For users requiring specific post-processing functions, or looking to print large parts with one or more materials for small series or production, the modular and scalable MetalFAB1 architecture enables configurations from 2 to 11 modules and guarantees maximum flexibility.
When users’ capacity requirements increase, they can add additional modules in the future. They can also improve the MetalFAB1’s print parameter settings for certain part qualification.
The MetalFAB1 Prints with Lowest Cost per Part
The MetalFAB1 has automated the manual steps of traditional powder bed fusion (PBF) printers to guarantee maximum productivity, leading to the lowest cost for each printed part. The process is fully automated, reducing human errors and increasing reproducibility. For new customers, Additive Industries assesses a cost per part business case.
The MetalFAB1 Prints the Highest Quality Parts
For industrial-quality production, the MetalFAB1’s part reproducibility is ensured through robust machine design combined with sophisticated laser calibration technology. This can be programed in advance to automatically run at given intervals. Scripted process controls, part build simulation, and in-process quality monitoring are combined to achieve predictability.
Customers are Partners
Additive Industries provides excellent service to increase the overall equipment efficiency of the MetalFAB1. A continuous open dialogue with Additive Industries’ customers drives the technology roadmap for constant enhancement.
MetalFAB1 Modules
Configuration of the MetalFAB1 system can be done by including a number of optional modules that automate post-processing or extend productivity. Additive Industries constantly enhances the system by adding functionality, which safeguards customers’ investment against obsolescence.
MetalFAB1 Flexible Configurations
Around 4 AM Cores with one to four lasers, exchange module, storage module, product removal module, and heat treatment module are included.
Software
The software includes the Additive World Platform Software and the Additive Industries Build Processor, compatible with Materialise Magics, 3D Systems 3DXpert, and Autodesk Netfabb.
MetalFAB1 Supporting Tools
Powder management tool and build plate handling tool.
Specifications of MetalFAB1 System
. |
. |
Process type: |
Metal Laser Beam Powder Bed Fusion (LB-PBF) |
Net build envelope: |
420 x 420 x 400 [mm] (16.5 x 16.5 x 15.7 [In]) |
Laser: |
Yb fiber lasers 500 W |
Number of Lasers: |
1 to 4 full field, preventing laser overlap regions |
Configurability: |
Configure up to 11 modules for more productivity or post-processing automation |
Build plate: |
Automated leveling and positioning |
Recoater: |
Polymer style with automated first layer technology |
Powder handling: |
Automated extraction, sieving and recycling during the build cycle |
Minimum autonomous operation: |
112 [hrs], maximum 8 build jobs |
Productivity: |
Up to 1.000 dm3/y (with 4 lasers, depending on material) |
Accuracy: |
< | 0.050 0.002 x part length | [mm] |
Reproducibility: |
< | 0.050 | [mm] |
Layer Thickness: |
20-100 um |
Optical calibrations: |
In-line, automated, laser-2-laser |
Safety: |
Safe chalk filter system |
Storage positions: |
8 empty build plates |
Job preparation: |
Off line build set up and routine cleaning and maintenance |
Remote access & monitoring: |
Continuous video feed through Additive World Platform |
Materials |
All LB-PBF materials supported, including Ti6Al4V (grades5,23), C360.0 AlSi10Mg, 1.4404 (316L), UNS N07718 (IN718), Scalmalloy©, 1.2709 (Maraging Steel) |
Quality control |
PrintRite 3D process monitoring by SigmaLabs |
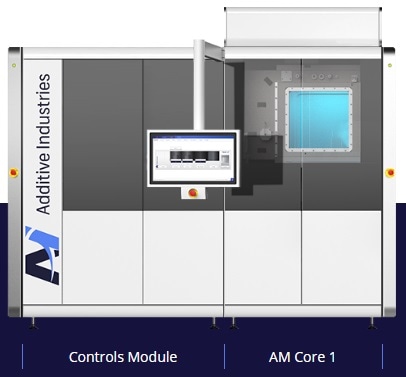