Apr 29 2009
Saudi Ethylene and Polyethylene Company (SEPC) has successfully started up its Petrochemical Complex in Al-Jubail Industrial City, located in the Kingdom of Saudi Arabia. SEPC, formed in 2006, is a joint venture owned by LyondellBasell Industries (25%) and Tasnee and Sahara Petrochemical Company (75%).
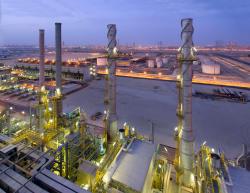
The complex includes facilities that produce:
- 400 KT per year of high density, mulitmodal polyethylene based on LyondellBasell's latest-generation Hostalen ACP process
- 400K KT per year of low density polyethylene based on LyondellBasell's Lupotech T technology
- 1000 KT per year of ethylene
- 285 KT per year of propylene
"Through the combined strengths of both partners, we've created a world-class manufacturing complex with highly competitive feedstock and operating costs in close proximity to our target markets," said Saleh Al-Nazha, President of SEPC. "By using the most advanced PE technologies available in the market, we can manufacture specialty and high-performance products but within a cost structure that can take into account the financial pressures and cyclicality of a commodity market."
"This complex is an important part of our strategy to grow and diversify our feedstock base, which will help us to meet the needs of our customers in Europe, Asia and the Middle East region," explained Manuel Fraga, LyondellBasell's Divisional Vice President for Operations in the Africa and Middle East Region.
Latest state-of-the-art PE technologies
The two polyethylene plants are the largest of their kind in the world, and demonstrate the technology leadership of LyondellBasell as polyolefins licensor.
The Hostalen ACP unit for multimodal HDPE addresses customer needs that are beyond the limits of standard bi-modal HDPE, producing resins with an advanced toughness/stiffness balance, superior impact resistance, higher stress crack resistance and significantly improved processing advantages. The process enables producers to create resins that meet demanding requirements for major HDPE applications ranging from thin-wall packaging to crack-resistant pipe.
The LDPE plant is based on the leading high-pressure tubular reactor process, Lupotech T. The technology offers attractive economics and world-scale capabilities, and has become the benchmark in LDPE manufacturing by providing the lowest operating costs currently in the market, while producing high-performance resins. Additional features of Lupotech T technology include fast start up and grade changes, as well as a high on-stream factor, making it today's technology of choice for the production of LDPE and EVA copolymers.