The instruments in the high-force Eplexor® series provide static and additional dynamic force levels from maximum ± 2000 N to maximum ± 4000 N, and are considered the ideal choice for analyzing the dynamic-mechanical (or only static) properties of firm samples as well as of specimens with more significant dimensions—even component parts.
As a result of their modular design, high-force DMA instruments could house add-ons to perform tests on properties such as heat build-up, fatigue, blow-out, and rolling resistance.
All testing machines present in this series are dependent on the following standards:
- DIN 53513
- DIN 53533
- ISO 6721/1
- ISO 6721/4
- ISO 6721/5
- ISO 6721/6
- ISO 4664
- ISO 4666/3
- ISO 4666/4
- ASTM D623
- ASTM D4065
- ASTM D4473
The following high-force DMA instruments are available:
Source: NETZSCH-Gerätebau GmbH
Instrument Type |
Max. Static Force |
Max. Dynamic Force |
DMA 523 Eplexor® (2000 N) |
6000 N |
± 2000 N |
DMA 523 Eplexor® (4000N) |
6000 N |
± 4000 N |
DMA 523 Eplexor high-force series
Video Credit: NETZSCH-Gerätebau GmbH
Set for the Future
The DMA Eplexor® series enables simple upgrades to the fundamental instruments with an extensive range of extra options or accessories. Force sensors can be exchanged.
Unsurpassed Flexibility
With the suitable hardware and software add-ons (which can also be retrofitted), the DMA 523 Eplexor® can be transformed into, for example, a Goodrich flexometer (ASTM D623), an instrument for high-temperature application or a 24/7 system with automatic sample changer.
Non-Stop Operation with the Second-to-None NETZSCH Autosampling Systems
By adding one of the two available autosampling systems (ASC–automatic sample changer or MPAS—multi-purpose automatic sample changer), any DMA Eplexor® could be transformed into a completely automatic testing system for up to 160 samples.
This assists tension, bending, shear, and compression modes. The peerless MPAS even streamlines the insertion of sample holders in arbitrary order.
Designed to Investigate Highly Stiff Materials
Depending on a separation between the static and the dynamic drive jointly with blade springs, complete force levels of up to 16000 N (static + dynamic) could be employed in the sample, thereby allowing improved conditions for studying metals, composites, or ceramics.
Maximum Safety During Fatigue and Tensile Tests
The electrodynamic shaker needs efficient shock absorption since fatigue or tensile tests at the highest force levels are typically destructive experiments. This is guaranteed by the special blade spring system featured in NETZSCH instruments.
Highly Economic LN2 Cooling
Improved cooling control enables low liquid nitrogen consumption while functioning at sub-ambient temperatures.
The Future is Now
Bring the devices into the laboratory with a click of a button.
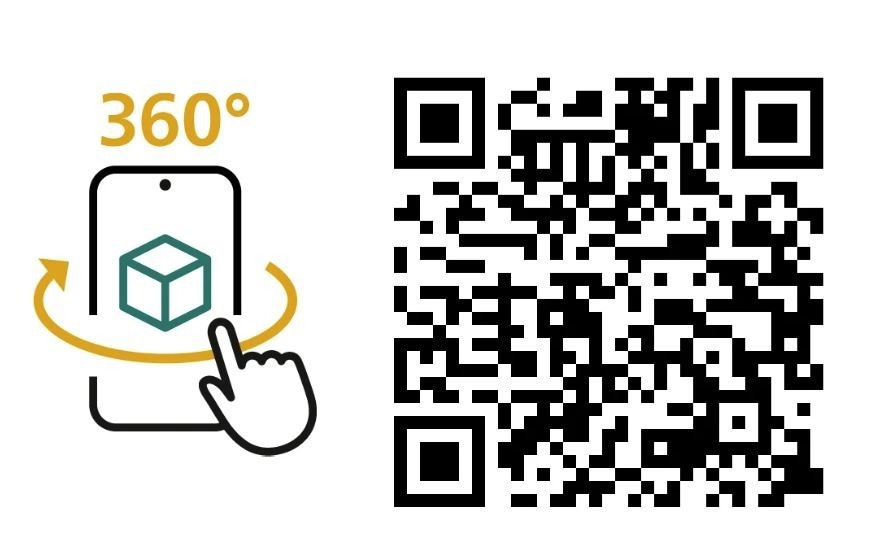
Image Credit: NETZSCH-Gerätebau GmbH
Users scan the QR code to receive a 3D model of the instrument directly on their tablet or mobile phone. With the help of the new artificial reality (AR) technology available, the 3D model could easily be positioned in users’ laboratories in its original life-size. This function is browser-based and requires no app.
