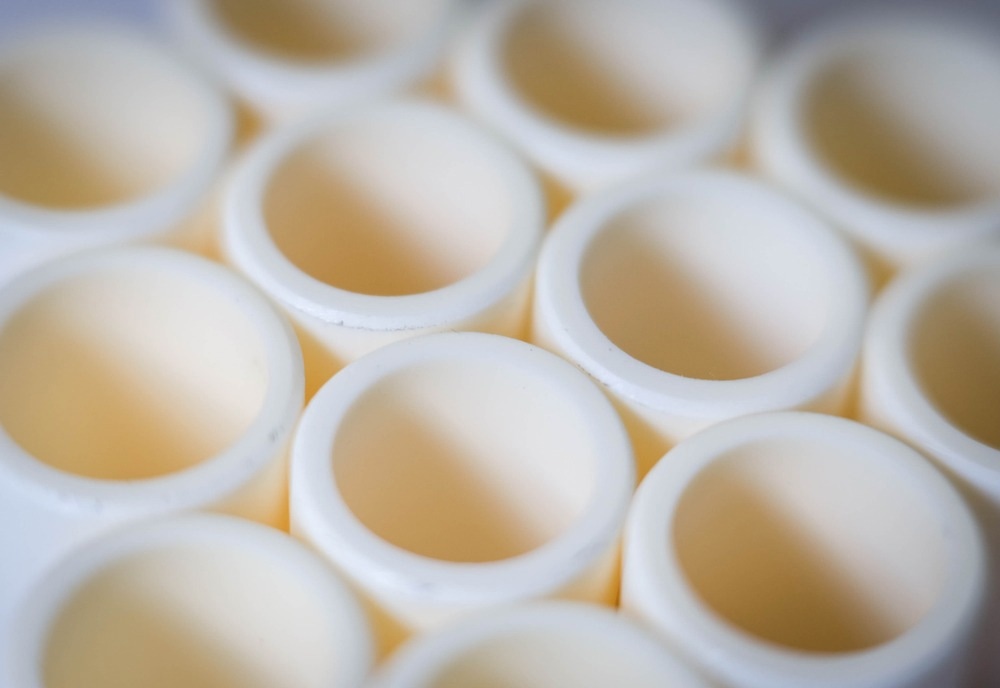
Image Credit: WildSnap/Shutterstock.com
What are Ceramic Matrix Composites?
Composite materials typically consist of two components: a reinforcement part to provide mechanical strength and a matrix material that holds all the components intact. In ceramic matrix composites, both components are composed of ceramics. In a few cases, the reinforcement and matrix materials are composed of the same type of ceramics, and additional secondary fibers may also be included.
Typical reinforcing fiber materials include carbon (C), silicon carbide (SiC), alumina (Al2O3), and alumina-silica (Al2O3-SiO2). Fibers exist in different forums, such as conventional continuous fibers, short fibers, whiskers, particles, and nanofibers. Similar to conventional ceramics, these fibers have a polycrystalline structure.
The thickness of the reinforcing fibers is as small as that of human hair and is even smaller in the case of nanofibers. These fibers are woven into fabrics and integrated into ceramic matrix composites. Although the matrix material used in ceramic matrix composites is the same as fiber materials, they are sometimes integrated with non-oxide ultra-high-temperature (UHT) materials.
Compared to traditional ceramics and metal alloys, ceramic matrix composites are significantly different and offer remarkable properties for various applications, including high-temperature resistance, lightweight, greater fracture toughness, and thermal shock resistance.
The ability of ceramic matrix composites to retain high mechanical strength, even at very high temperatures, makes them promising candidates for material science applications. Ceramic matrix composites also exhibit excellent stiffness and stability. Unlike conventional ceramic materials, ceramic matrix composites are resistant to fracture and crack propagation due to the integration of reinforcing fibers.
What is a Gas Turbine Engine?
Gas turbines are internal combustion engines that extract chemical energy from fuels and convert it into mechanical energy. Air is often used as the working fluid. Recently, gas turbines have gained significant interest in the generation of electricity that can be used in chemical plants and refineries.
There are four major types of gas turbines, as mentioned below:
- Turbojet Engines: In this type of engine, air moves at high speed and fuels the inlet and ignition of the combustion chamber. The turbine expands the air and accelerates the gas exhaust. This type of gas turbine is used in military aircraft, commercial aviation, supersonic aircraft, and others.
- Turboprop Engines: This engine is connected to a propeller through a gear system. In this type, a turbojet spins a shaft linked to a transmission gearbox, which slows the spinning process and attaches the slowest-moving gear to the transmission mechanism. The air propeller generates thrust through the rotation. This type is used in regional and commuter aircraft aircraft, cargo, and military aircraft.
