The process of alloying has been used by material engineers, particularly to impart useful specific properties to different materials. In the process of alloying, different materials in trace quantities are added to a main constituent substance to form a final product that has the desired properties intended for specific applications.
However, in recent years, a new type of superior alloy called the high-entropy alloy has been used in various industries. These alloys are manufactured using advanced metallurgical techniques, which will be reviewed in this article.
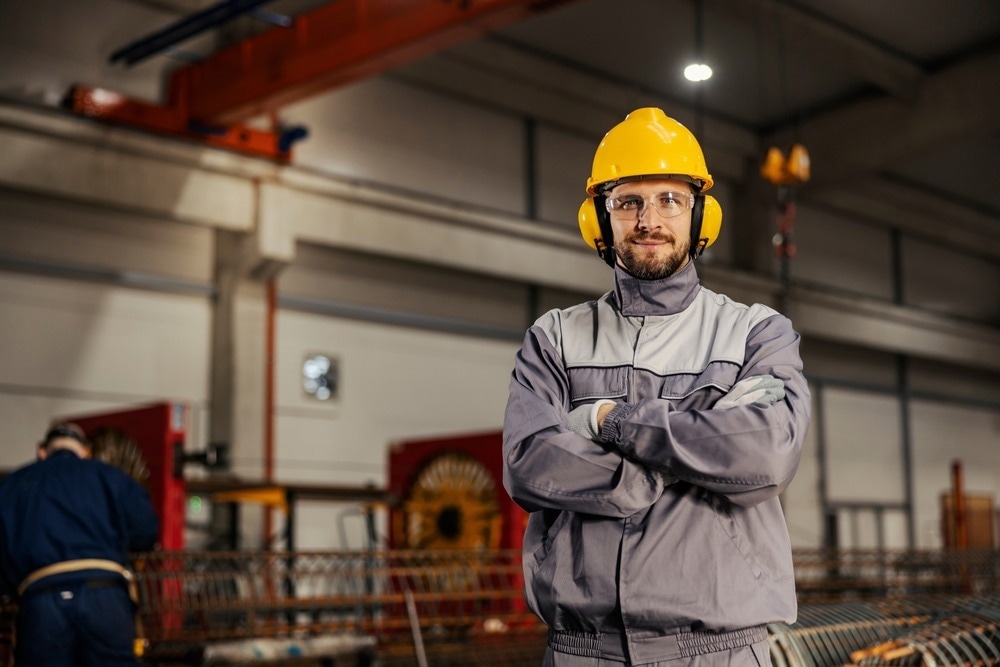
Image Credit: Dusan Petkovic/Shutterstock.com
A Brief Overview of High-Entropy Alloys
The basic technique of adding trace amounts of secondary elements to a basic primary element has been utilized by materials engineers for several decades. A research article published in Nature has presented an overview of high-entropy alloys.
As per the article, the novel approach for the production of high-entropy alloys involves combining several principal elements in relatively high concentrations, often in equi-atomic proportions.
This approach is unique from traditional practices and has gained significant attention. In the production of high-entropy alloys, incorporating five or more elements in near-equal-atomic proportions enhances the configurational entropy of mixing. This effect is adequate to counteract the enthalpies of compound formation, preventing the development of potentially harmful intermetallics.
For the class of high-entropy materials, five or more materials must be present in relatively high concentration (the concentration of these elements should be between 5 to 35%).
Initially, most high-entropy alloys (HEAs) explored were multi-phase alloys rather than single-phase solid solutions. However, in recent years, there has been a growing focus on a select few single-phase alloys to examine their behavior more thoroughly.
Studying single-phase alloys enables systematic variations in variables like the number, types, and concentrations of alloying elements. This direct correlation with physical and mechanical properties, such as elastic constants, bonding energies, diffusion coefficients, strength, and ductility, becomes possible.
Three Strategies for the Development of Advanced High-Entropy Alloys
High entropy alloys, whose initial concept was proposed in 2004, possess four distinct characteristics and core effects, including superior entropy values, slow rates of diffusion, higher lattice distortion, and complex multi-elemental interactions among the constituent substances called “cocktail effects”.
A research article published in Entropy reviews the three major strategies in the production of high-entropy alloys. Application-based redesign is likely the most commonly employed strategy among the three strategies. This approach focuses on designing high-entropy alloys (HEAs) tailored for specific applications. The major types of alloys produced by this method include refractory HEAs, lightweight HEAs, HE bulk metallic glass (HEBMG), and high-entropy superalloys.
The second major strategy is the second strategy involves altering the composition of a known conventional alloy by applying the high-entropy concept. This modification can be made to either the solvent or the solutes.
The crucial aspect is to substitute the current solvent or solute with additional elements. Modifying the solvent typically results in a new high-entropy alloy (HEA). Conversely, altering the solute yields a conventional alloy with increased entropy.
The third strategy is termed as “Incorporating Second Phases”. High-entropy alloys (HEAs) readily adopt simple phases, such as FCC (face-centered cubic) and BCC (body-centered cubic), offering distinct properties.
