A number of ultra-precision tools include an optical subassembly. These kinds of subassemblies have to be mounted to a flat, rigid, damped surface in order to maintain the positional stability of the optical system.
Until now, engineers had to pick between a honeycomb optical breadboard and a machined aluminum plate. Honeycomb breadboards have the benefit of delivering structural damping coupled with a much higher stiffness-to-weight ratio. Aluminum plates have the benefit of being machined to precision parallelism and flatness as well has tight tolerances on hole positions.
TMC's newest innovation combines the best of both.
The Hybrid Honeycomb™ begins as an aluminum plate. The plate is machined to attain the desired features. The underside is then machined away to leave behind a monolithic honeycomb pattern to lighten the structure. Next, a bottom skin is epoxied over the honeycomb cells, closing the structure and offering extra stiffness and damping. The Hybrid Honeycomb™ is ideal for optical subassemblies in photonics tools and applications, and is an engineered solution that is configured to user’s unique requirements.
The TMC Advantage
- The machined, monolithic aluminum panel guarantees parallelism and precision flatness, and thus hole tolerance can be attained.
- Comparable tolerance to machined aluminum plates
- Epoxy bonded face sheet seals honeycomb core and offers extra damping and stiffness
- Honeycomb core machined from solid aluminum plate
- Dimensional precision of the machined aluminum plate with the damping and high stiffness-to-mass ratio of the honeycomb breadboard
Specifications
- Top plate: Machined aluminum
- Core: Integral to the top plate. Cells machined from a monolithic structure
- Finish: Clear or black anodize
- Bottom plate: Machined aluminum
- Holes: Sealed through the process of machining blind holes
- Hole pattern: M6 on 25 mm, ¼-20 on 1” centers or custom
Performance
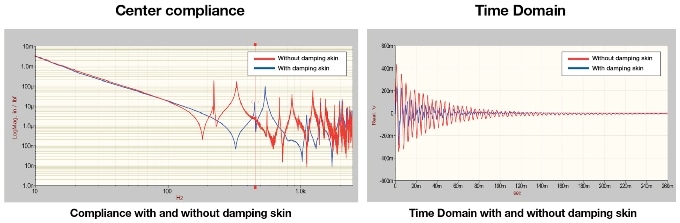