- Turbofan Engines: These are connected to the front of a turbojet engine with a duct fan that offers extra push and helps the engine cool, reducing the engine noise output. These are utilized in commercial aircraft, regional aircraft, cargo aircraft, and military aircraft, business jets.
- Turboshaft Engines: These turbojet motors have a large shaft connected to their backs. This type of engine uses the majority of the power to spin turbines. These engines are used in helicopters, unmanned aerial vehicles, marine applications, and agriculture aircraft.
Application of Ceramic Matrix Composites in Gas Turbine Engines
Continuous fiber-reinforced ceramic matrix composites reduce the susceptibility to damage and are hence used in gas turbine engines. Two classes of ceramic matrix composites are extremely useful for elevated temperature applications: oxide/oxide composites (oxide fiber oxide matrix composites) and SiC/SiC composites (silicon carbide fiber reinforced silicon carbide matrix composites).
Because of the low availability of high-temperature oxide fibers, low thermal conductivity, and high thermal expansion coefficient, oxide/oxide composites are limited to elevated-temperature applications of 1100 °C.
Moreover, the poor thermal shock resistance of oxide/oxide composites, which is a crucial requirement in the hot sections of gas turbines, limits their application. Consequently, SiC/SiC composites with tolerance to high temperatures and better thermal shock resistance are being widely utilized for high-temperature applications.
Recent Studies
A recent article published in the Journal of Engineering for Gas Turbines Power reported the fabrication of ceramic matrix composite vanes with shell and spar designs. These vanes were used in high-pressure turbines as inlet guide vanes at a constant rotor inlet temperature. Consequently, the ceramic matrix composite vanes offered emission and performance benefits, which were assessed using a reference engine.
Unlike metal inlet guide vanes, the redesign of vanes using ceramic matrix composites required less cooling, reduced fuel consumption by 0.23% during the cruise, and potentially by 0.41% with lower-pressure cooling air. Additionally, a decrease in nitrogen oxide emissions of over 4% was observed owing to the reduction in the turbine inlet temperature.
Another article published in the Journal of Turbomachinery reported the fabrication of ceramic matrix composite weaves by integrating film-cooling holes for three test coupons printed using additive manufacturing.
The first coupon had a weave topology along the surface of the internal channel supplying coolant to the film-cooling holes, the second coupon had a weave topology along the outer cooled surface, and the third coupon had a weave topology on the coolant supply channel, and the external film-cooled surface.
The study proved that the effectiveness of the weave surface on the external film-cooled wall was observed to be lower than that of a smooth external surface. Furthermore, this external weave increased the mixing of the coolant jet with the hot mainstream, resulting in poor cooling.
Conclusion
Overall, ceramic matrix composites have remarkable properties, such as resistance to high temperatures and lightweight, which make them ideal candidates for gas turbine engines. According to recent studies, ceramic matrix composites have been applied in critical engine components such as turbine vanes and combustion liners. They offer benefits including higher firing temperatures and reduced cooling requirements, thus enhancing the performance and efficiency of the engine.
The limitations of traditional materials, such as metal alloys, are substantially addressed by ceramic matrix composites, offering a promising solution to the demanding requirements of modern gas turbine technology.
More from AZoM: MC4: Improving the Circularity of Fiber-reinforced Composites in the EU
References and Further Reading
Gas Turbine Types: Overview of Types and Profitable Applications. (Accessed on 5 November 2023).
What Are Ceramic Matrix Composites? (Accessed on 5 November 2023).
What Are Ceramic-Matrix Composites & How Are They Used In Jet Engines? (Accessed on 5 November 2023).
Descamps, P., Tirlocq, J., & Cambier, F. (1991). Ceramic matrix composites: properties and applications. 3rd European Symposium on Engineering Ceramics. Pp. 109-125. https://link.springer.com/chapter/10.1007/978-94-011-7990-4_9
Wehrel, P., Schöffler, R., Grunwitz, C., Carvalho, F., Plohr, M., Häßy, J., & Petersen, A. (2023). Performance and Emissions Benefits of Cooled Ceramic Matrix Composite Vanes for High-Pressure Turbines. Journal of Engineering for Gas Turbines and Power, 145(12). https://doi.org/10.1115/1.4063534
Disclaimer: The views expressed here are those of the author expressed in their private capacity and do not necessarily represent the views of AZoM.com Limited T/A AZoNetwork the owner and operator of this website. This disclaimer forms part of the Terms and conditions of use of this website.