Nevertheless, the strength of HEAs with simple phases is typically constrained. Specifically, alloys with FCC structures tend to be relatively soft. Among prevalent strengthening mechanisms, second-phase strengthening proves to be the most effective. These second phases can be introduced directly in the cast state or precipitated within a matrix through heat treatment.
Additive Manufacturing of High-Entropy Alloys
In recent years, additive manufacturing (AM) technologies have garnered significant attention as an innovative approach for producing high entropy alloy (HEA) components. The exceptional mechanical and environmental properties of HEAs make them applicable in various demanding sectors, including the aerospace and automotive industries.
High entropy alloys (HEAs) can be conventionally manufactured through various methods, including the arc melting furnace (AMF), mechanical alloying, plasma spark sintering, and physical vapor deposition. Recently, there has been significant interest in utilizing additive manufacturing (AM) technologies for HEA production. These technologies allow for the fabrication of complex components with minimal post-processing steps.
A recent article in Materials has stated that the use of Additive Manufacturing (AM) technologies has gained significant attention in recent years for the production of HEAs.
A major technology is the Powder Bed Fusion (PBF) technology, in which a strong energy source, such as an electron beam or a laser, is utilized for scanning each layer of powder, which, in turn, melts the powder and develops the part as per the Computer-Aided Model (CAD) geometry.
Numerous studies on high entropy alloy (HEA) production using Laser Powder Bed Fusion (LASER-PBF) have employed pre-alloy powders. These powders were commercially manufactured through a gas atomization process. A brief list of these alloys, along with their crystal structure, is mentioned in the table below:
Alloy
|
Crystal Structure
|
AlCrFeCoNi
|
BCC/B2
|
Al0.3CrFeCoNi
|
FCC
|
AICrFeCoNi2.1
|
FCC
|
AlCrFeCoNi2.1
|
FCC + BCC/B2
|
AlCrFe2Ni2
|
BCC/B2
|
Al0.55Cr0.5FeNi
|
BCC/B2
|
AlCrFeNiCu
|
BCC/B2
|
AICrFeNi2.5Cu
|
FCC + BCC/B2
|
AlCrFeNi3Cu
|
FCC + BCC/B2
|
Al0.3CrFeCoNiCu
|
FCC
|
AlFeCoNiCu
|
FCC + BCC/B2
|
CrFeC01.1Ni1.6
|
FCC + BCC
|
CrFeCoNi
|
FCC
|
CrMnFeCoNi
|
FCC
|
TiMoTaW
|
BCC + HCP
|
Ti2.3Zr2.3NbMoTa
|
BCC
|
Si0.25Cr0.75MnFe2Co
|
FCC + HCP
|
Table Showing Common HEAs fabricated by L-PBF process and their Crystal Structure Data Source: Additive Manufacturing of High Entropy Alloys (HEAs) Available at: https://doi.org/10.3390/ma16062454
The utilization of additive manufacturing processes involving powder enables the straightforward creation of composite materials with a high entropy alloy (HEA) matrix. These materials can be reinforced through the incorporation of dispersion particles or by adopting a laminated structure. In the case of composite materials with metal alloy matrices, reinforcing particles such as metal carbides, nitrides, borides, and oxides can be effectively employed.
Future Outlook
CALPHAD can quickly screen out alloys that are unsuitable, thus the speed of development can be increased by several orders of magnitude. The thermodynamic properties of the majority of HEAs are still unknown, and much data is still to be identified. Therefore, the development of more multi-component thorough databases is urgently needed.
There is a pressing need for the advancement of computational and machine learning tools to predict multi-component phase diagrams and transport coefficients for high entropy alloys (HEAs).
Special attention should be given to understanding the roles of interstitial elements, such as B, known for their positive impact on interface cohesion in conventional alloys. Additionally, efforts should be directed towards achieving higher precision in predicting phase transformations, as well as understanding low-temperature equilibrium and non-equilibrium phases and microstructure states. This focus is especially crucial for certain HEAs designed for cryogenic applications.
In short, HEAs are essential for various industrial applications. However, certain advancements are needed to ensure the further development of high-entropy alloys, leading to rapid commercialization of HEAs.
More from AZoM: Improving Crack-Resistance Through Innovative Welding Techniques
References and Further Reading
Dierk Raabe, (2023). What are High Entropy Alloys and why are they interesting?. [Online]
Available at: https://www.dierk-raabe.com/high-entropy-alloys-overview/
George, E. et. al. (2019). High-entropy alloys. Nat Rev Mater 4, 515–534. Available at: https://doi.org/10.1038/s41578-019-0121-4
Tsai M-H. (2016). Three Strategies for the Design of Advanced High-Entropy Alloys. Entropy. 18(7):252. Available at: https://doi.org/10.3390/e18070252
Ron T. et. al. (2023). Additive Manufacturing Technologies of High Entropy Alloys (HEA): Review and Prospects. Materials. 16(6):2454. Available at: https://doi.org/10.3390/ma16062454
Disclaimer: The views expressed here are those of the author expressed in their private capacity and do not necessarily represent the views of AZoM.com Limited T/A AZoNetwork the owner and operator of this website. This disclaimer forms part of the Terms and conditions of use of this website.