A new study has investigated the fabrication of parts constructed from ceramic materials using robocasting. Published in the journal Materials, the study has been carried out by researchers from Germany.
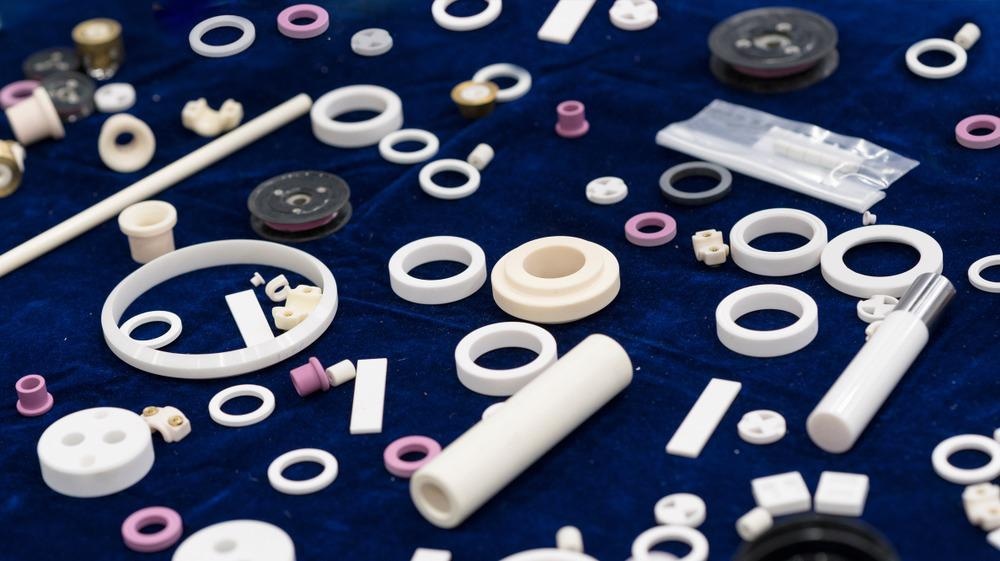
Study: Reorientation of Suspended Ceramic Particles in Robocasted Green Filaments during Drying. Image Credit: Aumm graphixphoto/Shutterstock.com
What is Robocasting?
Robocasting is a type of additive manufacturing technology. Additive manufacturing, otherwise known as 3D printing, has revolutionized several industries, providing innovative solutions for sectors such as manufacturing, biomedicine, tissue engineering, aerospace, and electronics.
Robocasting is a form of extrusion-based printing which is used to deposit ceramic slurries layer by layer to construct devices and components. Continuous, rod-like filaments are produced from a paste that contains suspended micro-sized ceramic particles. After the paste has been extruded, the filaments are subjected to drying and sintering steps. Drying steps are performed at room temperature using natural convection.
Slurries used in robocasting techniques must meet three criteria: they must possess adequate pseudo-plasticity, upon dispensing they must form a non-flowable mass, and they must be able to form defect-free layers in order to form a uniform mass.
Overview figure of the scope of this work. The figure shows an illustration of the robocasting process that extrudes a ceramic filament. A zoom shows the microstructure in the wet filament that is usually predicted using numerical simulation or analytical models. After printing, the carrier fluid evaporates, during which the particle orientation changes (second microstructure), yielding the microstructure that can be measured in the experiment. Image Credit: Dietemann, B et al., Materials
The Importance of Particle Orientation
Within the final processed filaments, particle orientation is an important characteristic as it influences the printed product’s material properties. Predicting this orientation has therefore become a focus of research interest in recent years. Much research has been performed using analytical orientation prediction models and microscopic simulations to predict particle orientation within wet filaments, but there is a lack of knowledge on particle reorientation during the drying step.
Particle orientation can only be measured after the sintering step, meaning that it is difficult to elucidate information on the particle reorientation during drying. Before this, the liquid phase must be removed, making experimental measurements of particle orientation in the wet filament highly difficult.
The Study
To address the problems faced by researchers trying to quantify particle reorientation, the researchers of this study quantified this characteristic by using numerical simulations. The authors used the discrete element method, as it satisfies several requirements.
This method can precisely resolve the exact particle geometry, interactions between particles can be described more effectively, the initial orientation of the particles can be set according to analytical models for the extrusion step and their predictions, and the composition of the paste can be accurately reproduced. Moreover, capillary laws are governed by specific macroscopic force laws. This is due to the drying phase possessing the remaining fluid phases.
The robocasted green filaments used in the research were composed of sphere- and platelet-like particles. The average maximum reorientation displayed by the particles was ± 5o. The authors highlighted that conventional analytical orientation prediction models do not typically include particle reorientation during the drying phase and are commonly applied during the extrusion phase when the filaments are still wet. It is applied during the extrusion phase to reliably predict mean orientation based on deformation.
