By Surbhi JainReviewed by Susha Cheriyedath, M.Sc.May 23 2022
In an article recently published in the open-access journal Polymers, researchers discussed the service and wear life of 3D printed polymeric gears.
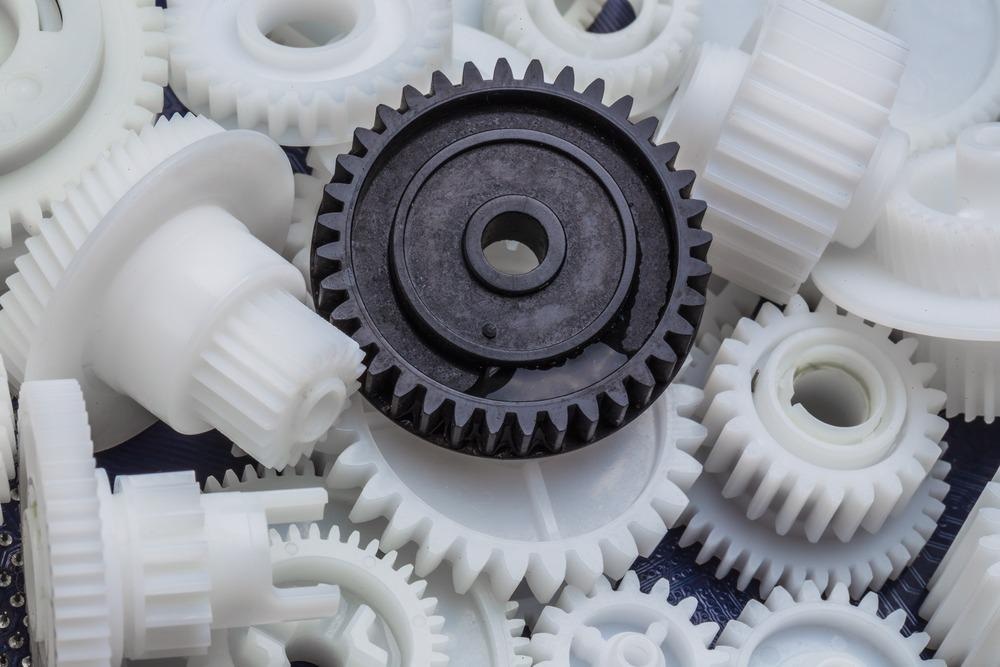
Study: Wear and Service Life of 3-D Printed Polymeric Gears. Image Credit: Zhukov Oleg/Shutterstock.com
Background
In recent years, additive manufacturing has surpassed traditional manufacturing methods in popularity. The most significant downside of additive manufacturing is that it takes longer to produce than traditional manufacturing methods and is not ideal for large production. With a little investment, it is feasible to make goods that have been modeled with a three-dimensional (3D) printer.
Because of their lightness, low cost, corrosion resistance, and silent operation, plastic gears are commonly employed in the electrical, culinary, and textile sectors. The strength of plastic gears printed in three-dimensional printers was investigated by researchers. The mechanical properties of gears created using the 3D printing approach have been investigated both theoretically and empirically under various working situations.
(a) Tooth contact areas and limits (b) load-surface velocity distribution. Image Credit: Mert Safak Tunalioglu and Bekir Volkan Agca, Polymers
About the Study
In this study, the authors calculated the wear resistance of plastic spur gears made using the fused deposition modeling (FDM) method theoretically. Wear tests were performed in the Forschungsstelle für Zahnrader und Getriebebau (FZG) type test equipment at the same load and rotational speeds to assess the service life of gears. Gears were made from thermoplastic polymer materials such as acrylonitrile butadiene styrene (ABS), polylactic acid (PLA), and polyethylene terephthalate (PETG).
The team determined the wear of plastic gears generated by the FDM process in 3D printers theoretically based on the number of rotations. MATLAB® was used to calculate the equation that was used to describe wear along the line of action.
The researchers evaluated the gears' service life by repeating the tests with the same load and rotating speeds. PLA, ABS, and PETG polymeric thermoplastic materials were used, which are often utilized in the FDM process. Plastic gears were printed using a BCN 3D Sigma R19 three-dimensional printer. Wear testing was performed with the FZG closed-circuit wear test instrument to observe the wear on the gears.

The relative movements of point p1 and p2. Image Credit: Mert Safak Tunalioglu and Bekir Volkan Agca, Polymers
Observations
PETG plastic gears were more durable than other types of plastic gears. PETG plastic gears outlasted PLA and ABS by 22.3% and 37%, respectively. PLA gears appeared to be 12% more robust than ABS gears. The wear depths of PETG material gears were 30% and 40% lower than ABS and PLA material gears, respectively.
The most wear was seen in ABS, PLA, and PETG at the theoretically calculated wear depths when the gears rotated at the same load and rotational speeds. In terms of wear, PETG was the most durable material. The root area of the gears was the important place for plastic gears.
The wear depth values computed using the theoretical equation for PLA-fabricated gears differed by 4–5% from the results observed experimentally with the use of CMM. This demonstrated the theoretical equation's use and adaptability to different plastic gears. ABS and PLA were shown to have similar wear characteristics. When all three plastic gear materials were compared, PETG was observed to be on top as the most durable. PETG material was resistant to wear which was related to its high elongation break and rigid but flexible nature.

Polymeric spur gears (a) PLA, (b) ABS, (c) PETG. Image Credit: Mert Safak Tunalioglu and Bekir Volkan Agca, Polymers
Conclusions
In conclusion, this study theoretically determined the equation of wear depth of the plastic gears generated by the proposed FDM method in the 3D printer, and the wear depths along the action line were calculated using the MATLAB® code that was derived. To assess the service life of the gears, the tests were repeated until damage occurred at the same number of revolutions and speed.
Wear was particularly observed in the region of the tooth root where the driving gear entered operation in the plastic gears made by the FDM process. The root area of the gears was the important place for plastic gears.
Due to their differences in quality, three distinct polymeric materials (ABS, PLA, and PETG) were compared in the manufacture of materials using the FDM method in 3D printers. While PLA was the easiest material to work with, ABS was harder the hardest. When it comes to price and availability, all three polymeric materials are marketed as filaments and have similar costs, but in terms of wear resistance, PETG was the clear winner.
The authors mentioned that future research will compare the wear behavior of polymeric gears as made using various 3D printing techniques and printing parameters.
Disclaimer: The views expressed here are those of the author expressed in their private capacity and do not necessarily represent the views of AZoM.com Limited T/A AZoNetwork the owner and operator of this website. This disclaimer forms part of the Terms and conditions of use of this website.
Source:
Mert Safak Tunalioglu and Bekir Volkan Agca. Wear and Service Life of 3-D Printed Polymeric Gears. Polymers 14(10) 2064 (2022). https://www.mdpi.com/2073-4360/14/10/2064