Technical Data
Temperature range: ranges between −160 °C and 500 °C
Static force: 6000 N
Frequency range: 0.0001 Hz to 100 Hz
Dynamic force range: ±2000 N, ±4000 N (based on instrument type; see table)
Force sensor: interchangeable; nominal forces come up to 12000 N
Blade springs: To compensate for high static forces and for expanding the operation range
Static displacement: max. 70 mm
Dynamic displacement: Comes up to ± 15 mm (DMA 523 Eplexor® 2000N/4000N); every instrument could be fitted with two strain transducers.
Additional measuring modes: Creep, relaxation, curing, heat build-up, fatigue, tensile tests
Automatic sample length/thickness determination: in tension, compression and bending geometry
Automatic sample changer: Maximum of 160 samples of the same geometry (ASC), also for varying sample holder geometries (MPAS)
The instrument enables measurements up to 10000 N.
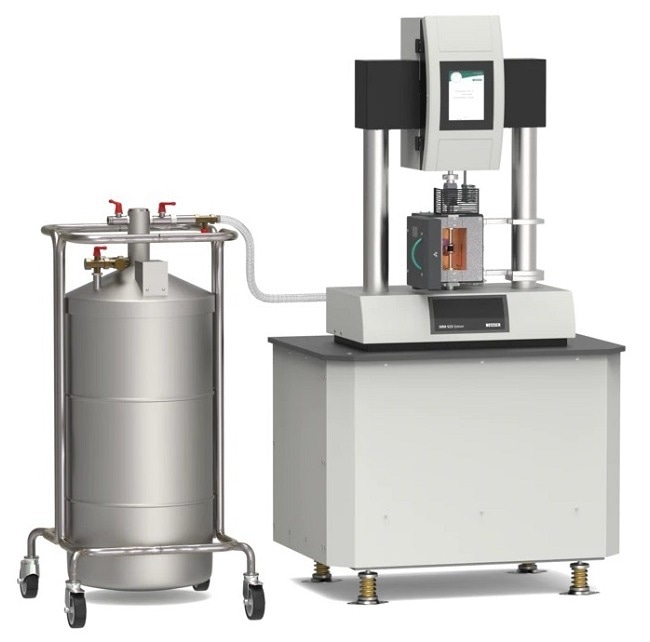
Image Credit: NETZSCH-Gerätebau GmbH
Software
The technologically advanced DMA GABO Eplexor® 8 software is an ideal match for the DMA instrument. The software depends on the Windows™ operating system and provides extensive chances for data and curve analyses.
Predefined software packages align with the chosen clamping devices like tension, bending, or compression.
The software features are:
- Frequency sweep (0.01 to 100 Hz; optional 200 Hz; optional 0.0001 Hz; also optional: multi-frequency sweep)
- Temperature sweep
- Static and dynamic stress or strain sweep available
- Time sweep
- Temperature and frequency sweep—Isothermal frequency varies (temperature steps)
- Constant stress amplitude mode per ASTM D623 (heat build-up test along with static load and dynamic deformation—optional)
- Time-temperature superposition—TTS (WLF, Arrhenius, numeric—optional)
- Universal test driven by the servo motor (optional) or by the shaker (optional)
- Evaluation of complicated modulus (E, G), storage modulus (E’, G’), loss modulus (E", G), damping factor (tand), glass transition temperature, and optional creep, relaxation and retardation, energy loss, fatigue, Payne or Mullins effect analysis and crack growth testing
- Prediction of the rolling resistance of tires (optional)
- Hysteresis presentation of outcomes (optional)
- Identification of thermal expansion (for tension mode-optional)