It was the opinion of the authors that the drying phase should continue to be neglected in these analytical models since, during extrusion, reorientation is significantly larger than during the drying phase. As long as the particles experience significant deformation, orientation can be accurately predicted using orientation prediction models. Additionally, the authors demonstrated that filament diameter had no influence on particle reorientation.
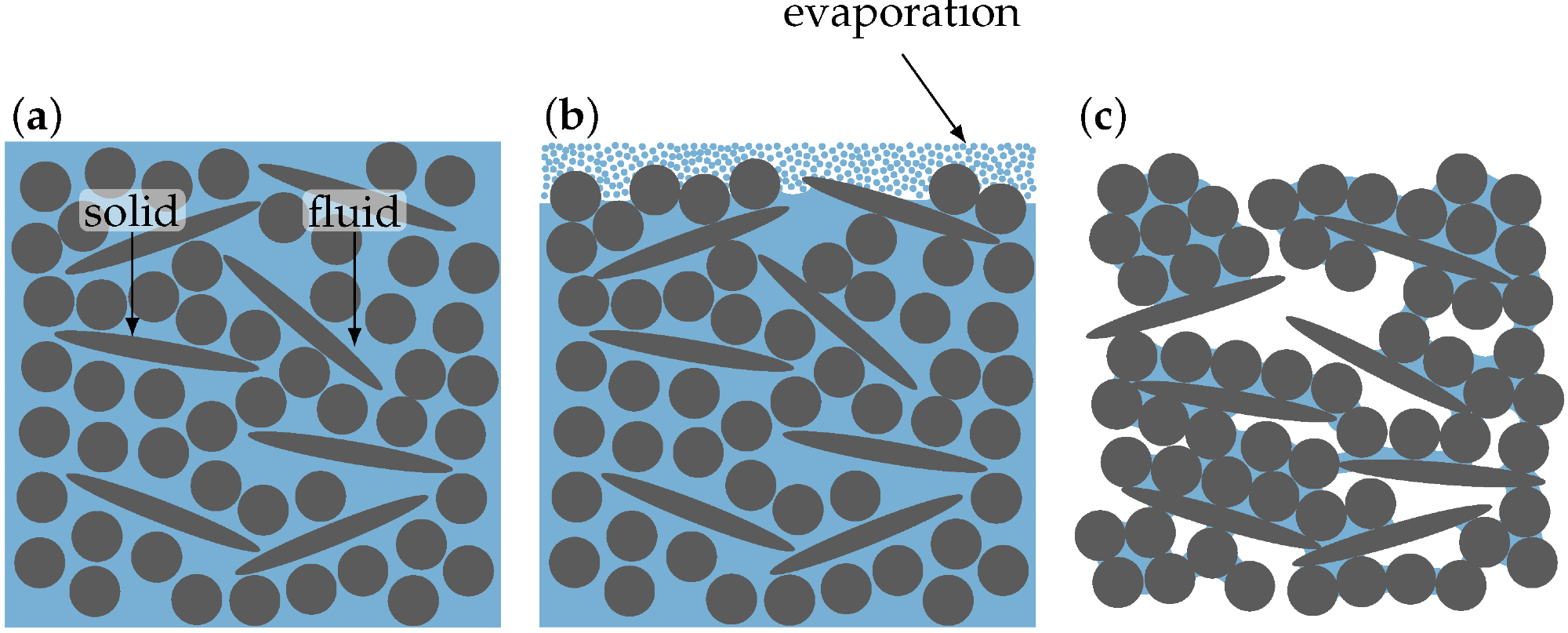
Illustration of the drying cell strategy. (a) shows the particle configuration in the wet filament as produced by the printing process. During the first stage of drying (b,c), most of the water evaporates and the particles change their orientation. Image Credit: Dietemann, B et al., Materials
Further Research and Limitations of the Study
The research has identified at least two subjects that warrant further research. Firstly, during the falling rate period, which is the second drying phase (which is largely unconsidered) stress can be induced in the filament which can lead to cracking. This is due to the evaporation of remaining fluid and avoiding this is crucial for final product design. The authors are currently unaware of research that adequately addresses this phenomenon.
Secondly, future studies should adequately quantify the sintering step for the present system. Sintering is the phase during which the product gains its strength. During sintering, there is a further reduction in volume, with the potential for further reorientation. Elucidating information on this step will further add to the knowledge on particle reorientation during the entire process of robocasting green ceramic filaments.
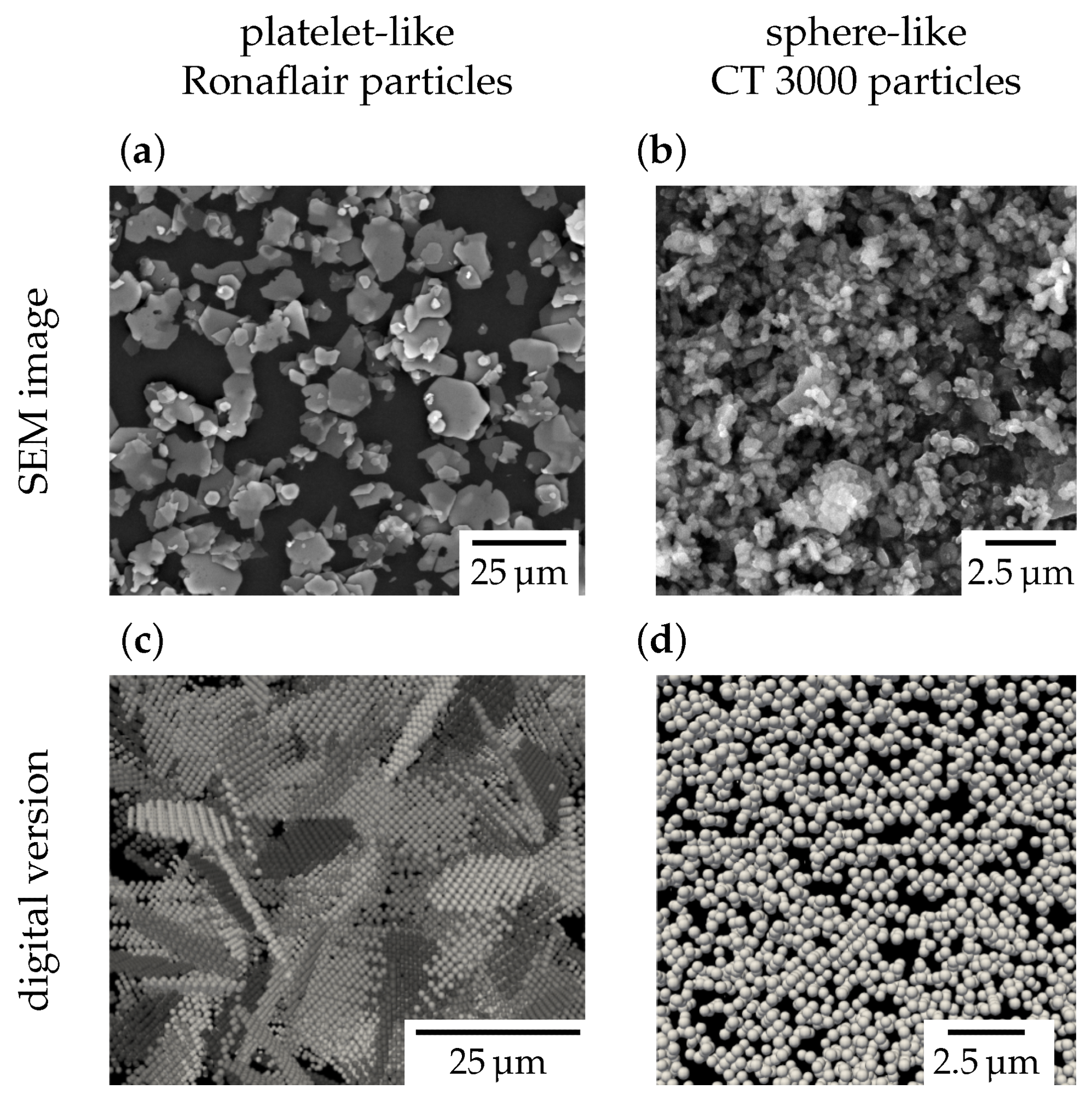
The Ronaflair (a) and CT 3000 particle systems (b) as observed by SEM images and as represented in the numerical simulation (c,d). Image Credit: Dietemann, B et al., Materials
Whilst the study provides useful information on particle reorientation during the drying phase, the authors have identified limitations with their work. Electrostatic contributions were neglected as the authors studied uncharged ceramic particles. Secondly, the composition of the extruded ceramics included significantly smaller spheres than platelets. The dynamics of ceramic slurries with larger spheres may be different.
Thirdly, the authors assumed that kinetics during the drying phase can be neglected, with no effect caused by particle inertia. This means that the results of the study cannot be compared with systems that possess fast-drying kinetics. Furthermore, due to the micrometer scale particles which were embedded in a system with a high filling fraction, Brownian motion was neglected. This means that the results cannot be compared with systems that possess nanometer-sized particles, which are significantly affected by Brownian motion.
Further Reading
Dietemann, B et al. (2022) Reorientation of Suspended Ceramic Particles in Robocasted Green Filaments during Drying [online] Materials 15(6) 2100 | mdpi.com. Available at: https://www.mdpi.com/1996-1944/15/6/2100
Disclaimer: The views expressed here are those of the author expressed in their private capacity and do not necessarily represent the views of AZoM.com Limited T/A AZoNetwork the owner and operator of this website. This disclaimer forms part of the Terms and conditions of use of this website.